Function block library lenze9300servo.lib, Stop – Lenze DDS Function library 9300 Servo User Manual
Page 21
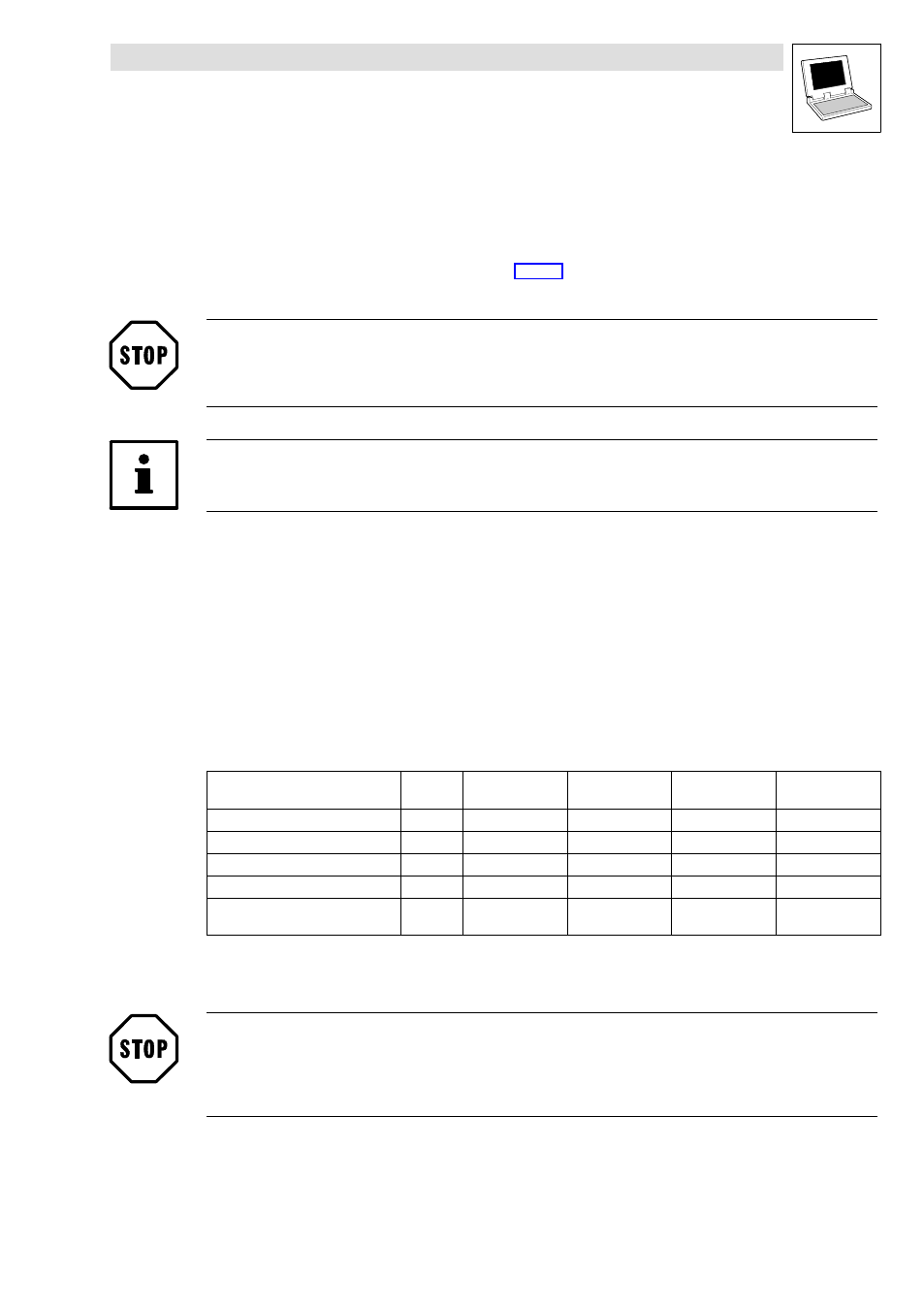
Function block library Lenze9300Servo.lib
Special functions
2.1.2
Supply−failure control (L_MFAIL)
2−11
L
Lenze9300Servo.lib EN 1.1
Parameterization of the supply−failure control
The parameters to be set are strongly dependent on the motor used, the inertia of the driven machine
and the drive configuration (single drive, drive network, master−slave operation, etc.). This function
must therefore be adapted to the individual application in every case.
The following specifications refer to Chapter 2.1.2.1
Important settings prior to the initial commissioning:
Stop!
With internal voltage supply to the terminals, terminal X6/63 is used as a voltage source for external
potentiometers. In this case, measure across terminals +U
G
, −U
G
.
Note!
To perform the measurements, a new download that includes the changes must be made.
1. Measure the DC−bus voltage with an oscilloscope (channel 1)
– with a suitable voltage divider across the terminals +U
G
, −U
G
or
– by providing the DC bus voltage at terminal X6/62, for instance. To do this, connect the
system variable MCTRL_nDCVolt_a with the system variable AOUT2_nOut_a .
2. Measure the speed with an oscilloscope (channel 2)
– by supplying the speed on terminal X6/62, for instance, (standard setting). To do this,
connect the system variable MCTRL_nNAct_a with the system variable AOUT1_nOut_a .
3. Enter, in C0472/20 ( FCODE_nC0472_20_a ) the threshold for the supply−failure detection.
The entry depends on the setting in C0173 (adjsutment of the U
G
−threshold).
– Set the threshold approx. 50 V above the switch−off threshold LU
(example for C0173 = 0.1; C0472/20 = 48 % = 480 V).
Supply voltage range
C0173 =
Switch−off
threshold LU
Switch−on
threshold LU
Switch−off
threshold OU
Switch−on
threshold OU
< 400 V
0
285 V
430 V
770 V
755 V
400 V
1
285 V
430 V
770 V
755 V
400 V ... 460 V
2
328 V
473 V
770 V
755 V
480 V without brake chopper
3
342 V
487 V
770 V
755 V
Operation with brake chopper (up to
480 V)
4
342 V
487 V
800 V
785 V
4. Set the setpoint to which the DC bus voltage is to be controlled:
– Set the setpoint to approx. 700 V (C0472/18 = 70%).
Stop!
This setpoint must be below the threshold of any brake unit which may be connected.If a connected
brake unit is activated, the drive is braked with the maximum possible torque (I
max
). The desired
operating behaviour is lost.