S&S Cycle Bore Big Twin Stroker Kit 1936–1999 3 7/16 - 3 1/2 User Manual
Page 9
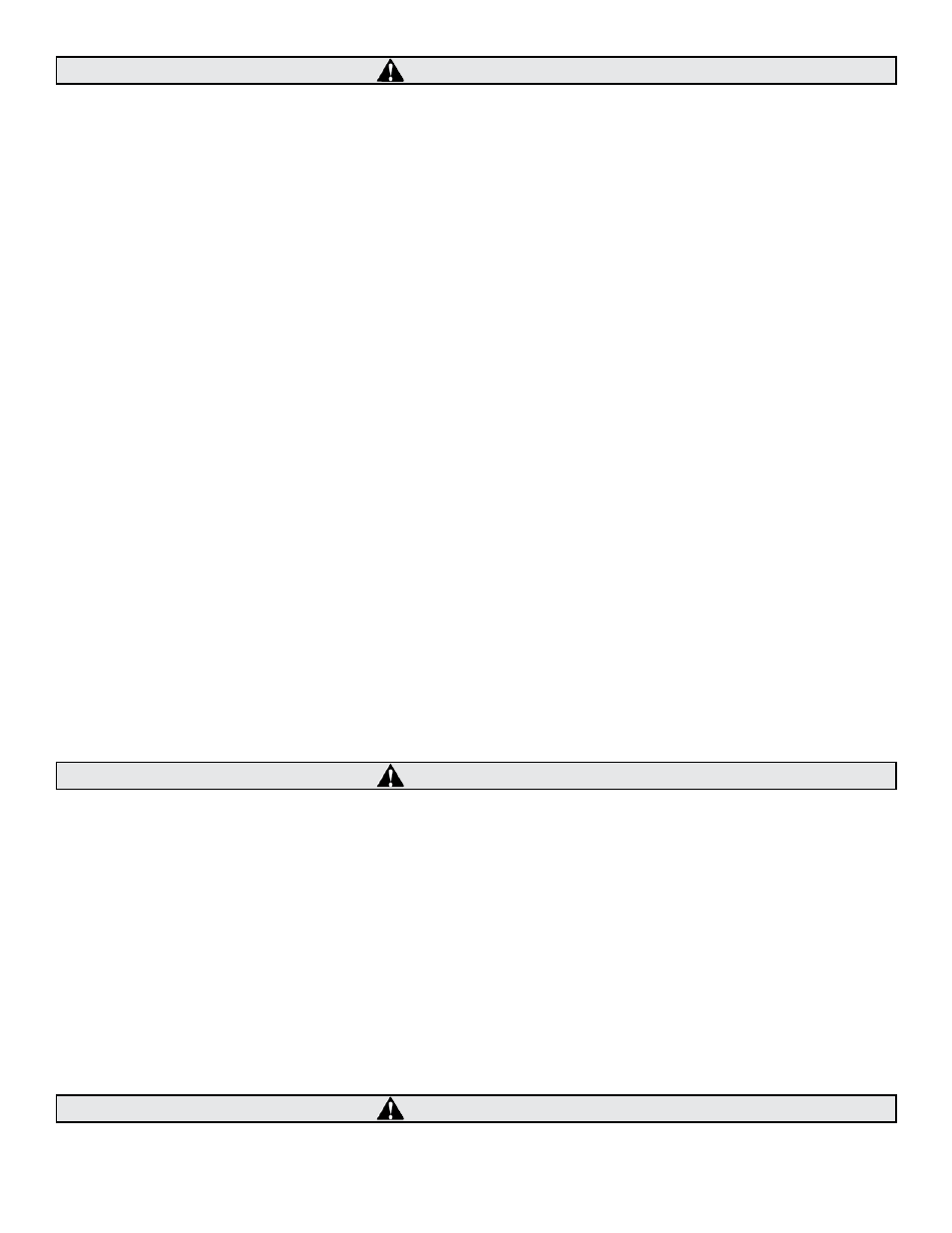
9
Use of spiral-loc type wristpin retainers with wristpins with beveled ends could result in wristpin retainer failure and major damage to engine.
PTFE wristpin buttons must only be used in pistons where buttons are fully supported by wristpin hole. They are used in place of and not in
conjunction with conventional wristpin retaining clips. Recommended wristpin endplay is .010" to .060" and is determined by subtracting
length of wristpin with a button on each end from finished cylinder bore. To make fitting easier S&S® buttons come in two widths for stock
bore applications. “A” buttons are thinner and “B” buttons are thicker. Use two A buttons, PN 94-9251, for bore sizes 37/16" std. to 37/16" +.040,
two B buttons, PN 94-9252, for bore sizes 37/16" +.050 to 37/16"+ .090.
Ring Installation
1. Piston ring widths have changed on some piston series from time to time. It is recommended that ring parts supplied with pistons be
recorded for future reference in the event replacement rings are required.
2. Oil rings are three piece circumferential expander cylinder type. End gap on all rails except those for V2s with 31⁄2" (37⁄16" +.060) bore is .010"
to .040". On V2s with 31⁄2" bore it is .015" to .065" Grind end gaps as necessary. Do not leave burrs as they will scratch cylinder walls. Do not
shorten expander for any reason. Place end gaps as follows: Expander – gap in center of thrust face 90° to wristpin. Bottom rail – gap 2" to
right of expander gap. Top rail – gap 2" to left of expander gap.
3. Compression rings may be cast iron type, chrome faced cast iron type, moly faced cast type and chrome type. The most common
combinations supplied are two chrome faced cast, one chrome faced cast and one cast iron, and one moly faced cast and one cast iron.
Chrome faced or moly faced ring always goes in top groove. Cast iron type usually goes in second groove. Cast iron type is usually a reverse
torsion style ring distinguished by an inside diameter bevel on one side of ring with a “dot” or oversize mark on other side of ring. If two cast
iron compression rings are supplied in set, check to see if one is reverse torsion style ring. Reverse torsion style ring always goes in second
groove. The following rules apply to compression ring identification and placement. Rules are listed in order of priority.
a. Chrome or moly ring goes in top groove.
b. Cast iron regular or reverse torsion goes in second groove.
c. Any identifying “pip” marks, dots or oversize marks go to top of piston.
d. One dot goes in top groove, two dots go in second groove.
e. If both have one dot or two dots, they can go in either groove.
f. If ring has dots and inside diameter bevel, dots go to top of piston.
g. If ring has no dots and inside diameter bevel, bevel goes to top of piston.
h. If ring has not dots, etc. and no bevel, it can go either way.
End gap on all compression rings except V2s with 31⁄2" bore is .012" to .030”. On V2s with 31⁄2" bore end gap is .008" to .030". In certain
instances, the next oversize ringset may be supplied with pistons, ie. + .060" oversize rings with +.050" pistons. This is permissible but end
gaps must be filed. Place end gaps on all compression rings as follows: Second groove – 3" to right of oil expander gap. Top groove – gap 3"
to left of oil expander gap.
4. When rings are compressed for piston installation in bore, be sure oil ring expander ends do not overlap and ring stays assembled
properly.
FINAL ASSEMBLY
To avoid parts damage and obtain accurate torque readings, clean head bolt threads thoroughly before installation. For knuckleheads,
panheads or shovelheads, head bolt threads and area of bolt head that contacts washer (if applicable) or cylinder must then be lubricated
with Permatex® anti-seize lubricant or similar anti-seize compound. S&S has received reports of thread damage in these engines
associated with use of engine oil to lubricate head bolts. Use of clean engine oil is preferred for installation of V2 style headbolts in
Evolution™ engines.
A. Install and tighten cylinders, cylinder heads and manifold as in standard assembly.
NOTE: Retighten cylinder base nuts and head bolts as necessary after engine has been run.
B. Install engine in frame and check for engine to frame and/or gas tank contact.
NOTE: Engine with longer cylinders than stock due to cylinder base plates may contact rigid mount frame and/or right gas tank with rear rocker box. S&S
recommends there be .060" minimum clearance between engine and other chassis components on rigid frame installations. Rubber mount chassis have
adequate room for any engine combination. Up to .060" or .070" may be ground from rocker box cover in some areas for clearance. Additional material
may be sparingly removed from frame if rocker cover clearancing is inadequate.
Excessive material removed from rocker cover may damage cover causing oil leaks.
CAUTION
CAUTION
CAUTION