RMS Technologies R325 DRIVER W/PDT User Manual
Page 14
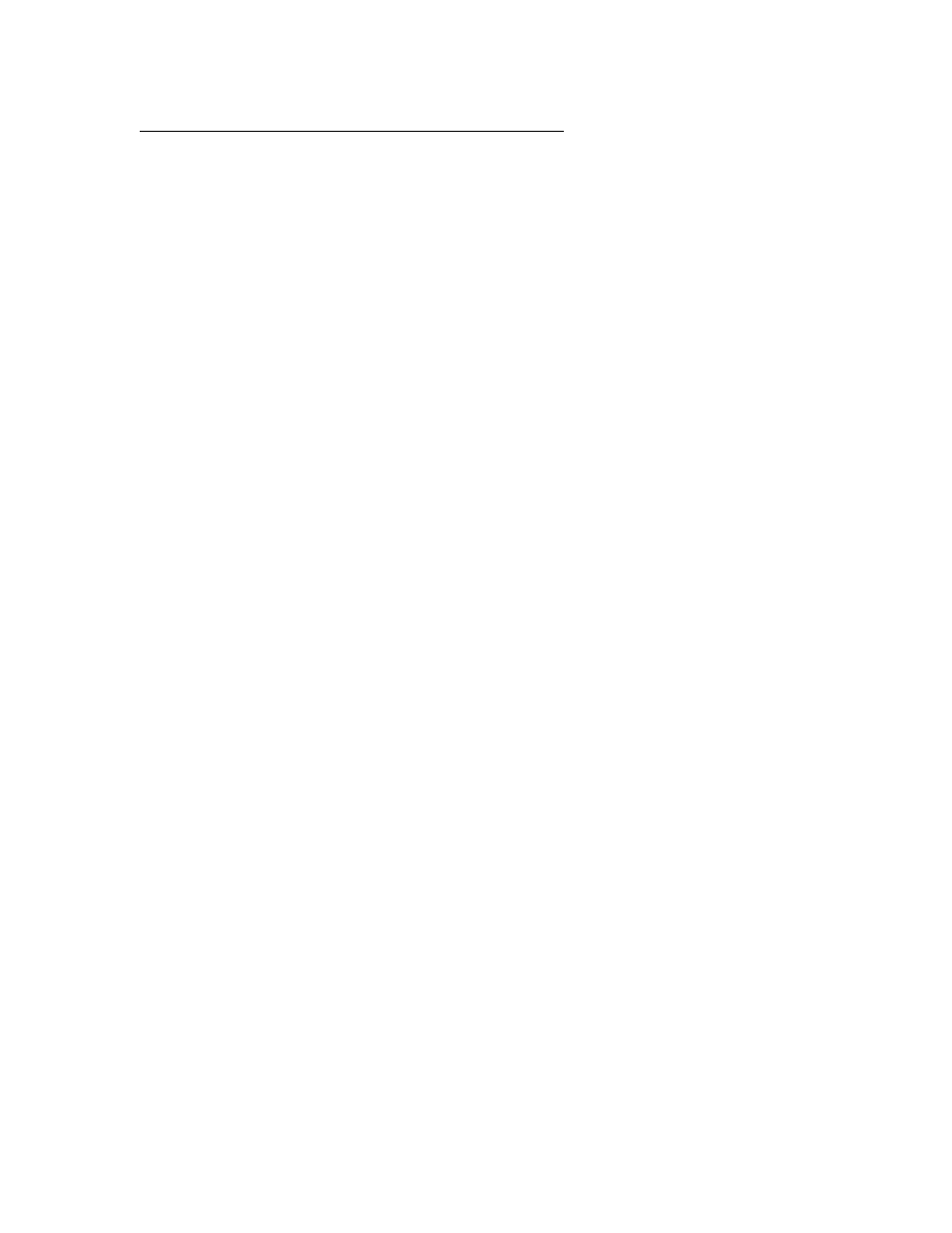
RMS Technologies
Page 14
Version 1.20
R325IE Single Axis Controller/Driver Manual
02/13/2006
8. BASIC STEP AND DIRECTION OPERATION
The four control signals Step, Direction, Disable, and Fault Out are optically isolated,
with a common positive connection (usually 5 VDC).
The common positive connection (Pin 1) is typically 5 VDC. Each of the inputs is set
to TRUE by supplying a signal level 5V below the common positive connection
powering the optical isolators. The input is set FALSE by putting the signal within 0.5
VDC below the common positive value.
Example: If 5 VDC is supplied to Pin 1 (common positive connection), TRUE is 0V,
and FALSE is any value between 4.5 VDC to 5 VDC.
For test purposes, and some applications where input isolation is not required, the
internal 5 VDC supply at Pin 4 of the I/O connector can be used as the common
positive connection, by linking pins 1 and 4 on the connector.
If this is done then each input is set TRUE by bringing the voltage level at the input
equal to, or more negative than the Power Supply negative connection at Pin 11.
With this arrangement Direction, Disable, and Fault Out control can be effected by
simple switch closure between the input and the power negative connection at Pin
11.
If the Step input is obtained from a Function Generator, then careful adjustment of
the Offset control is needed to ensure that the negative level of the input signal is
equal to, or more negative than, the power negative connection at Pin 11.
The minimum duration of the active (negative) Step input signal level is 400
nanoseconds and also this is the minimum for the inactive (positive) level. This limits
the maximum usable step rate to 2.5 MHz.
The optimum operating arrangement (minimum power usage) is for a constant width
negative going pulse of 400 nanoseconds with the pulse interval varying with pulse
rate.
For test purposes, setting the Function Generator duty cycle to 50%, and just
varying frequency is satisfactory.