Description – JUMO 705040 mTRON T - Router Module Data Sheet User Manual
Page 2
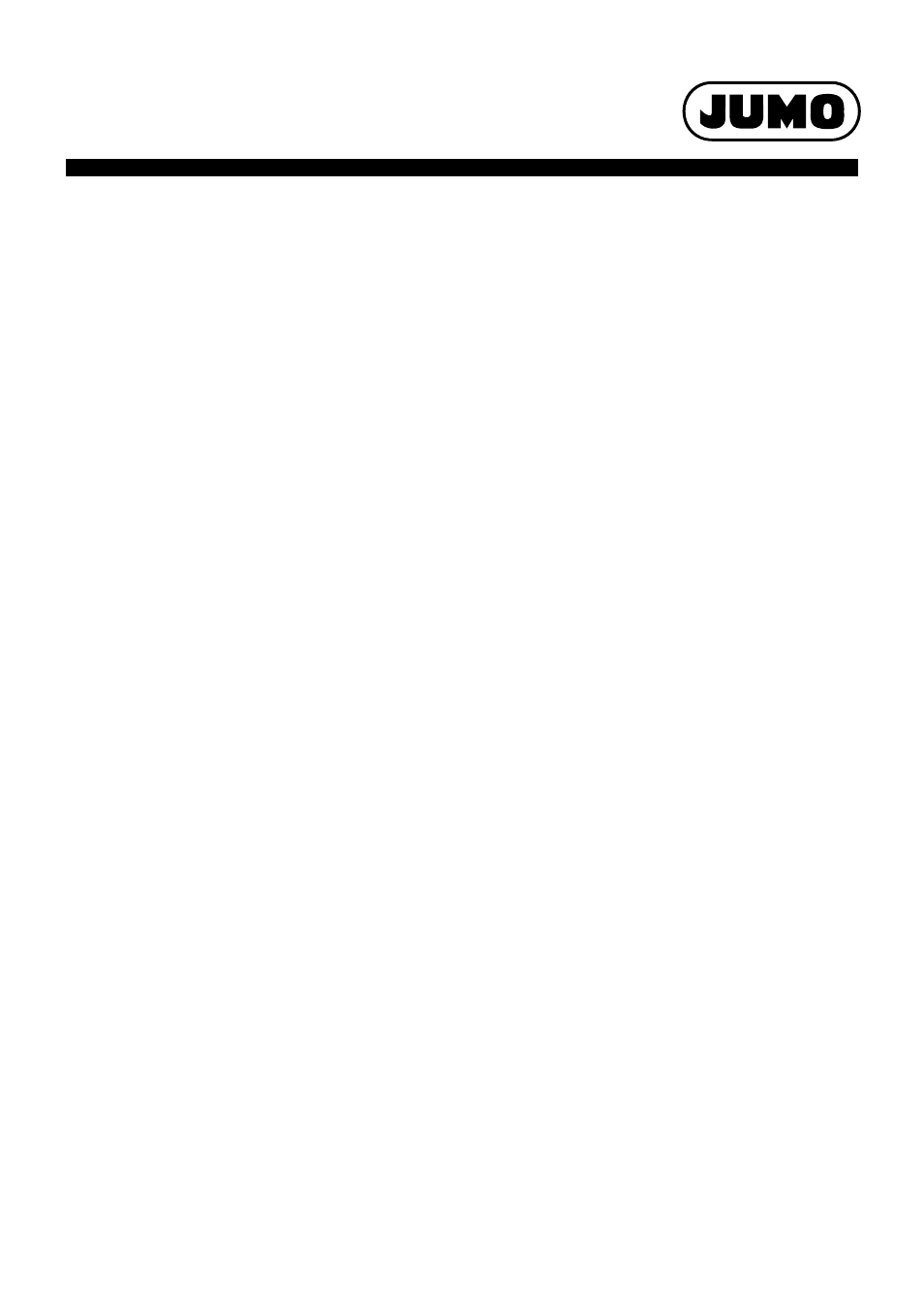
2014-04-15/00529103
Data Sheet 705000
Page 2/10
JUMO GmbH & Co. KG
Delivery address: Mackenrodtstraße 14
36039 Fulda, Germany
Postal address:
36035 Fulda, Germany
Phone:
+49 661 6003-0
Fax:
+49 661 6003-607
E-mail:
Internet:
www.jumo.net
JUMO Instrument Co. Ltd.
JUMO House
Temple Bank, Riverway
Harlow, Essex CM20 2DY, UK
Phone: +44 1279 635533
Fax:
+44 1279 635262
E-mail:
Internet: www.jumo.co.uk
JUMO Process Control, Inc.
6733 Myers Road
East Syracuse, NY 13057, USA
Phone: 315-437-5866
1-800-554-5866
Fax:
315-437-5860
E-mail:
Internet: www.jumousa.com
Description
Functionality
• Multichannel controller, program generator
(optional)
• Measured data detection, visualization, and
recording incl. batch reporting (optional)
with multifunction panel
• Measured data archiving and evaluation by
means of the PC Evaluation Software
PCA3000 and PCA Communication Soft-
ware PCC
• Operation, visualization und batch reporting
with Plant Visualization Software SVS3000
• PLC programming system CODESYS; pro-
gramming acc. to IEC 61131-3
Multilingual operation
Operation and configuration of the measuring,
control, and automation system is possible in
many European and Asian languages.
Setup program
The setup program is installed on a PC and
connected to the base unit (central processing
unit) or the multifunction panel via USB or LAN
interface. That way the entire system can be
comfortably configured, parameterized, and
operated.
The setup data is transmitted to the up to 30
connected input/output modules (system bus).
General setup data and functions:
• Hardware configuration of the entire system
• Selection and editing of the operating lan-
guages
• Configuration and parameterization of the
input and output modules
• Configuration of the central processing unit
and the multifunction panel
• Configuration and programming of the PLC
• Program editor for 99 programs
• Configuration of the 9 program generators
• Configuration of the recording and the batch
reporting
• Editor for customer-specific process images
Central processing unit
The central processing unit is the heart of the
system. It contains the process image of the
application and manages the configuration
and parameter data of the complete system
(except for the multifunction panel).
For individual control tasks 64 limit values can
be monitored.
Nine program generators and a PLC accor-
ding to IEC 61131-3 are available as an op-
tion.
The central processing unit continuously com-
pares the saved system configuration with the
data of the existing modules. For this reason
Plug and Play replacement of the module in-
sert of controller and input/output modules is
possible during service work (Hot-Connect).
Multichannel controller module
In the standard version, the multichannel con-
troller module is a 2-channel PID controller
with relay output or logic output to control a
solid-state relay. It is additionally equipped
with three optional slots which can be used to
extend the number of inputs and outputs. As a
result, all common controller types can be uti-
lized including the cascade controller. Even a
4-channel two-state controller is possible.
The module operates independently, the con-
trol task is carried out even if the central pro-
cessing unit fails or the higher-ranking system
malfunctions. This behavior can be confi-
gured.
All controller channels can operate as a fixed-
setpoint controller or a program controller. The
programs are specified by the program gene-
rator function of the central processing unit or
by the PLC.
Math and logic functions can be utilized by the
user with the setup program.
Multifunction panel 840
The multifunction panel with TFT touch screen
is used for clearly-arranged measured data vi-
sualization, operation, configuration, and pa-
rameterization of the system.
As an interface between man and machine, it
allows a clear look into the process statuses
and parameters of the system. It is perfectly
suited for the display and operation of the con-
troller screen, process screen, program editor
or recording function. Controller setpoint val-
ues and texts for batch reporting can be direct-
ly entered on the screen.
Operating panels 350, 570, 1040
As of system version 02 the measuring, con-
trol, and automation system supports the use
of up to four operating panels. The panels con-
tain a CODESYS runtime system (V3.5 SP3
patch 9 or higher) and they are connected via
Ethernet to the central processing unit's LAN
interface.
The function of an operating panel is imple-
mented as a PLC application (target/web visu-
alization).
Input/output modules
The following input/output modules extend the
system in addition to the multichannel
controller module:
• Relay module 4-channel
• Analog input module 4-channel
• Analog input module 8-channel
• Digital input/output module 12-channel
Router module
The router module is used to achieve decen-
tralization within the automation system (the
input/output modules are distributed to several
DIN rails/control cabinets). Up to 100 m dis-
tance between two router modules or between
a router module and a base unit/ multifunction
panel are possible. Up to 30 router modules
and up to 30 input/output modules are possi-
ble in a system.
No configuration of the router module is re-
quired. It is integrated into the overall system
by the setup program.
PLC function
The PLC function can be used to read and
write to all inputs and outputs of the system
modules. A library with predefined function
modules and data types including their docu-
mentation is provided for the user.
For programming a control application, all
editors defined in the IEC 61131-3 standard
are provided:
• Structured text (ST)
• Sequential function chart (SFC)
• Continuous function chart (CFC)
• Function block diagram (FBD)
• Ladder diagram (LD)
• Instruction list (IL)
Furthermore, a large number of functions are
implemented which can be used to quickly and
efficiently debug, test, and start the applica-
tion.
In addition, the user has the following func-
tions and possibilities when using the PLC:
• Generation of events saved in the event list
of the central processing unit
• Configuration of all system modules
• Process screen control of the multifunction
panel
The PLC programming system is started from
the setup program. Information about the sys-
tem hardware (modules) is automatically im-
ported into the PLC programming system. The
user can assign machine-specific names to
process data so that working with the PLC is
even more comfortable.
A fully adequate OPC server is available in
connection with the PLC function. This simpli-
fies the exchange of data with other systems
such as SCADA systems or other control sys-
tems.
Event list
The event list within the central processing
unit contains all events that occurred in the
system including date and time. This includes
system messages (configuration changes of a
module, mains OFF/ON of the central pro-
cessing unit), general events (sending an e-
mail), malfunctions (module errors, communi-
cation malfunction), alarms and collective
alarms.
An alert e-mail can be sent up to three ad-
dresses simultaneously. Up to five alarm texts
can be configured, the sending is controlled
via digital signals.
Recording function
The optional recording function in the multi-
function panel detects, visualizes, and records
all measuring and process data. The user can
transfer the data to the PC Evaluation Soft-
ware PCA3000 using a USB memory stick or
the PCA Communication Software PCC. The
data can then be evaluated in the software.