Carbolite HTR 11/150 User Manual
Page 6
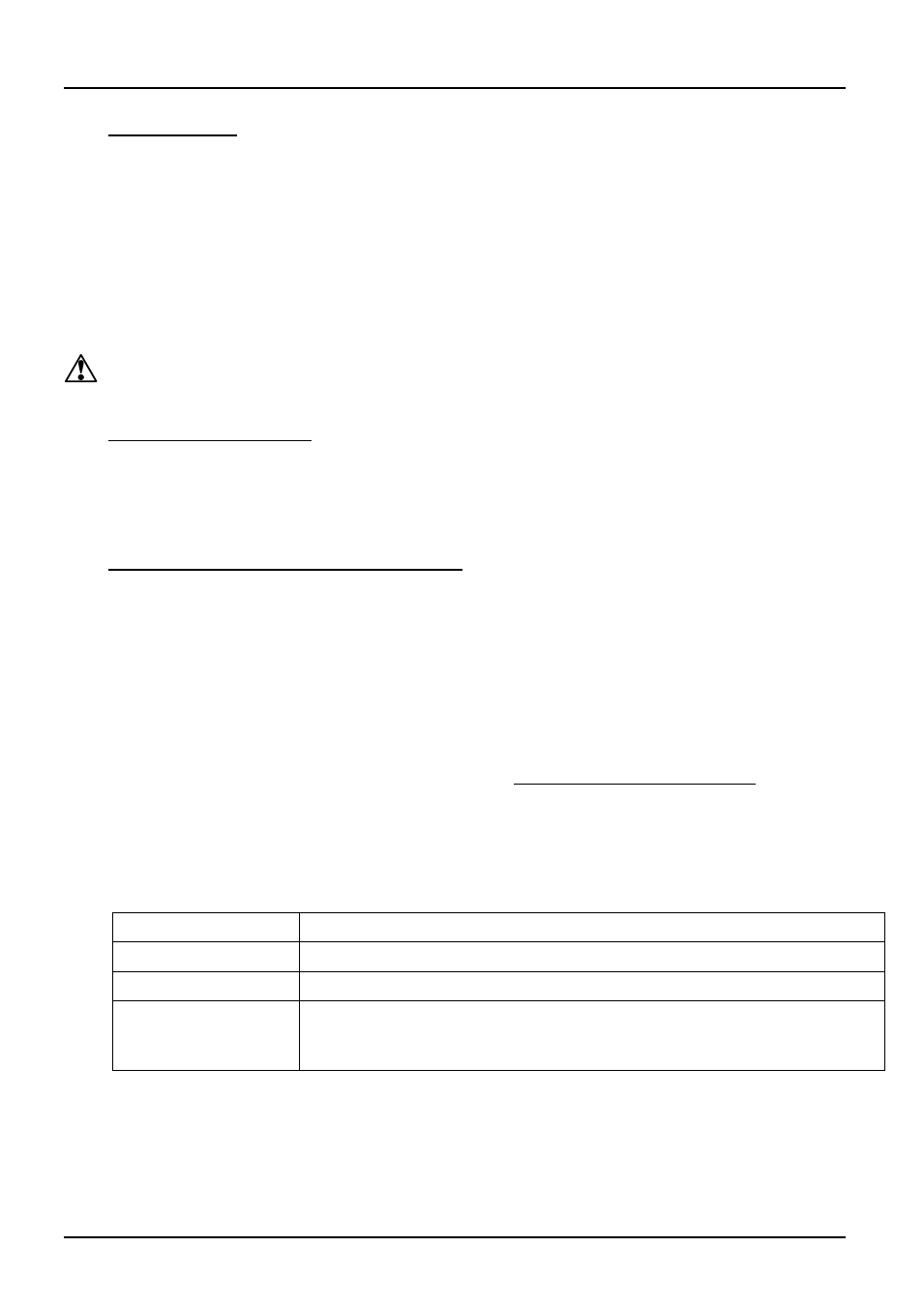
HTR
6
MF30 – 3.07
3.4 Operator Safety
The ceramic materials used in furnace manufacture become electrically conductive to some extent
at elevated temperatures. Do not insert conductive tools or items in the chamber without isolating
the elements. If a metal vessel is used, it should be guarded against being touched when the
furnace is on.
The elements are isolated when lid is open or the instrument switch is off. For full safety,
disconnect the furnace from the electrical supply.
Avoid burns. Use appropriate handling equipment, face masks, and heat resistant gloves. Before
you remove a hot vessel from the furnace make sure you have a safe place to put it down. Take
care: the vessel may be hot but look cold.
CAUTION: the furnace is designed for operators who understand their process. DO NOT use the
equipment with dangerous gases or materials without proper safety precautions. This is the
customer’s responsibility: Carbolite can only advise on precautions for specific processes if asked.
3.5 Care of the Vessel (Silica)
The fused silica (“quartz”) vessel is fragile and expensive: at all times take care in handling it.
Always make sure that there is somewhere safe to put it down before moving it.
Fused silica has a high resistance to thermal shock. Nevertheless, avoid sudden temperature
changes. For example: do not allow cold water to splash onto a hot vessel.
3.6 Devitrification and Chemical Attack (Silica)
Fused silica is liable to devitrify at high temperature. This is a recrystallisation process which is
greatly affected by surface conditions and therefore by contaminants in the furnace atmosphere. At
1000°C only a highly contaminated atmosphere has a noticeable effect, but at 1100°C the rate of
devitrification may become significant.
A devitrified vessel eventually fails. Failure is likely to be by cracking after cooling below 300°C.
Impurities such as alkali or alkaline earth ions, which occur in dust and perspiration, should be
avoided. It is advisable to handle the vessel with clean gloves or a dry cloth, and to touch the
central (hot) part as little as possible.
The silica vessel should be cleaned with pure alcohol, and wiped dry with a clean cloth.
The specific substances used by the customer’s process may, of course, be prime causes of
devitrification, as they may attack the vessel inner surface chemically and by abrasion. Carbolite
can advise, or seek external advice, on specific materials, if requested.
The following lists some elements and compounds known to cause devitrification. The list is not
exhaustive.
Severe below 1000°C
Na Fe Co Sn LiCl SnCl
3
Severe above 1000°C
Mg Ba Mn Cu Sb MgO BaCO
3
NaCl KCl CsCl BaCl
2
Less severe
Al As Sn(OH)
2
Ba(OH)
2
CaCO
3
CaCl
2
Not known to cause
devitrification up to
1100°C
Ca B Ti Zr V Nb Ta Cr Mo W Ni Ag Zn Cd Hg C Si
Pb S Se Ir H
2
O CaO Al
2
O
3
SiO
2
P
2
O
5
MoO
3
WO
3
ThO
2
RbCl NaBr Kbr NaI KI MgCl
2
AlCl
3
Some substances chemically attack silica. In particular, hydrofluoric acid attacks it at all
temperatures, and phosphoric acid above 150°C. Concentrated alkaline solutions may attack at
high temperatures, while carbon and some metals may cause reduction.