RMS Technologies IMDE23 INTEGRATED MOTOR+DRIVER+ENCODER User Manual
Page 9
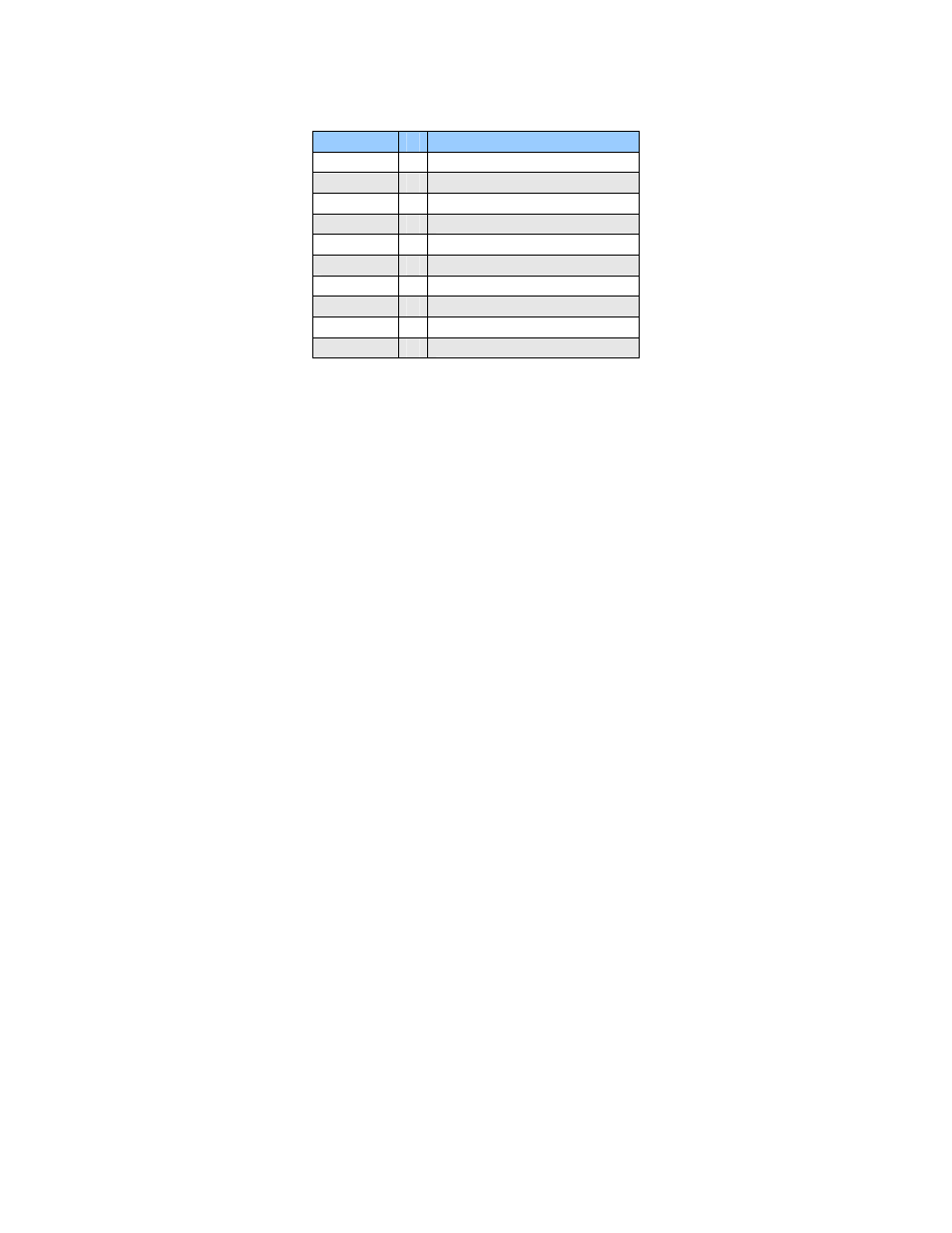
RMS Technologies
Page 9
Version 1.17
R164 Controller Manual
09/15/2005
Percent
Desired Current (Amps)
10% =
0.15
20%
=
0.30
30% =
0.45
40%
=
0.60
50% =
0.75
60%
=
0.90
70% =
1.05
80%
=
1.20
90% =
1.35
100%
=
1.50
Table 3: Desired Current
To achieve the equivalent Driver Current (Amps), multiply your motor’s
rated current by 1.4. Follow these examples:
Example One:
You have a motor that is rated at 0.85 Amps, 0.85 Amps x 1.4 = ~1.2 Amps. Using
Table 3 we would see that 1.2 Amps is 80% of the driver’s maximum output current.
Assuming the R164 Controller is addressed to Number 1, this is what you’d program:
/
1l80m80R
Example Two:
You have a motor that is rated at 1.0 Amps, and your Controller is addressed to
Number 1, this is what you’d program:
/1l95m95R
This will set the controller to 1.4 Amps Peak. How did we get 1.4 Amps? Æ 1.0
Amps x 1.4 = 1.4 A
Example Three:
You have a motor that is rated at 1.0 Amps, but you would like to run it at 1.0 Amps
Peak. Using Table 3 we would see that 1.05 Amps is 70% is the correct setting.
This is what you’d program:
/1l70m70R
Example Four:
You have a motor that is rated at 0.35 Amps, here is the MAXIMUM current you are
able to use:
/1l33m33R
Programming anything higher than this will damage the motor.
WARNING!: Setting the Current to a value greater than the Motor’s rated
current will damage your motor, and may overheat the controller.