EUCHNER CMS(07/11) User Manual
Page 4
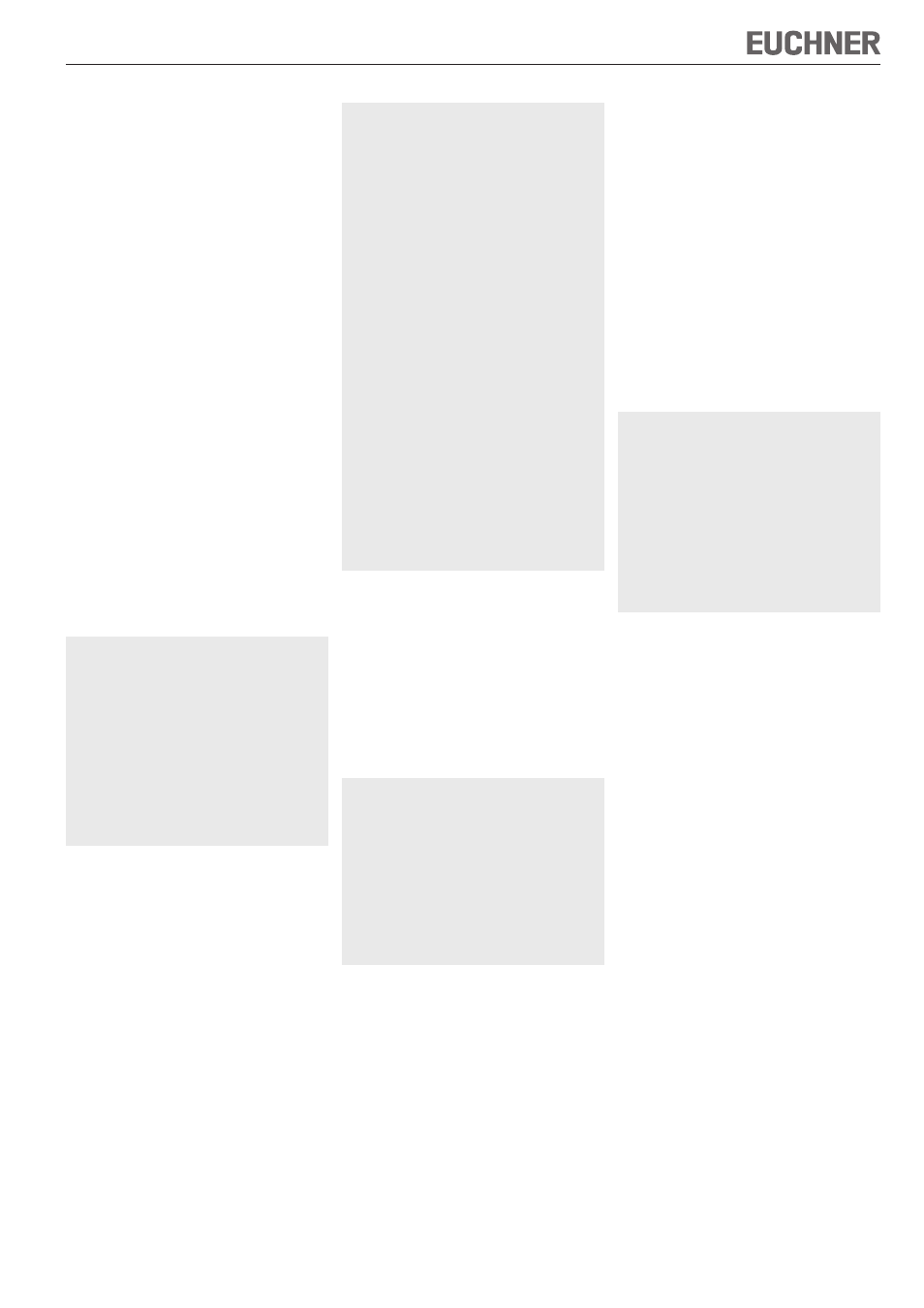
Operating Instructions Read Heads/Actuators for Evaluation Units CMS
These operating instructions only apply in
conjunction with the operating instructions for
the relevant evaluation units CMS-E-.. !
Correct use
The Coded Magnetic Safety switches series CMS
are safety devices for monitoring movable safety
guards.
In combination with a safety guard, this safety
component prevents dangerous machine move-
ments from being performed for as long as the
safety guard is opened. A stop command is
triggered if the safety guard is opened during the
dangerous machine function.
Before safety switches are used, a risk assessment
must be performed on the machine, e.g., in
accordance with:
EN ISO 13849-1, Safety of machinery. Safety
related parts of control systems. General
principles for design
EN ISO 12100, Safety of machinery – Basic
concepts, general principles for design
EN 62061, Safety of machinery – Functional
safety of safety-related electrical, electronic and
programmable electronic control systems.
Correct use includes observing the relevant
requirements for installation and operation, e.g.:
EN 1088, Safety of machinery. Interlocking
devices associated with guards. Principles for
design and selection
EN 60204-1, Safety of machinery. Electrical
equipment of machines. General requirements
The read heads and actuators must be used only
with the designated evaluation units from EUCHNER.
On the use of different evaluation units, EUCHNER
provides no warranty for safe function.
Important!The user is responsible for safe
integration of the device into a safe overall system.
For this purpose, the overall system must be
validated, e.g. in accordance with EN ISO 13849-
2. Correct use requires observing the permissible
operating parameters (see Technical data). If a
product data sheet is included with the product,
the information on the data sheet applies in case
of discrepancies with the operating instructions.
Only components may be used that are permissible
in accordance with the following combination
options table. Refer to the operating instructions
of the corresponding component for further
information.
Exclusion of liability and warranty
In case of failure to comply with the conditions for
correct use stated above, or if the safety
instructions are not followed, or if any servicing is
not performed as required, liability will be excluded
and the warranty void.
General Safety Instructions
Safety switches protect people. Incorrect
installation or tampering can lead to severe injuries
to personnel.
Check the safe function of the safety guard
particularly
each time after putting into operation
each time after replacement of a CMS component
after an extended period without use
after every fault
Independent of these checks, the safe function of
the safety guard should be checked at suitable
intervals as part of the maintenance schedule.
Warning! Fatal injury due to incorrect connection
or incorrect use.
Safety switches must not be bypassed (bridging of
contacts), turned away, removed or otherwise
rendered ineffective. On this topic pay attention in
particular to the measures for reducing the possibility
of bypassing from EN 1088:1995+A2:2008,
Section 5.7.
The device is only allowed to be installed and
placed in operation by authorized personnel
who are familiar with proper handling of safety
components
who are familiar with the applicable EMC
regulations
who are familiar with the applicable occupational
health and accident prevention regulations
who have read and understood the operating
instructions.
Function
The safety switch CMS consists of an
evaluation unit, read head and actuator and
is only functional in particular combinations
(see combination options)!
The read head connected to the evaluation unit
contains reed contacts that are activated by the
coded magnetic actuators. The evaluation unit
converts this information and transfers the safety
guard state to the control system via a safety
contact.
Mounting
Caution! Risk of damage to equipment as a result
of incorrect installation.
Read heads or actuators must not be used as a
mechanical end stop. Fit an additional end stop
for the movable part of the safety guard.
Caution! Read heads or actuators must not be
used in an environment with strong magnetic fields.
Important! Read heads and actuators must be
positively mounted to the safety guard, e.g. by
using the safety screws supplied.
Important! The M8 plug connector must be
tightened with a suitable tool.
The read head and actuator may be installed in any
position. The alignment of the read head and the
actuator must be kept in mind (see Figure 1).
Install read head and actuator so that:
They are accessible for inspection and replace-
ment work
The active faces of the read head and actuator
are exactly opposite each other when the safety
guard is closed (see Figure 1)
The actuator is in the activation range of the read
head when the safety guard is closed.
A guide and an additional stop must be installed
for the moving part of the safety guard.
A latching mechanism in the closed position must
be provided for the safety door.
If the read head and actuator are installed flush,
the operating distance decreases depending on
the installation depth and the material of the safety
guard.
The read distance decreases when the read head
and actuator are installed on ferromagnetic ma-
terial.
If the approach speed between the read head
and the actuator is low and the evaluation unit
CMS-E-BR is used, the approach direction Z (see
Figure 1) should be avoided.
Round actuators have protection against rotation.
In order to ensure that the actuator cannot be
rotated when secured to the protective doors, a
∅ 2 mm hole should be drilled for the safety lug
during installation.
Electrical connection
Warning! In case of an error, loss of the safety
function through incorrect connection.
Lay the connection cables with protection to
prevent the risk of short circuits.
Caution! Risk of damage to equipment or
malfunctions as a result of incorrect connection.
On read heads with LEDs the current on the
contact status indication is not allowed to be
greater than 15 mA.
The read heads must be connected to the
evaluation units in accordance with the wiring dia-
gram (see operating instructions for evaluation
units).