Det-Tronics 505 Combustible Gas Detector Transmitter with Combustible Gas Sensor CGS User Manual
Page 9
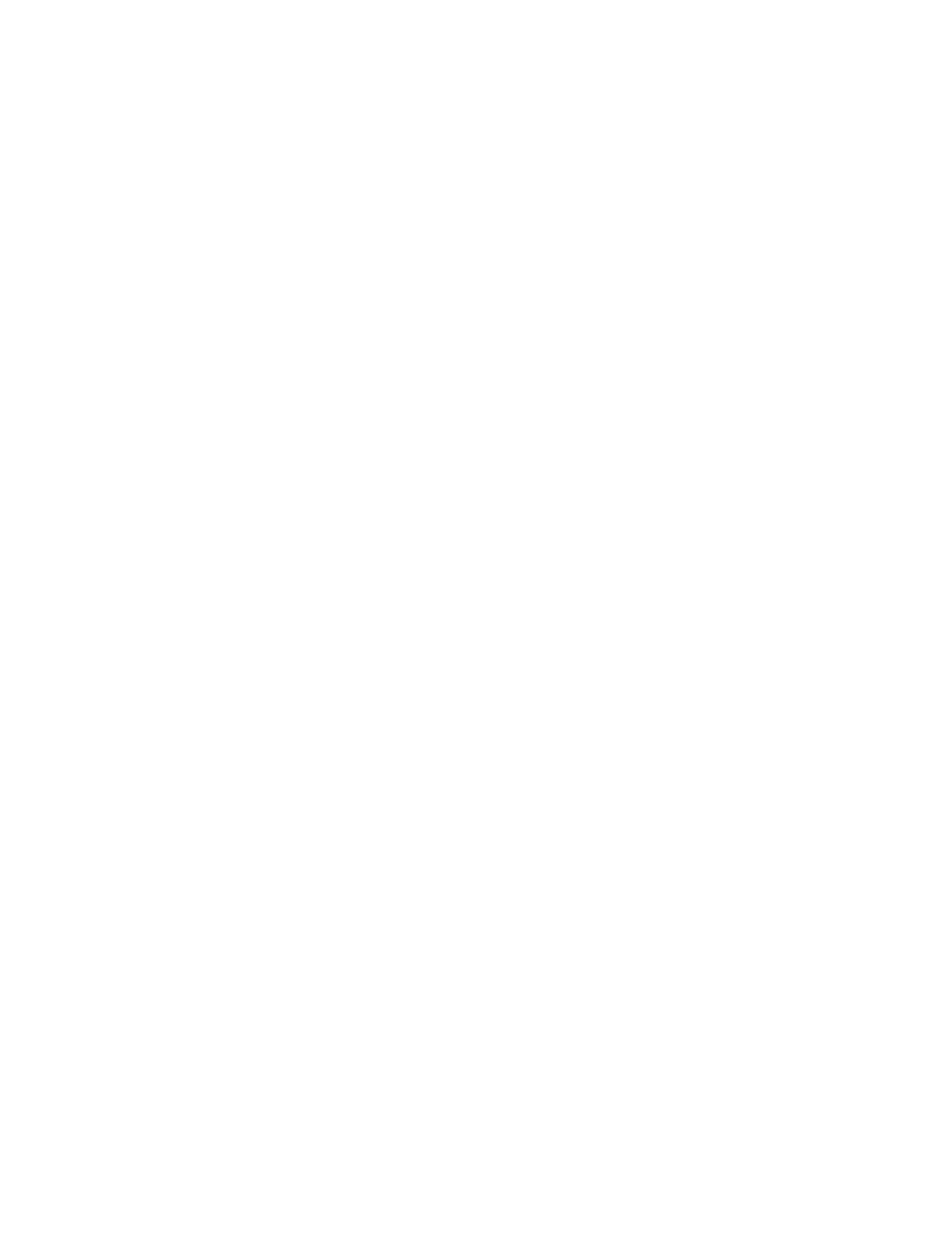
6
95-8472
3.1
Section II —
Installation and Startup
INSTALLATION
CAUTION
Always store and transport the sensor in the
original factory packaging to ensure proper
protection against contamination.
SENSOR LOCATION
Proper sensor positioning is essential to ensure maximum
gas detection capability. Optimum sensor placement
and density varies depending upon the conditions at
the job site. The system designer and installer must
examine the specific area to be protected and identify
the most likely leak sources and gas accumulation areas
to determine the best sensor locations.
The following factors should be considered for every
installation:
1. What kind of gas is to be detected? If it is lighter than
air (Acetylene, Hydrogen, Methane, etc.), place the
sensor above the potential gas leak. Place it close to
the floor for gases that are heavier than air (Benzene,
Butane, Butylene, Propane, Hexane, Pentane, etc.)
or for vapors resulting from flammable liquid spills.
Careful analysis of both the vapor hazard and the
application is required — first to determine the
feasibility of detection and then to ensure that proper
sensor locations are selected.
2. How rapidly will the gas diffuse into the air? Locate
the sensor as close as practical to the anticipated
source of a gas leak.
3. Ventilation characteristics of the immediate area must
also be considered. Air movement can cause the gas
to accumulate more heavily in one area than another.
Smoke generator tests are useful in identifying typical
air current patterns as well as “dead” air spots for
both indoor and outdoor applications. The sensors
should be placed where the most concentrated
accumulation of gas is anticipated.
4. The sensor should be located in an area where it
is safe from potential sources of contamination that
could poison the sensing element.
5. The sensor should be pointed down to prevent the
buildup of contaminants on the gas inlet.
6. The sensor must be accessible for testing and
calibration.
7. Exposure to excessive heat or vibration can result in
premature failure of electronic devices and should
be avoided if possible. Shielding the transmitter
from intense sunlight will reduce solar heating and
enhance the service life of the unit.
IMPORTANT
All diffusion-based gas sensors including the
catalytic gas sensor used with the Model 505
must contact the target gas in order to provide
an accurate gas measurement and response.
This must always be remembered when selecting
locations for gas sensor installation.
WIRING REQUIREMENTS
Wire Size and Type
The transmitter is typically connected to the controller/
power source using a three conductor shielded cable.
Shielded cable is highly recommended to protect against
interference caused by EMI and RFI. Cable shields
should be connected to earth ground at the transmitter
end only for maximum noise immunity. Shield termination
to ground at the controller end only is also acceptable,
but may offer reduced noise immunity.
The maximum allowable distance between the Model 505
and the output signal receiver (controller) is determined
by the wire size used. For the Model 505 with signal loop
impedance option “A,” the maximum loop resistance is
125 ohms. For the Model 505 with signal loop impedance
option “B,” the maximum loop resistance is 500 ohms.
Calculate the total linear distance and overall resistance
of the signal cable. Do not exceed the maximum loop
resistance for the Model 505 version being installed.
Power cable size must be adequate to ensure that no
less than the minimum operating voltage is delivered to
the transmitter under all operating conditions. Minimum
operating voltage for the Model 505 with signal loop
impedance option “A” is 10 Vdc, for the Model 505
with signal loop impedance option “B” it is 17 Vdc. A
linear, filtered and regulated 24 Vdc power supply is
recommended. Maximum wire size accepted by the
Model 505 wire terminals is 12 AWG (2.5 mm2). It is
acceptable to power the Model 505 from a 24 Vdc power
source that is remotely located from the output signal
receiver.
In applications where the wiring cable is installed in
conduit, the conduit should not be used for wiring to
other electrical equipment.