Description – JUMO 705010 mTRON T - Multichannel Controller Module Data Sheet User Manual
Page 2
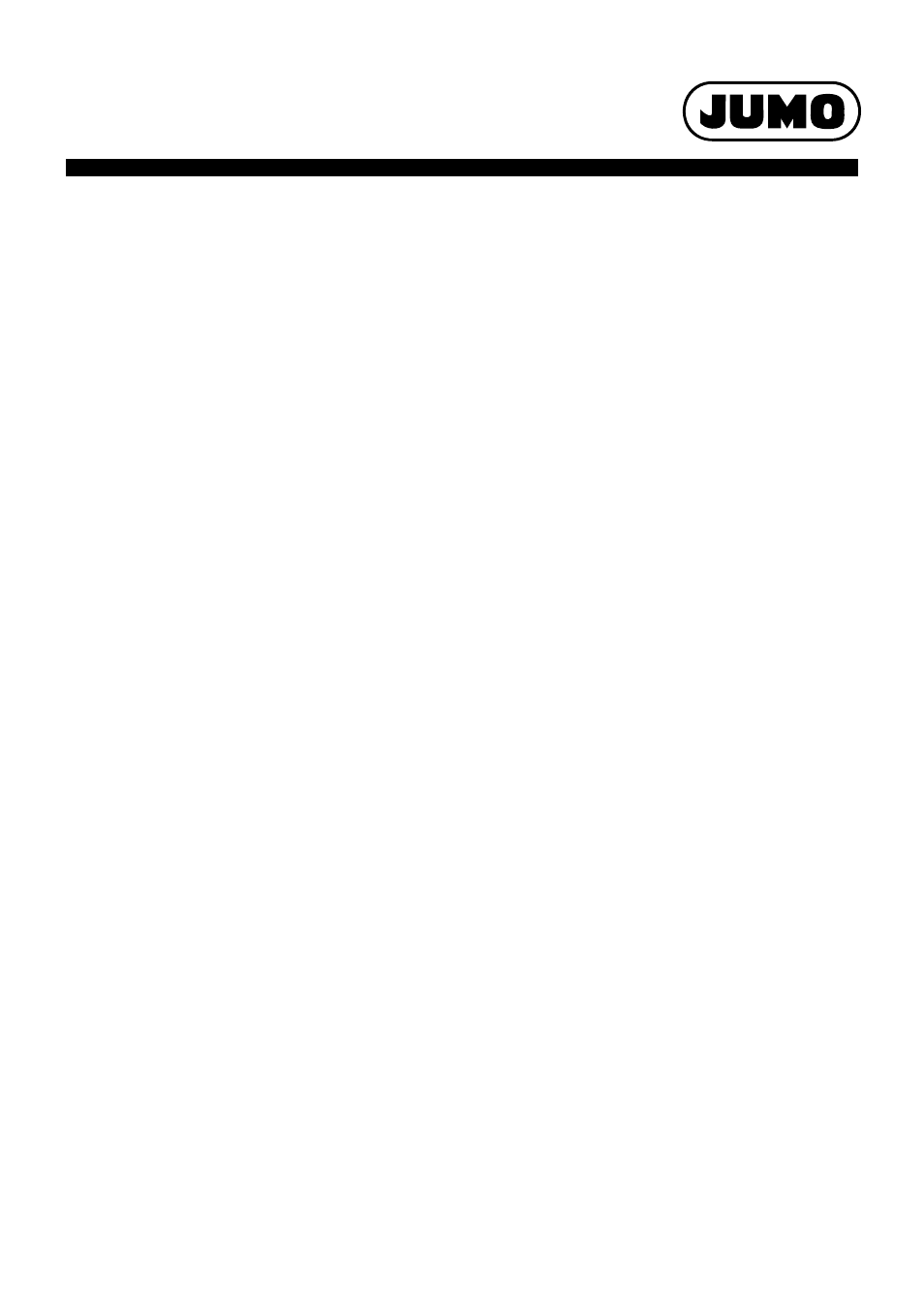
JUMO GmbH & Co. KG
Delivery address: Mackenrodtstraße 14
36039 Fulda, Germany
Postal address:
36035 Fulda, Germany
Phone:
+49 661 6003-0
Fax:
+49 661 6003-607
E-mail:
Internet:
www.jumo.net
JUMO Instrument Co. Ltd.
JUMO House
Temple Bank, Riverway
Harlow, Essex CM20 2DY, UK
Phone: +44 1279 635533
Fax:
+44 1279 635262
E-mail:
Internet: www.jumo.co.uk
JUMO Process Control, Inc.
6733 Myers Road
East Syracuse, NY 13057, USA
Phone: 315-437-5866
1-800-554-5866
Fax:
315-437-5860
E-mail:
Internet: www.jumousa.com
2013-05-07/00529107
Data Sheet 705010
Page 2/15
Description
Controller types
The controller can be configured as two-state
controller, three-state controller, modulating
controller, continuous controller, or continuous
controller with integrated actuator controller
independent of the number of channels. If the
number of standard and optional inputs and
outputs provided on the controller module are
insufficient for the desired configuration, exter-
nal inputs and outputs are available through
the system bus. The cycle time of the control-
ler module can be configured between 50 ms
and 250 ms.
Parameter sets
Two parameter sets can be saved for each of
the four controller channels. Each parameter
set contains 17 parameters so that separate
derivative and reset times can be set for the
"Heating" and "Cooling" functions. The param-
eter set can be changed over separately for
each controller channel.
Self-optimization
Self-optimization makes it possible for the
controller to be adjusted to the control loop by
a user who is not a control technology expert.
During this process, the reaction of the control
loop to the actuating variable is evaluated. The
oscillation method is set as the standard
method in the controller. The step response
method can be activated in the setup program
or the multifunction panel.
Setpoint values
Up to four setpoint values can be entered for
each controller channel. The setpoint value
changeover is controlled by two digital signals.
Ramp function
The ramp function is used for a continuous
setpoint value change up to the ramp limit
value (setpoint value input). Any analog value
(e.g. actual value) available in the system can
be selected as the start value. The ramp
change is defined via two adjustable gradients
(upward, downward). If the setpoint value
changes, the new setpoint value is reached
under consideration of the set gradient. De-
pending on the start value, the result is an up-
ward or downward ramp. Alternatively a ramp
start synchronous to a digital signal is possi-
ble. The ramp function can be stopped and
canceled via digital signals.
It is possible to enter a tolerance band (sym-
metrically or above/below) around the setpoint
value curve to monitor the actual value. If the
actual value leaves the tolerance band, a dig-
ital signal is activated which can be used inter-
nally or externally.
Limit value monitoring
For each analog input, two separate alarms
(min/max alarm) can be activated; each alarm
has its own limit value. Alarm type, event text,
collective alarm, alarm suppression, and
alarm delay are configurable.
In addition, four limit values with configurable
alarm functions are available. Any analog sig-
nal can be selected as the actual value and
setpoint value. The actual value monitoring
depends on the set limit value and the used
alarm function (monitoring band around the
setpoint value, limit value above or below the
setpoint value as well as independent of the
setpoint value).
Math and logic function
The optional math and logic function (extra
code of base unit) can be used to link analog
or binary values. Up to four freely configurable
math or logic formulas can be entered with the
setup program. The results are available in the
controller module for various functions or can
be made available at the outputs.
Analog inputs
The maximum four analog inputs are universal
measuring inputs for RTD temperature
probes, thermocouples, resistance transmit-
ters, resistance/potentiometers, and standard
signals (current, voltage). Linearizations for
over 20 common measuring probes (RTD
temperature probes, thermocouples) are
stored. A measured value offset or a fine ad-
justment can be carried out to compensate for
plant-specific deviations. Due to the measur-
ing circuit monitoring, a measuring range that
is too high or too low, probe/cable break, and
probe/cable short circuit are detected – de-
pending on the measuring element type – so
that the system is switched to an operational
safe status in the event of an error.
Customer-specific linearization
A customer-specific linearization is also possi-
ble. Programming is carried out through a for-
mula (polynomial up to the 4th order) using the
setup program.
Analog outputs
The maximum three analog outputs are freely
scalable (current, voltage). They can be used
to make available controller outputs, setpoint
values, math results, signals of the analog in-
puts (e.g. actual value), and values from the
system bus. The output behavior in case of an
error is selectable from available options (e.g.
behavior according to NAMUR recommenda-
tion NE 43).
Digital inputs
The signals of the up to eight digital inputs (DC
0/24 V) can be used to initiate various internal
functions such as changeover of the parame-
ter set, start of self-optimization, or acknowl-
edgement of a limit value exceedance.
Linking of digital signals
External and internal digital signals (e.g. logic
results) can be OR-linked. Four logic links of
up to four digital signals are possible. The re-
sults are also available to control internal func-
tions or they can be made available at the
digital outputs.
Digital outputs
The up to eight digital outputs can be used to
provide digital signals such as controller out-
puts, signals of the limit value monitoring, logic
results, signals of the digital inputs, and values
from the system bus. In addition to the two
standard outputs (relay or logic), further out-
puts can be realized via the option slots (relay,
solid-state relay, open-collector output).
Counter
The controller module is equipped with a
counter which is solidly connected to the first
digital input and counts all low-high edges of
the input signal. The counter reading is avail-
able in the base unit. The counter runs end-
lessly in the "Counting" operating mode. The
counter starts with zero again after reaching
the maximum counting value (0xFFFF). In the
"Filling" operating mode the counter is started
via a digital signal and generates a switch-off
signal when the adjustable switch-off limit is
reached.
Operation
The controller module is operated with the
multifunction panel. Furthermore, specific val-
ues can be changed and functions can be ac-
tivated via the PLC or the Modbus interface
(base unit).