4 fault elimination, 1 drive errors, Fault elimination – Lenze EVF9338−EV User Manual
Page 31: Drive errors, Troubleshooting and fault elimination
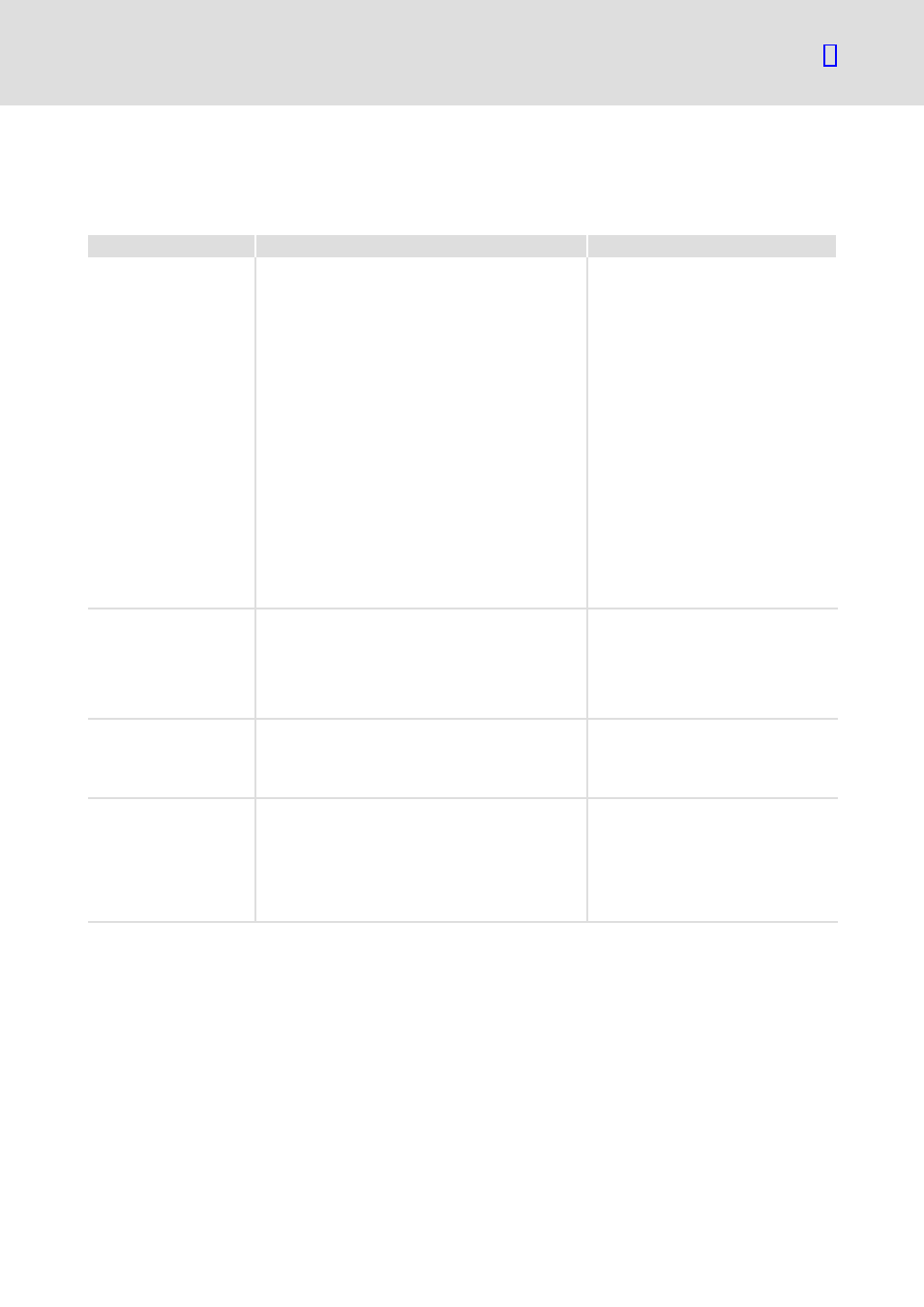
Troubleshooting and fault elimination
Fault elimination
Drive errors
l
31
EDKVF93−04 EN 2.0
4.4
Fault elimination
4.4.1
Drive errors
Malfunction
Cause
Remedy
An asynchronous motor
with feedback rotates in an
uncontrolled manner and
with low speed
The motor phases are reversed so that the rotating field
of the motor is not identical with the rotating field of
the feedback system. The drive shows the following
behaviour:
l
V/f characteristic control (C0006 = 5)
– The motor rotates faster than the speed setpoint by
the value set in C0074 (influence of the speed
controller, Lenze setting 10 % of n
max
). After the
controller is enabled, it does not stop at zero speed
setpoint or quick stop (QSP).
– The final motor current depends, among other
things, on the set value of the V
min
boost (C0016)
and can rise to I
max
(C0022). This may activate the
fault message OC5.
l
Vector control (C0006 = 1)
– The motor rotates slowly with maximum slip speed
(depending on motor data and maximum current)
and does not react to a speed setpoint. The
direction of rotation, however, is determined by
the sign of the speed setpoint.
– The motor current rises up to I
max
(C0022). This
may activate the fault message OC5 with a time
delay.
l
Check motor cable for correct phase
relation.
l
If possible, operate the motor with
deactivated feedback (C0025 = 1) and
check the direction of rotation of the
motor.
Motor does not rotate
although the controller is
enabled (
c is off) and a
speed setpoint has been
specified.
The two terminal strips X5 are reversed. Since X5/A1 and
X5/28 face each other, the controller can be enabled if
the control terminals are internally supplied. All other
connections, however, are assigned incorrectly so that
the motor cannot start.
Check the position of the terminal strips:
l
If you look at the connection unit in
reading direction, the left terminal
strip X5 must be connected with the
input signals and the right terminal
strip X5 must be connected with the
output signals.
The monitoring of the
motor phases (LP1) does
not respond if a motor
phase is interrupted,
although C0597 = 0 or 2
The function block MLP1 is not entered into the
processing table.
Enter the function block MLP1 into the
processing table. The function block MLP1
requires 30
ms of calculating time.
If during high speeds
DC−injection braking (GSB)
is activated, the fault OC1
(TRIP) or OU (TRIP) occurs
During DC−injection braking the controller sets pulse
inhibit for a short time (DCTRL−IMP) to reduce the
magnetisation in the motor before a DC voltage is
injected into the motor. At high speeds (e. g. in case of
mid−frequency motors) the residual voltage which
develops from the residual magnetism and high speed
can generate such a high motor current that OC1 or OU
are activated.
Prolong the duration of the pulse inhibit:
l
Connect the output signal DCTRL−IMP
to the function block TRANSx and
adjust the desired switch−off time
there (usually 500 ms). If
DCTRL−CINH1 is set to HIGH, the
duration of the pulse inhibit is
prolonged by the time adjusted.