Installation, Continued), 45 and dynamic brake terminals a1 – Rockwell Automation 1397 NEMA Type 1 Brake Installation Inst. User Manual
Page 4: ❐ 5 remove the jumper between terminals 3, 4 and dynamic brake terminals 1, 2, 3
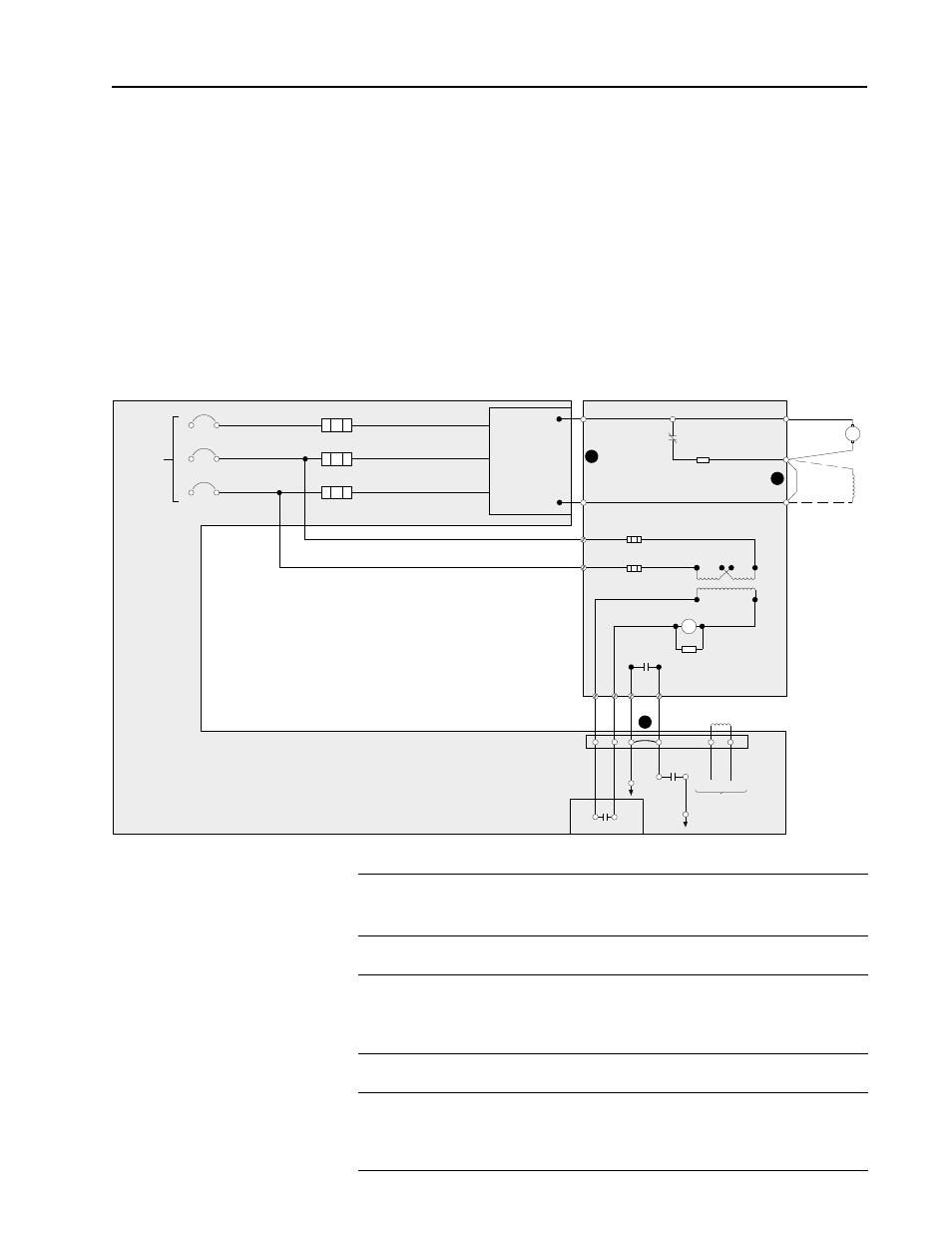
1397 NEMA Type 1 Dynamic Brake
4
1397-5.14 March, 1997
Installation
(continued)
181/L1
81
1FU
A1
DB
45
A1
A1
A1
A2
S1
S2
S2
A2/S1
DB
DB
45
1
2
3
13
14
3
2
4
F1
F2
1
P6-5
P6-2
P5-5
P5-6
35-F2
37-F1
DBCR
13
FROM
FIELD
SUPPLY
14
FAN
AUX
4
ARMATURE
SUPPLY
1397 DRIVE
DYNAMIC BRAKE KIT
DYNAMIC BRAKE TERMINAL BLOCK
2FU
282
281
16FU
(H1) (H3) (H2)
(H4)
(X1)
115V AC
2SS R
DB AUX
(X2)
182A
182
17FU 183A
183
3FU
283
230/460V AC
50/60Hz
AC
INPUT
82
83
182/L2
183/L3
MOTOR SHUNT FIELD
4
3
5
RESISTOR
❐
4
If the motor has S1 & S2 field leads, remove the S1 & S2 jumper from
the brakes’ power terminal block and connect the motor series leads
to their respective terminals.
❐
3
Follow the wiring diagram above and connect user supplied leads
between drive terminals A1
&
45 and dynamic brake terminals A1
&
45.
❐
5
Remove the jumper between terminals 3
&
4 at the drive terminal block
and connect user supplied leads between drive terminals 1, 2, 3
&
4
and dynamic brake terminals 1, 2, 3
&
4.
Operation
Dynamic braking slows down a rotating DC motor and its load. It is an
"uncontrolled" process. During dynamic braking, the motor armature is
disconnected from the drive. A resistor is placed across the motor’s rotating
armature (now acting as a generator), and the resulting current causes braking
torque in the motor. The motor will decelerate, even with a drive failure, as
long as motor field excitation is maintained.
The drive must have the DC contactor open for dynamic braking to occur.
Dynamic Braking is typically initiated with a Coast/DB stop command or a
drive fault. Under drive fault conditions, the DC contactor opens and applies
the dynamic braking grid across the armature for a dynamic braking stop.