Testing the actuator, Installation and bleeding – JLG 800A_AJ Service Manual User Manual
Page 255
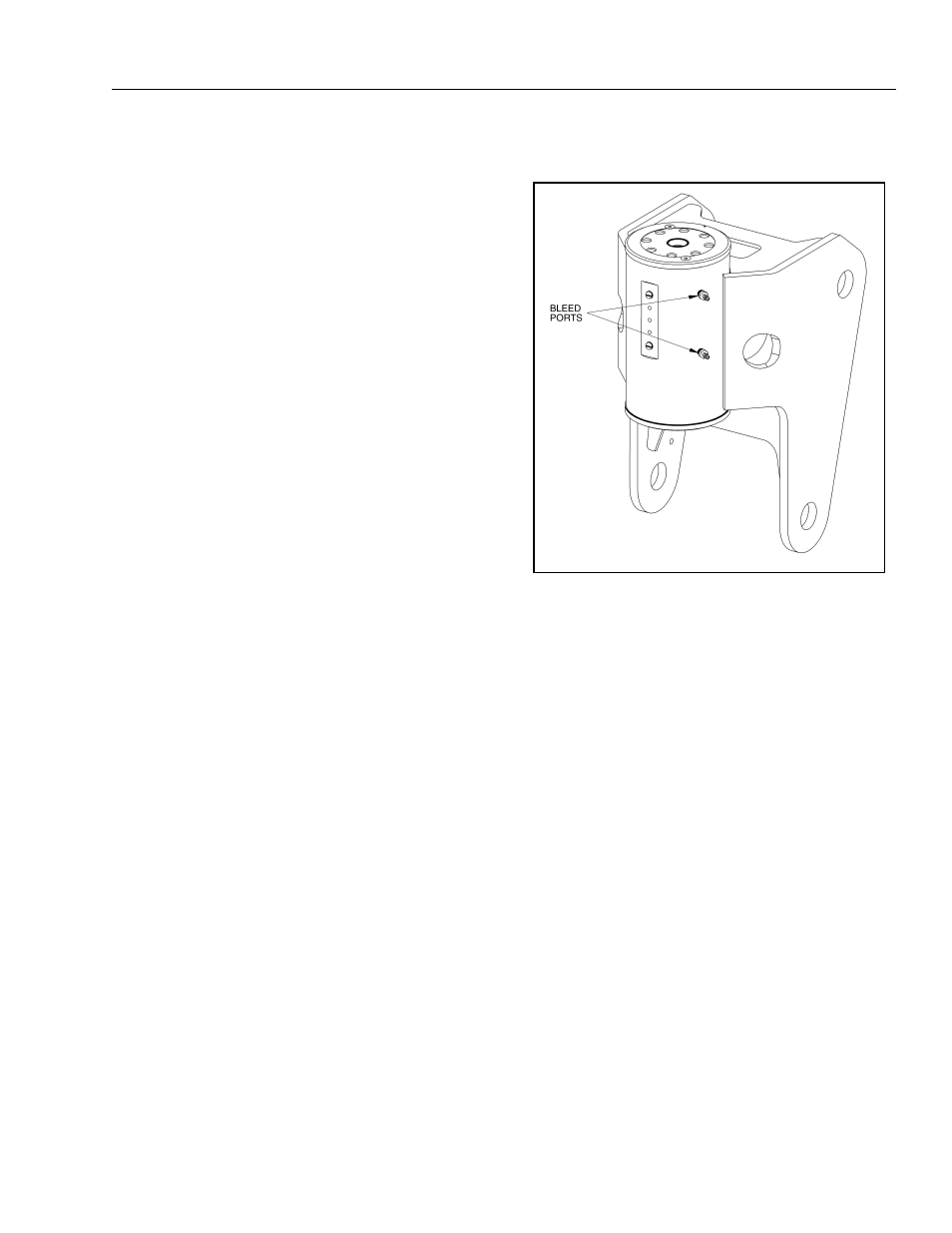
SECTION 4 - BOOM & PLATFORM
3120858
– JLG Lift –
4-41
Testing the Actuator
If the equipment is available, the actuator should be tested
on a hydraulic test bench. The breakaway pressure — the
pressure at which the shaft begins to rotate — should be
approximately 400 psi (28 bar). Cycle the actuator at least
25 times at 3000 psi (210 bar) pressure. After the 25 rota-
tions, increase the pressure to 4500 psi (315 bar) to check
for leaks and cracks. Perform the test again at the end of
the rotation in the opposite direction.
TESTING THE ACTUATOR FOR INTERNAL
LEAKAGE
If the actuator is equipped with a counterbalance valve,
plug the valve ports. Connect the hydraulic lines to the
housing ports. Bleed all air from the actuator (see Installa-
tion and Bleeding) Rotate the shaft to the end of rotation
at 3000 psi (210 bar) and maintain pressure. Remove the
hydraulic line from the non-pressurized side.
Continuous oil flow from the open housing port indicates
internal leakage across the piston. Replace the line and
rotate the shaft to the end of rotation in the opposite direc-
tion. Repeat the test procedure outlined above for the
other port. If there is an internal leak, disassemble, inspect
and repair.
Installation and Bleeding
After installation of the actuator on the equipment, it is
important that all safety devices such as tie rods or safety
cables are properly reattached.
To purge air from the hydraulic lines, connect them
together to create a closed loop and pump hydraulic fluid
through them. Review the hydraulic schematic to deter-
mine which hydraulic lines to connect. The linear feet and
inside diameter of the hydraulic supply lines together with
pump capacity will determine the amount of pumping time
required to fully purge the hydraulic system.
Bleeding may be necessary if excessive backlash is exhib-
ited after the actuator is connected to the hydraulic sys-
tem. The following steps are recommended when a
minimum of two gallons (8 liters) is purged.
1. Connect a 3/16" inside diameter x 5/16" outside
diameter x 5 foot clear, vinyl drain tube to each of the
two bleed nipples. Secure them with hose clamps.
Place the vinyl tubes in a clean 5-gallon container to
collect the purged oil. The oil can be returned to the
reservoir after this procedure is completed.
2. With an operator in the platform, open both bleed
nipples 1/4 turn. Hydraulically rotate the platform to
the end of rotation (either clockwise or counterclock-
wise), and maintain hydraulic pressure. Oil with
small air bubbles will be seen flowing through the
tubes. Allow a 1/2 gallon of fluid to be purged from
the actuator.
3. Keep the fittings open and rotate the platform in the
opposite direction to the end position. Maintain
hydraulic pressure until an additional 1/4 gallon of
fluid is pumped into the container.
4. Repeat steps 2 & 3. After the last 1/2 gallon is
purged, close both bleed nipples before rotating
away from the end position.
TYPICAL CONFIGURATION
OF ACTUATOR