Enerpac VM32 User Manual
Page 2
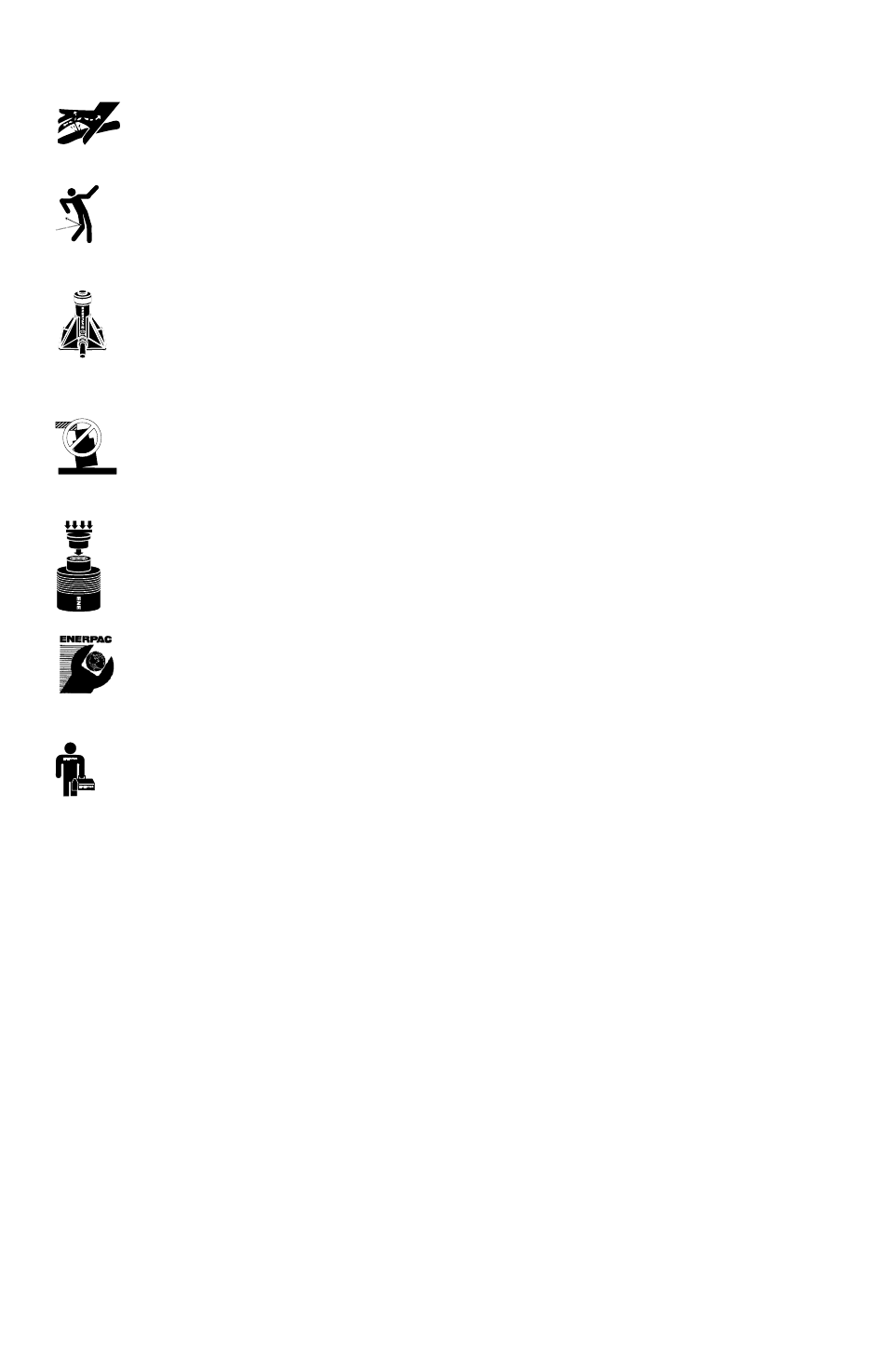
2
of 65°C [150°F] or higher. Protect hoses and cylinders
from weld spatter.
DANGER: Do not handle pressurized
hoses. Escaping oil under pressure can
penetrate the skin, causing serious injury. If
oil is injected under the skin, see a doctor immediately.
WARNING: Only use hydraulic cylinders in a
coupled system. Never use a cylinder with
unconnected couplers. If the cylinder
becomes extremely overloaded, components can fail
catastrophically causing severe personal injury.
WARNING: BE SURE SETUP IS STABLE
BEFORE LIFTING LOAD. Cylinders should
be placed on a fl at surface that can support
the load. Where applicable, use a cylinder
base for added stability. Do not weld or otherwise
modify the cylinder to attach a base or other support.
Avoid situations where loads are not
directly centered on the cylinder plunger.
Off-center loads produce considerable
strain on cylinders and plungers. In addition, the load
may slip or fall, causing potentially dangerous results.
Distribute the load evenly across the entire
saddle surface. Always use a saddle to
protect the plunger.
IMPORTANT: Hydraulic equipment must
only be serviced by a qualifi ed hydraulic
technician. For repair service, contact the
Authorized ENERPAC Service Center in your
area. To protect your warranty, use only ENERPAC oil.
WARNING: Immediately replace worn or
damaged parts by genuine ENERPAC parts.
Standard grade parts will break causing
personal injury and property damage.
ENERPAC parts are designed to fi t properly and
withstand high loads.
3.0 HYDRAULIC CONNECTIONS
3.1 Check All Coupler Connections
1. Use Enerpac hi-fl ow couplers for best results,
or Enerpac regular couplers when very low fl ow
pumps are used. (Maximum fl ow below 1 GPM
— 230 cu. in./min.)
2. Connect hoses to valve at designated port
locations. If using pipe sealants on male pipe
threads, use sparingly and never over ends of
fi ttings where it can be torn loose and get into
system.
4.0 OPERATION
1. Connect and secure hoses and cylinders noting
that the proper ports are connected.
2. Quick disconnects must be fully engaged and
locking collars drawn up fully to ensure free fl ow
of oil between valve and attached component.
3. Before starting pump rotate valve handle counter-
clockwise (CCW), viewed from the top, to open
the valve to tank line. Pump can now be run but
pressure will not build.
4. To build pressure, rotate the handle clockwise
(CW) until the handle stops closing the valve.
Pump can now build pressure. Rotation (CCW
)will release the pressure and/or load and the
decent is controlled by the amount of rotation.
NOTE:
The VM22 and VM32 Enerpac valves are
equipped with an integral user adjustable relief
valve. This relief valve is factory set to 10,000
psi [700 bar]. The valve can be adjusted by fi rst
loosening the jam nut and either rotating the
setscrew clockwise to increase system pressure
or counter-clockwise to reduce system pressure.
Set screw must be locked in place with the jam
nut when adjustments are done.
5.0 TROUBLE SHOOTING
1. System will not build pressure. Check relief valve in
the control valve or in the pump, for proper setting
(see pump repair sheet or valve repair sheet).
Check and secure all hose connections. If trouble
is not corrected, remove cylinder and hoses from
the valve. Now place a pressure gauge in port A
and close (CW) the valve. If pressure cannot be
developed, the unit should be taken to the nearest
authorized ENERPAC Service Center. If pressure
develops, the cylinder, hoses or couplers are the
problem.
2. The cylinder will not build pressure. This is an
indication of a worn valve seat which must be
replaced by a Service Center.
3. VM22 has a check valve in-line with the pressure
port. This check will hold the pressure at port A
after the pump is turned off. When the pump is
functioning properly, the valve closed, you can jog
the pump and hold the pressure at port A.
6.0 MAINTENANCE
1. Periodically check all hydraulic connections to be
sure they are tight. Loose or leaking connections
may cause erratic and/or total loss of operation.
Replace or repair all defective parts promptly.
2. Periodically check the hydraulic oil level in your
system.
3. Change hydraulic oil approximately every 250-300
hours of operation. In dusty or dirty areas, it may
be necessary to change the oil more frequently.
7.0 STORAGE INSTRUCTIONS
In the event that the unit would be stored for any great
length of time (30 days or more), prepare as follows:
1. Wipe the entire unit clean.
2. Disconnect all hydraulic lines to prevent accidental
operation.
3. Cover the unit with some type of protective
cover.
4. Store in a clean, dry environment that is NOT
exposed to extreme temperatures.