On 3.5, pa, On 3.5 – Carbolite EZS Series User Manual
Page 18
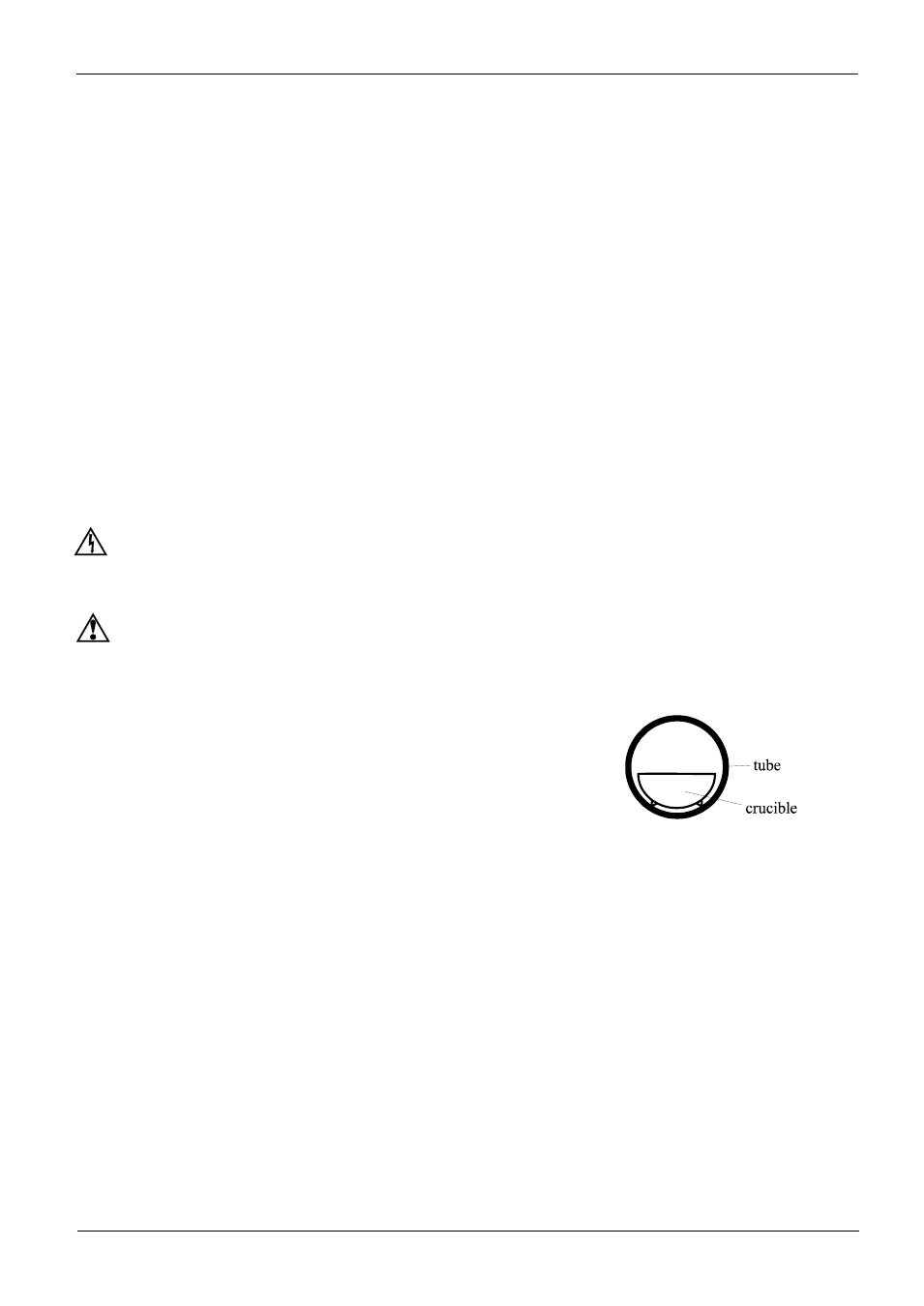
E range
18
MF65-1.01
MF65-1.00
It is possible to use local trim in the end zone controllers to enter a positive or negative adjustment
from the centre zone temperature. Once entered this trim will always be added or subtracted from
the retransmitted set temperature. In level 2 of the end zone controller (see controller operating
instruction), scroll to
LOC.T
(local trim) and use the Up Down enter the desired positive or
negative difference to be added to the end zone set temperature. There is no need to alter the centre
controller.
C.
Independent Control
In this case the three controllers are completely independent. Remember that it is not possible to
maintain very different zone temperatures because of heat transfer within the furnace body and
work tube.
3.4 General Operating Advice
Heating element life is shortened by use at temperatures close to maximum. Do not leave the
furnace at high temperature when not required. The maximum temperature is shown on the rating
label and in section 9.1 page 24 of this manual.
Light weight ceramic fibre insulation can easily be marked by accidental contact. Some fine
cracks may be visible on the surface of the insulation, or may develop in the surface of the
chamber due to the progressive shrinkage of the insulation materials. Cracks are not usually
detrimental to the functioning or the safety of the furnace.
3.5 Operator Safety
The ceramic materials used in furnace manufacture become electrically conductive to some extent
at high temperatures. Also, there are partially exposed heating coils in the chamber. DO NOT use
any conductive tools within the work tube without isolating it. If a metal work tube is used, it must
be earthed (grounded).
Switch off the Heater switch whenever loading or unloading the furnace. The elements are
isolated when the Heater switch is OFF (see Figure 1-1, page 3). This switch cuts both sides of the
circuit via a contactor
3.6 Work tube Life
A ceramic work tube may be cracked if work pieces are
inserted too quickly or at temperatures below 900°C when
the work tube is more brittle. Large pieces should also be
heated slowly to ensure that large temperature differences do
not arise.
Poor thermal contact should be encouraged between the work
piece and the work tube; crucibles or boats should be of low
thermal mass and should have feet to reduce the contact with
the work tube (Figure 3-2).
Do not set too high a heating rate. Large diameter work tubes are more susceptible to thermal
shock than smaller diameters. Work tubes that extend beyond the heated part of the furnace are
more at risk. A general rule for maximum heating rate is 400/internal diameter (°C/min); for
75mm i/d work tubes this comes to 5°C per minute. The controller can be set to limit the heating
rate.
3.7 Pressure
Work tubes are not able to accept high internal pressure. When gas seals or similar fittings are in
use, the gas pressure should be restricted to a maximum of 0.2 bar (3 psi). A pressure of about half
of that should normally be sufficient to achieve the desired flow rate. The customer must ensure
that the exhaust path from the work tube is not blocked, so that excess pressure does not occur.
3.8 Gas Tightness
IAP material work tubes are impervious; sillimanite may look similar but is porous. Ensure that
the correct work tube material is used before connecting and using any gases other than inert gases
such as nitrogen.
Figure 3-2. Diagram Showing Poor Thermal
contact of Work piece to Avoid Work tube
Cracking