Rockwell Automation 873P Programmable Ultrasonic Sensors User Manual
Page 4
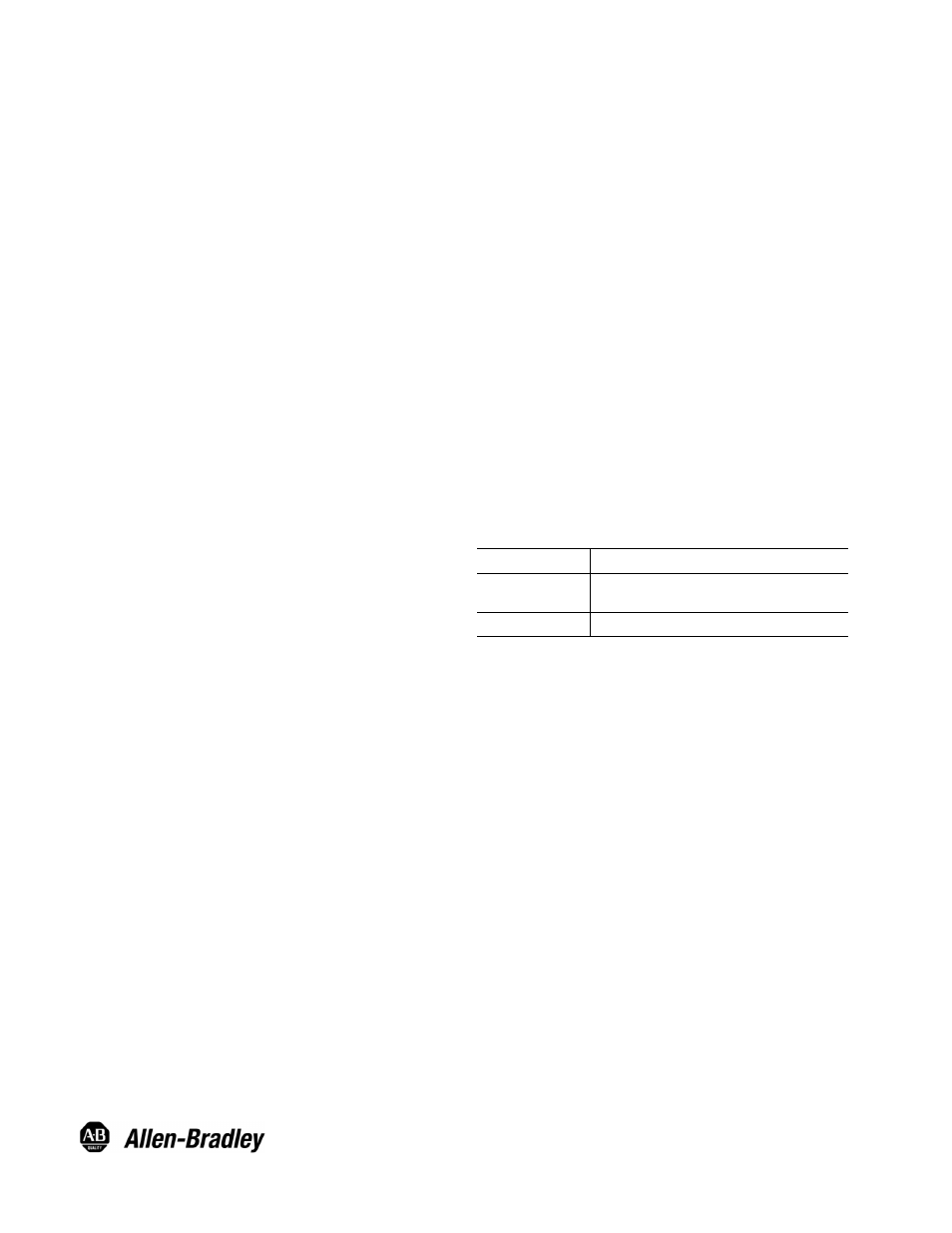
4
Target Considerations
Since the actual sensing distance to an object depends on
a reflected sound wave, target material, shape, size,
temperature, and position will influence operation; it is
possible that the sensing distance can be reduced or the
target may not be detected based on these characteristics.
The ideal target is a smooth, flat surface. Target material
that is not relatively sound reflective (fabric, foam rubber,
etc.) may be difficult to detect depending on the application.
Rounded or uneven objects can also be detected, but the
sensing distance may be reduced. For best performance,
the sensor should be aligned such that the sensor face is
parallel to the target surface.
Environmental Factors
The velocity of sound in air is dependent upon temperature
(sound waves travel faster at higher temperatures). Bulletin
873P ultrasonic sensors have internal temperature
compensation to adjust the ultrasonic frequency to
compensate for these changes in the ambient air
temperature. However, while this feature does compensate
for ambient temperature changes, temperature variations
within the sensing range due to convection currents,
heating/cooling elements, etc., may still divert or refract the
sound wave and adversely affect sensor performance.
Strong air turbulence can also influence the signal and
adversely affect the stability and overall sensor operation.
Humidity does not significantly affect ultrasonic sensor
operation, but changes in humidity can have a slight affect
in some instances due to the absorption of sound.
Mounting Considerations
The sensor must be securely mounted on a firm stable
surface or support. A mounting configuration that is
unstable or subject to excessive vibration may cause
intermittent operation.
A mounting location should be chosen such that the sensor
faces directly toward the target’s surface (perpendicular to
the barrel axis of the sensor).
When using more than one 873P there is a potential for
cross-talk (mutual interference) between the sensors. As a
result, consideration should be given to the sensor spacing.
See the beam pattern chart for the minimum acceptable
distance between sensors that are mounted side by side.
When the sensors must be mounted facing each other they
should be separated by a distance at least four times the
maximum sensing range for the model.
Background Suppression
The setpoint limits for the programmable sensor models
can be set up to detect a target in a defined range within
the sensor specifications. This includes the capability to
ignore all objects beyond a specified distance (background
suppression). The far limit of the sensing range can be
adjusted to detect valid targets and ignore background
targets such as the side of a conveyor.
Profile Reduction Beam Deflectors
Beam deflectors are available to reduce the mounting
profile for applications that cannot accommodate the barrel
length of the sensor. They can also be used to protect the
sensor face from target collisions. These accessories
deflect the ultrasonic beam at 90_ and are available in
plastic and stainless steel versions. In addition to the profile
reduction, the stainless steel models provide mounting
capability and also focus the ultrasonic beam.
Catalog Number
Description
60- 2758
Stainless Steel beam deflector and mounting bracket
for 30mm models
60- 2760
Plastic beam deflector for 30mm models
Stilling Tubes
For applications where the target may be a liquid with a
turbulent surface, a stilling tube can be used to diminish this
instability. The tube should have a smooth inner diameter
and its size should be a minimum of 50mm depending on
the application. The sensor should be mounted such that
the barrel is parallel to the sides of the tube but not
touching.
Publication 75009--191--01(A)
December 2002
Printed in USA