S&S Cycle Bore Big Twin Stroker Kit 1936–1999 3 7/16 - 3 1/2 User Manual
Page 18
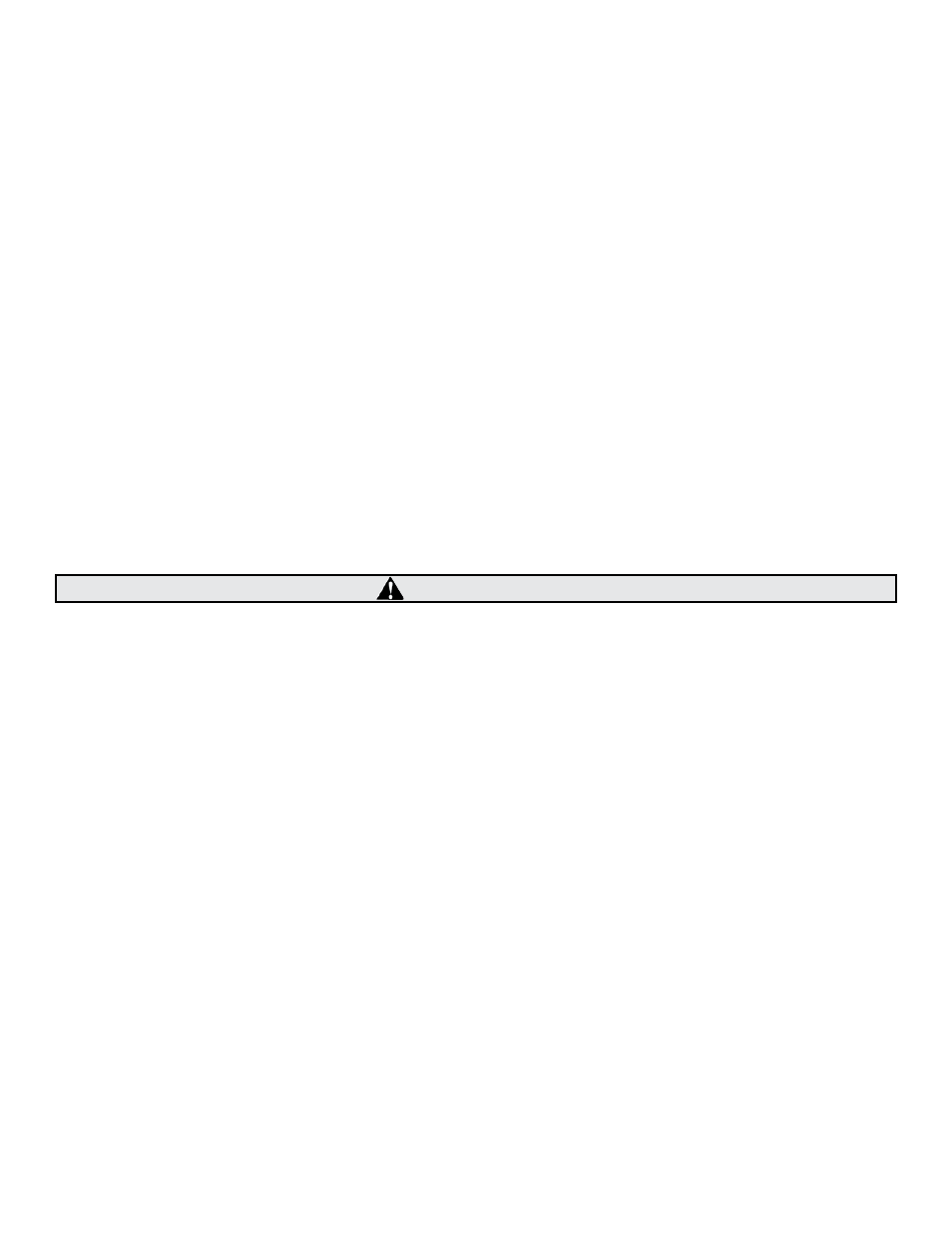
18
NOTE: This procedure increases area that air and oil have to pass from breather gear cavity to gear side.
5. Cam, Lifters and Tappet Blocks (All)
NOTEs:
•
Big inch, stroked H-D® engines with compression ratios of 81⁄2+ to 1 or more respond well to higher lift, longer duration cams. Engines with lower
compression ratios should have shorter duration cams. S&S® offers cams for all big twins except knuckleheads that we have run in our test engines. We
recommend their use along with S&S high performance valve springs and retainers. These components along with other valve train parts are available
in kits that not only satisfy most any degree of rebuilding required but also make valve spring spacing and high lift cam installation an easy job. If you
are using a high lift camshaft perform any required head work and valve spring spacing per manufacturer’s instructions.
•
Knucklehead strokers built using 1936 to ‘47 cases may use any aftermarket knuckle cam such as an Andrews “S” or “K” grind. Knuckleheads installed
on later crankcases, 1948 and up, should use cams such as “575” Sifton. In panhead or shovelhead 575’s lift is much higher, but when used with Knuckle
heads, lift is only .400” since knucklehead rocker arm ratio is 1 to 1. S&S Strokers for Evolution™ engines have been tested using both solid lifters and
hydraulics. We recommend using S&S hydraulic assemblies in all V2® applications. Late-style hydraulic lifters are far superior to early style panhead/
shovelhead assemblies and hold up extremely well under most conditions. To maximize efficiency and reduce potential valve float in high rpm
situations, S&S HL2T hydraulic lifter limited travel kit should be used in all V2 performance applications. PN 33-5338 for 1985 and PN 33-5339 for 1986
and later.
•
Panhead, 1953 and later, and shovelhead strokers with solid lifters should have tappet block hydraulic lifter oil feel holes plugged to prevent excess oil
escaping above lifters from filling pushrod tubes causing potential oil leaks.
To do this, perform following steps:
A. Starting at gasket surface end of oil feed passageway in tappet block base, thread 8-32 tap into oil passage hole. Turn tap until tap end just
starts to enter cam follower hole.
B. Screw 8-32 x 3⁄16" allenhead set screw in passageway until it stops.
C. Perform steps A and B to other tappet block.
NOTE: If hydraulic lifters are ever reinstalled, plugs must be removed.
Restricted oil flow to hydraulic lifter assemblies causes lifters to operate with improper oil pressure which may damage them or other
valve train components.
6.
Piston to Valve Clearancing (All)
NOTEs:
•
All valve spring spacing, rocker arm to collar and rocker arm to rocker cover clearancing must be done before piston to valve clearancing can be
checked.
•
S&S pistons have sufficient valve clearance when used with most street high performance cams with lifts up to .525". However, we recommend that
valve clearancing be checked if other than stock cam is used.
Check piston to valve clearance in following manner:
A. Assemble engine with exception of cylinder heads.
B. Turn engine over until piston in front cylinder is at top dead center. Paint area around valve pockets on pistons with machinist’s blue.
C. Place valves in cylinder head leaving off springs and retainers. Place head on cylinder and secure with one bolt.
D. Lower valves until they contact piston. Rotate valve marking painted area.
E. Remove head and check points of contact. Valve should fit in recessed area machined in piston dome.
NOTE: s&s REcOMMENds AT LEAsT .060" cLEARANcE AROuNd PERIPhERY OF VALVE.
F. If insufficient clearance exists, remove piston and grind valve pocket until head of valve fits flush with proper clearance.
G. Repeat procedure for other cylinder head.
H. Spread layer of putty into valve pockets in both pistons.
I. Assemble cylinder heads and bolt assemblies on cylinders with head gaskets in place. Install pushrods and adjust to simulate final
assembly.
J. Turn engine over in normal direction of travel two complete revolutions.
K. Disassemble engine and check thickness of putty in valve pockets.
NOTE: s&s REcOMMENds AT LEAsT .060" cLEARANcE bETwEEN VALVE ANd PIsTON VALVE POckET REcEss. whILE .060" cLEARANcE Is
REcOMMENdEd MINIMuM, IT Is AdVIsAbLE TO hAVE .080" ANd uP, IF POssIbLE.
CAUTION