Caterpillar – Class1 Throttle Information Reference User Manual
Page 9
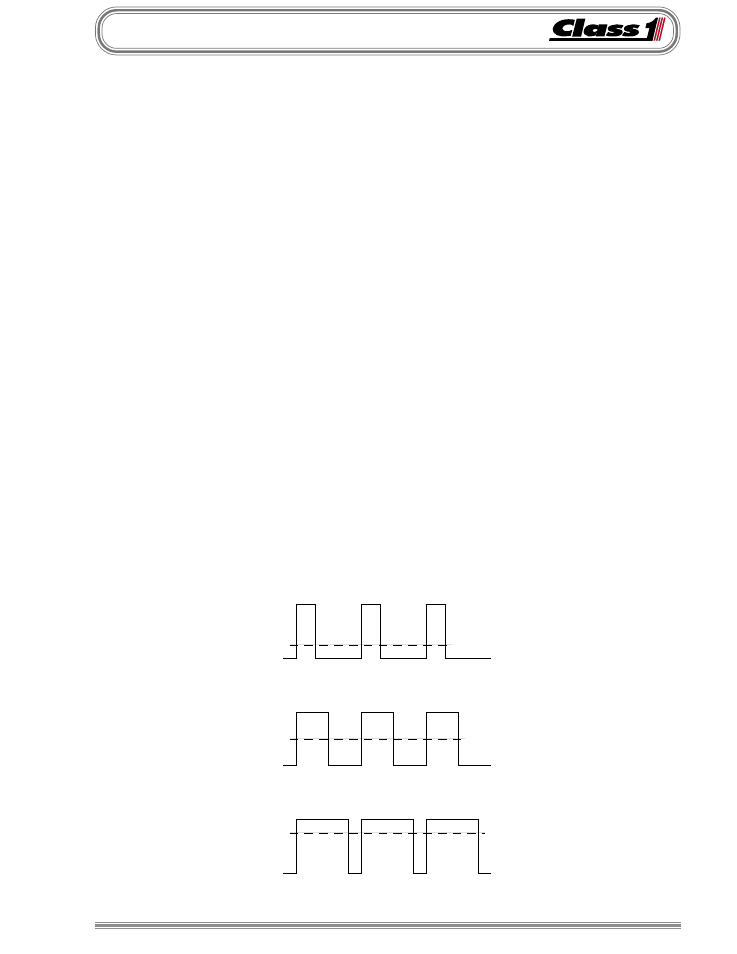
9
e:\manuals\throttles\LDSBBT.p65
Caterpillar
Caterpillar has several engine models that are used in fire apparatus.
The C-10 and C-12 engines along with the 3406E are identical for remote throttle and engine
ECM connections. They are in the process of changing over to the HEUI configuration and the
ECM connections will change from the 40 pin connectors (over and under) to the 70 pin side
by side connectors used on the newer ECMs. The 3116 and 3126 engines have two varia-
tions. The original 3116 and 3126 models are no longer being produced and will not be
addressed here to avoid confusion. The 3126B HEUI and 3116 B HEUI engines are the
current production models.
CAT remote throttle inputs require a pulse width modulated signal (PWM). The Class1 throttle
interface module converts the 0-5 Volt signal from a vernier control to an appropriate PWM
signal that is used to control engine RPM.
One note about the HEUI engines as currently delivered: They do not support oil pressure
information on the J-1587 data bus unless that feature is specifically ordered with the engine.
Class1 produces a module that delivers oil pressure to the information bus if an electronic
information center is desired and the oil pressure feature was not ordered with the engine.
CAT currently performs idle validation on the remote throttle signal on HEUI engines. This
means that there will be no throttle response if the control is left open or not closed properly
when the remote throttle is turned on at the engine ECM. To use the throttle, it must be closed
and then re-opened. The throttle interface module from Class1 also performs idle validation. If
necessary for operation, the module’s validation can be over-ridden by supplying 12 volts to
connector C-4 ( this is labeled high idle, but is actually the idle validation over-ride feature) at
the same time that the module is turned on.
Best operation is attained if the interface module is turned on concurrently with the engine
ECM. This method will work on all electronically controlled CAT engines. Safety Interlocking
should be performed on the PTO On/Off switch (multi-function input #1).
Engine specific wiring information provided on the following pages is as accurate as possible
at the time of publication. Bear in mind that engine control software is constantly changing
and revisions may show up that may result in unexpected or unexplained operation.
As always, the engine manufacturer’s dealers and publications are the best and most reliable
source for application specific operational information.
0.0 VDC
5.0 VDC
0.0 VDC
5.0 VDC
0.0 VDC
5.0 VDC
15% PWM approx. 0.75 VDC average
50% PWM approx. 2.50 VDC average
80% PWM approx. 4.0 VDC average