Dakota Ultrasonics CMX User Manual
Page 39
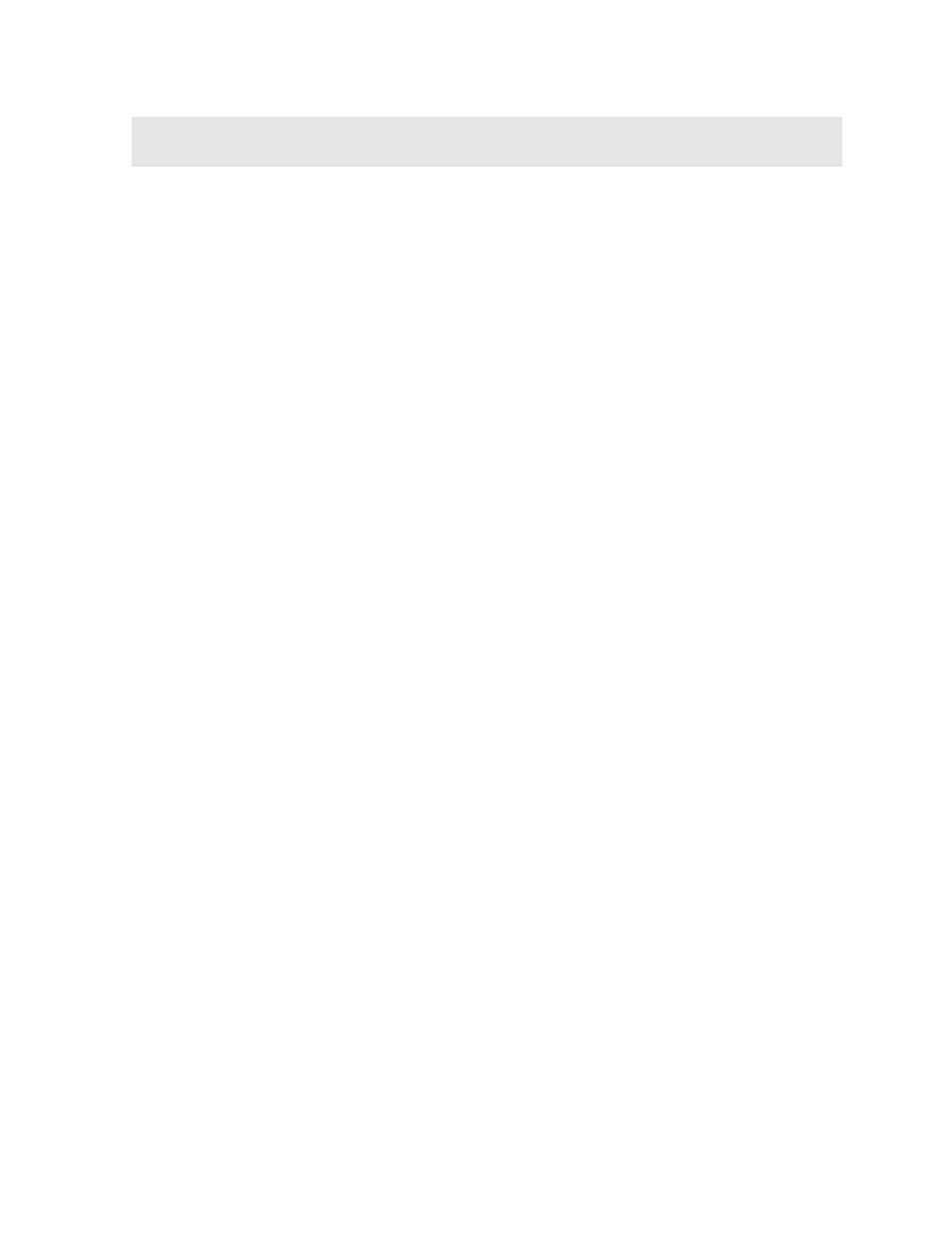
35
CHAPTER FIVE
SELECTING THE MEASUREMENT MODE
5.1 The setup library
The CMX contains 64 user configurable preset locations to store custom setups for
easy recall. These setups can be optimized for the user’s specific application needs
and can also be stored on a PC and transferred bi-directionally using Dakota’s PC
interface software included with the instrument.
The setups supplied with the instrument cover some of the more typical applications
commonly used with this type of instrument. These setups can be recalled, modified,
and overwritten to one of 64 setup locations. Therefore, these factory setups can
also be considered a good starting point to be modified for custom applications. The
PC software includes a default setup file that can be uploaded to the gauge at any
time to restore factory settings. However, it is recommended that the user consider
saving modified setups to an empty location rather than overwriting the factory setups
in the CMX. Once again, these factory settings are excellent starting points for
custom setups.
5.2 Which mode & transducer do I use for my application?
High penetration plastics and castings
The most common mode for these types of applications is pulse-echo. The CMX has
been optimized for cast materials. Cast iron applications require 1 - 5MHz
frequencies, and cast aluminum requires a 10MHz frequency. Plastics typically
require lower frequencies depending on the thickness and make-up of the material.
Larger diameters offer greater penetration power because of the crystal size, for
difficult to measure materials.
Corrosion & Pit Detection in steel and cast materials
Use pulse-echo mode whenever attempting to locate pits and flaws. Typically a
5MHz transducer, or higher, will be used for these types of applications. Use low
frequencies for greater penetration and use higher frequencies for better resolution.
Measuring Material & Coatings
The pulse-echo coating mode should be used when both material and coating
thickness are required, while still requiring the ability to detect flaws and pits. A
special coating style transducer is required for use in this mode. There are a variety
of coating transducers in various frequencies available from Dakota.