Vr-36ha — service information – Multiquip VR36HA User Manual
Page 54
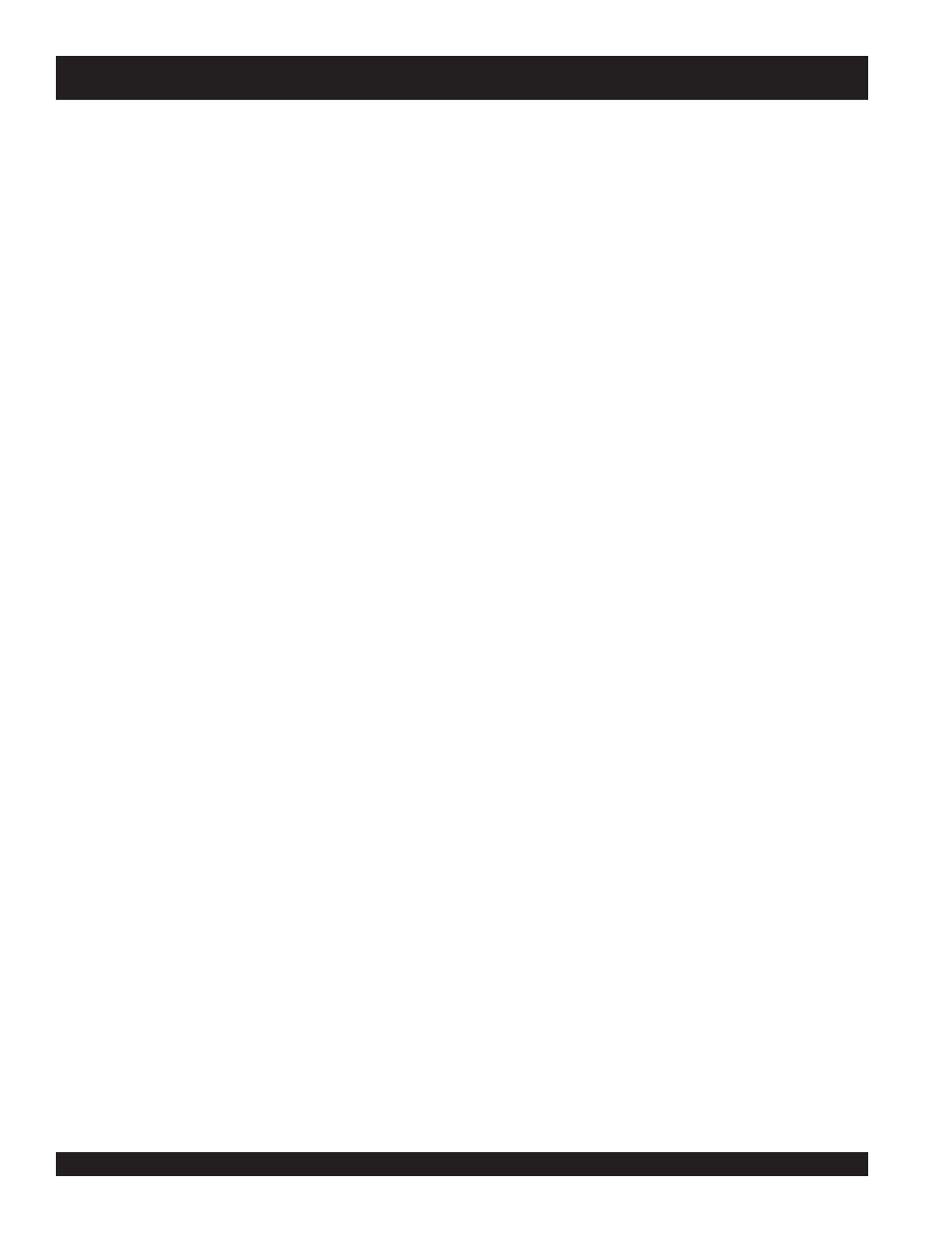
PAGE 54 — VR-36HA • VIBRATORY ROLLER — PARTS & OPERATION MANUAL — REV. 6 (06/13/06)
VR-36HA — SERVICE INFORMATION
2.2 Drum Drive
The drum drive circuit is a parallel, closed loop system consisting
of a hydrostatic pump, two relief valves, towing valve, and front
and rear drum drive motors.
The hydrostatic pump is manually controlled by a cable
connected to the forward / reverse shift lever located on the right
side of the operator. When the shift lever is placed in forward,
high-pressure oil is supplied by the hydrostatic pump to the valve
block (port A). The valve block directs this high-pressure oil to
the front and rear drum drive motors. Return oil from the motors
is returned to the valve block (port B) and is returned to the
suction side of the hydrostatic pump. When shifted into reverse,
the high-pressure and suction ports on the hydrostatic pump are
reversed. Oil flow is then in the opposite direction of forward
(port B becomes high-pressure and port A becomes suction).
2.3 Vibration & Steering
The vibration and steering system is an open loop circuit operated
by a gear type pump. Separate relief valves control each circuit.
This system consist of the gear pump, relief valves, electric
vibration control valve, vibration drive motor, steering valve, and
steering cylinder.
The vibration circuit is controlled by an electric control valve
located on the valve block. This valve is controlled by the “ON /
OFF” switch mounted on the steering column. High-pressure oil
is supplied by the pump to the valve block (port P) and is directed
to the electric control valve. When the switch is in the “OFF”
position, this valve is open allowing oil to go to the steering
valve, without driving the vibration motor. When the switch is in
the “ON” position, the electric control valve closes and oil is
directed out of port 1 to the vibration motor. Return oil from the
motor returns to the valve block via port 2 and is directed to the
steering valve.
Steering is controlled by a steering valve and cylinder. The
steering wheel is direct coupled to
the steering valve controling the oil flow to the cylinder. Oil
supplied from the vibration circuit is directed to port 3 which
connects to port P of the steering valve. When steering is not
being used, oil passes out of port T of the valve block and returns
to the hydraulic tank. When the steering wheel is operated, the
steering valve closes and oil is directed to port L or R to extend
or retract the steering cylinder.
2.4 Back Pressure Valve
A back pressure valve located in the block attached to the return
filter keeps the return system at 14.5 PSI. This maintains the
hydrostatic charge pump oil supplied, prevent cavitation, and
keeps the hydraulic system from draining when the unit is
stopped.
2.5 Towing Valve
A towing valve is located in the valve block. When opened, port
A & B are allowed to connect, bypassing the oil to and from the
drum drive motors. Freewheeling results for towing.
2.6 Testing Hydraulic Pressure
1.
Set the parking brake.
2.
Check and repair all hydraulic leaks.
3.
Check hydraulic oil level.
4.
Adjust engine RPM (3300 +/- 50 RPM)
5.
Operate the machine until the hydraulic oil is at full
operating temperature (approx. 180ш)