Wiring connections – Flint & Walling Constant Pressure Pumping Stations - ADW2W73 User Manual
Page 3
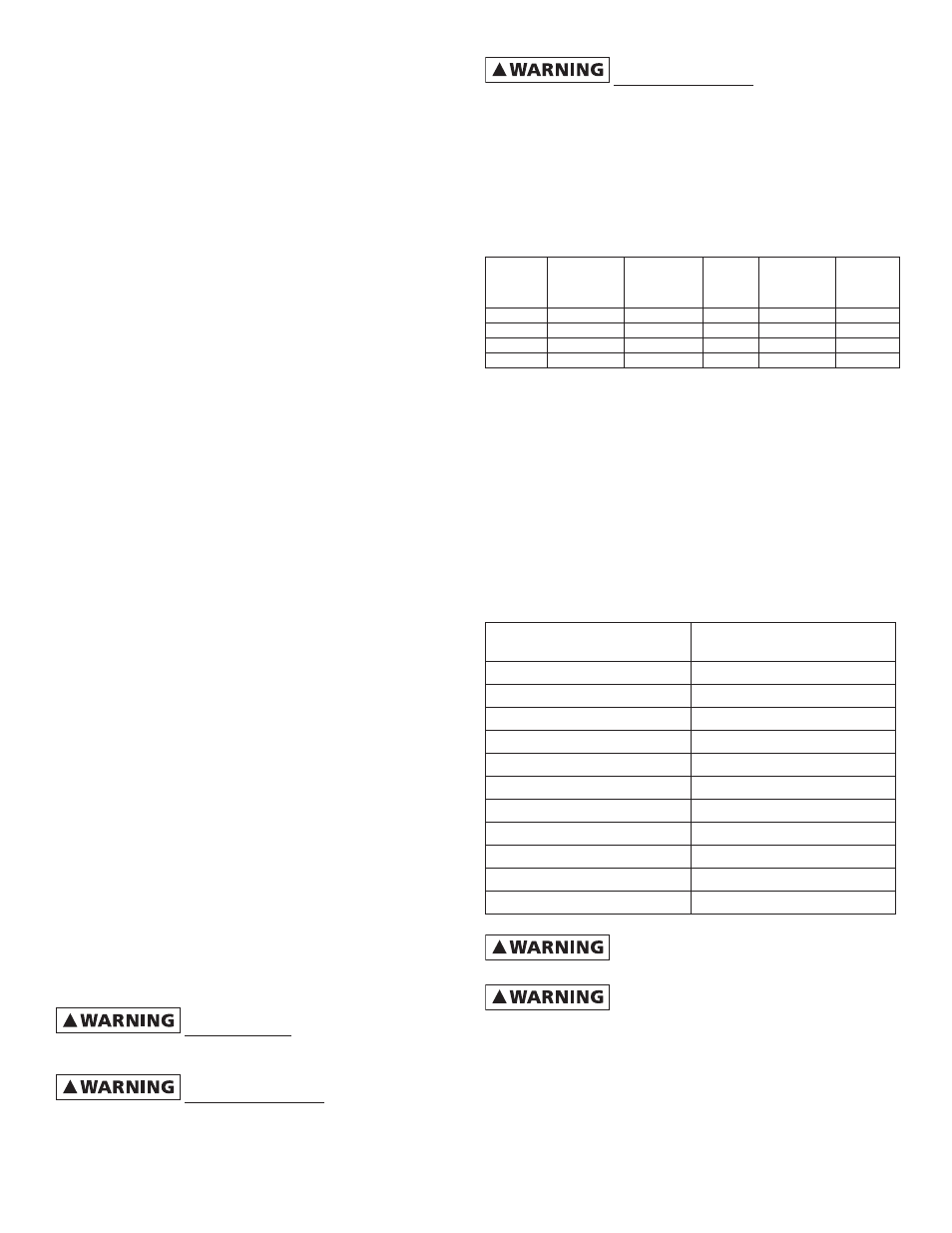
3
(FW1365)
95 North Oak St. • Kendallville, IN 46755 • 1-800-345-9422
3. The Pump Station shall be lifted with proper lifting
equipment (i.e. fork lift). Be sure all necessary lifting
equipment is used properly.
4. DO NOT ATTEMPT TO USE DRIVE SUPPORT BRACKET FOR
LIFTING THE PUMP STATION. The bracket will not support
the overall weight of the pump station.
5. The pump station must be installed according NEC and
local electrical codes. Proper electrical disconnect MUST be
installed in view of the pump station.
6. Ensure compliance with all applicable local, state, and
OSHA regulations when installing, operating, repairing, or
maintaining the pump station.
7. The pump station is manufactured to best ensure operator
safety under normal operating conditions. The manufacturer
will not take any responsibility for personal or equipment
damage if the equipment has been modified or if the
safeguards have been modified. Any proposed modifications
must be carefully documented (to include a risk analysis) by
the party proposing the modification; and coordinated with
and approved by the manufacturer. Otherwise, the customer
assumes all responsibility for its actions and subsequent
consequences.
InStAllAtIOn PrOceDure
1. Position the skid in final location and attach to pad as
necessary. NOTE: For serviceability of the pump and
protection of discharge plumbing fixtures down line of the
pump station, it is recommended to incorporate unions and
isolation valves on the intake and discharge plumbing. If
deemed applicable, a bi-pass loop with properly placed
valves should also be incorporated into the installation.
2. Install plumbing to the intake of the pump. Note: For
proper functionality of the system it is not recommended
that a pipe size smaller than 2-1/2” is use on the intake of
the pump. Note: For suction lift applications, intake pipe
plumbing needs to allow for suction pipe to be filled by
external water source to prime the pump. Note: If the water
source for the pump station is susceptible to containing
debris, an appropriately sized filter should be installed prior
to the pump intake which should be checked & cleaned
regularly to avoid clogging the pump and/or degrade system
performance.
3. Install plumbing to discharge manifold. Note: For proper
functionality of the system it is not recommended that a pipe
size smaller than 2” is use on the discharge manifold. Note:
To avoid causing damage to the system, when tightening
onto the threads of the discharge manifold, a pipe wrench
should be used on the manifold to keep the manifold from
turning.
4. With supply power OFF, connect power supply cables to L1
& L3 terminals for single phase power supplied drives or L1,
L2 & L3 terminals for three phase supplied drives. Attach
ground wire to grounding lug on drive. See Figures 4 - 6 on
page 7 & 8 for depictions of each HP power supply wiring
connections.
!
3 & 5 HP Models: To avoid a fire hazard and
maintain validity of the UL listing, torque the power terminal
screws to 12 lb.-in. (1.4 N-m).
!
7.5 HP 3 Phase Model: To avoid a fire hazard
and maintain validity of the UL listing, torque the power
terminal screws to 13.2 lb.-in. (1.5 N-m).
!
7.5 HP 1 Phase Model: To avoid a fire hazard
and maintain validity of the UL listing, torque the power
terminal screws to 21.6 lb.-in. (2.5 N-M).
Wiring connections
cIrcuIt BreAKer AnD WIre SIzInG
The minimum circuit breaker size and maximum allowable
wire lengths for connection of motor to the Artesian Drive
are given in the following table:
tABle 1: MInIMuM BreAKer SIze AnD MAxIMuM
cABle lenGth (In feet)
Drive
Model
Recommended
Input Cable
Recommended
Motor Cable
Maximum
Cable
Length to
Motor (Ft.)
Recommended
Breaker
Maximum
Continuous
Current
ADW2W31
10
14
325
30
9.6
ADW2W51
8
12
325
30
15.0
ADW2W71
6
10
325
50
22.0
ADW2W73
8
10
325
30
22.0
NOTE:
•
Maximum allowable wire lengths are measured between
the controller and motor.
•
Aluminum wires should not be used with the Artesian
Drive.
•
Wire sizing between the service entrance and the
controller must be sufficient to provide the required
maximum input amps to the controller while conforming
to local standards and codes.
The pressure tank pre-charge setting should be 70% of the
system pressure sensor setting as indicated in the following
table.
tABle 2: PreSSure tAnK AIr PrechArGe (PSI)
System Pressure (at Pressure
Sensor)
Pressure Tank Precharge
Setting (± 2 PSI)
30
21
35
25
40
28
45
32
50
35
55
39
60
42
65
46
70
49
75
53
80*
56
!
Do not use motor or system in swimming
areas.
!
Because of the leakage current produced
by the internal filtering, permanent fixed ground connections
must be made using two independent conductors each with
a cross-section equal to or exceeding that of the supply
conductors. The drive is provided with two ground terminals
marked PE to facilitate this for 3 & 5 HP models.
NOTE: Ensure that the system is properly grounded all the
way to the service entrance panel. Improper grounding may
result in the loss of voltage surge protection and interference
filtering.