Freeze protection – COOK ERV Fluid Coil Supplement User Manual
Page 2
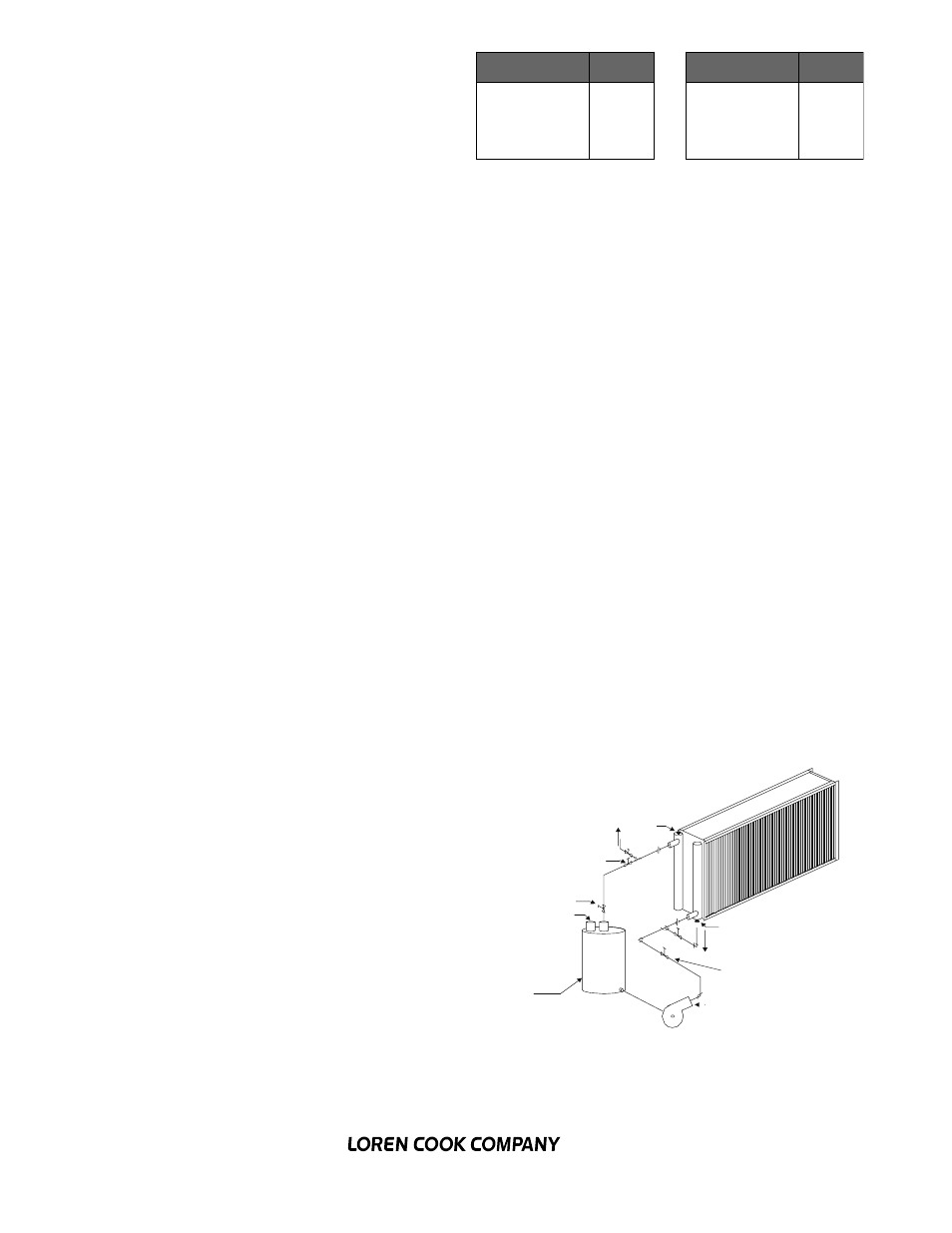
2
maintain maximum coil performance and service life.
2.
Periodic inspection of the coil for signs of corrosion and/or
leaks is recommended. Repair and replacement of the coil and the
connecting piping, valves, etc., should be performed as needed by
a qualified individual(s).
3.
Should the coil surface need cleaning, caution should be
exercised in selecting the cleaning solution as well as the cleaning
equipment. Improper selection can result in damage to the coil
and/or health hazards. Clean the coil from the leaving air-side so
that foreign material will be washed out of the coil rather than
pushed further in. Be sure to carefully read and follow the manu-
facturer’s recommendations before using any cleaning fluid.
4.
Maintain the circulated fluid free of sediment, corrosive
products and biological contaminants. Periodic testing of the fluid
followed by any necessary corrective measures along with main-
taining adequate fluid velocities and proper filtering of the fluid will
help to satisfy this goal.
5.
If automatic air vents are not utilized, periodic venting of the
coil is recommended to remove accumulated air. Caution should
be exercised to avoid injury. High pressure and/or high tempera-
ture fluids can cause serious personal injury.
Freeze Protection
During the winter, chilled water coils need to be protected
against freezing. The two predominant protective measures are
covered below.
Blowing-Out Coils
1.
Isolate the coil from the rest of the system by closing the
valves on both the supply and return lines (gate valves in Figure 2
- Horizontal Airflow Diagram).
2.
Drain the coil by opening all drain valves and/or the drain
plug. Remove the vent plug to aid the draining process.
3.
Once the coil has been fully drained, the blower can be
hooked-up. Caps installed in the piping on straight runs going to
the supply and return connections are ideal points to hook-up the
blower. The air vent and drain plug are not suitable locations for
hooking up the blower. Caution should be exercised when install-
ing the blower. The blower operator must take precautions to
insure that water does not come into contact with any of the elec-
trical components of the blower. Failure to do so may result in
damage to the equipment and serious injury.
4.
Close the vent or drain plug on the header which the blower
is connected and open the drain valve or cap on the other header.
5.
Operate the blower for 45 minutes and then check the coil to
see if it is dry. A mirror placed in the discharge will become fogged
if moisture is present. Repeat this procedure until the coil is dry.
6.
Let the coil stand for several minutes then blow it out again. If
water comes out, repeat the blowing operation.
7.
Leave all plugs out and drains open until the threat of freez-
ing has passed.
Flushing Coils
1.
Recommend the use of inhibited glycol designed for HVAC
applications for corrosion protection. The use of uninhibited glycol
has produced formicary corrosion in copper tubing. The complete
filling of water coils with an inhibited glycol solution for freeze pro-
tection can be expensive. In some instances, it is more cost effec-
tive to flush the coils with an appropriate concentration of inhibited
glycol solution. Residual fluid can be left in the coil without the
threat of freeze damage provided the correct concentration of
inhibited glycol was used. The recovered fluid can then be used to
flush other coils. Select an inhibited glycol solution that will protect
the coil from the lowest possible temperatures that can occur at
the particular coil’s locality. The following tables have been pro-
vided for your convenience.
Corporate Offices:
2015 E. Dale Street
Springfield, MO 65803 417.869.6474
lorencook.com
2.
Estimate the volume of the coil in gallons.
For 5/8” tubes (1.5” face tube spacing)
(finned height in inches)x(finned length in inches)x(# of
rows)x 0.0011 = gallons
For 1/2” tubes (1.25” face tube spacing)
(finned height in inches)x(finned length in inches)x(# of
rows)x 0.00083 = gallons
3.
Isolate the coil from the rest of the system by closing the
valves on both the supply and return lines (gate valves in Figure
1 - Horizontal Airflow).
4.
Drain the coil by opening all drain valves and/or the drain
plug. Remove the vent plug to aid the draining process.
5.
Close the drain valve(s) and drain plug.
6.
Connect the flushing system to the coil. A typical system is
shown in Figure 3 - Flushing System Diagram.
7.
With the throttling valve closed, start the pump and oper-
ate until the air is vented from the coil. Next, close the air vent.
8.
Open the throttling valve about half-way and circulate the
fluid through the coil for 15 minutes. Check the strength of the
fluid. A hydrometer or test kit from the fluid manufacturer is suit-
able for this application.
9.
Adjust the solution strength as needed and circulate the
fluid for another 15 minutes.
10.
Repeat steps 8 and 9 until the desired concentration is
reached.
11.
Shut the pump down and drain the inhibited glycol from
the coil.
12.
The recaptured fluid can be used to flush other coils.
Note:
Be sure to follow the manufactures’ recommendations
before utilizing any glycol based antifreeze solution. Additional
fluid will be required for the pump, connected piping and fluid
reservoir. Formulae are for estimation purposes only.
y
B
l
o
c
y
l
G
e
n
e
l
y
h
t
E
%
e
m
u
l
o
V
e
z
e
e
r
F
t
n
i
o
p
1
y
B
l
o
c
y
l
G
e
n
e
l
y
p
o
r
P
%
e
m
u
l
o
V
e
z
e
e
r
F
t
n
i
o
p
1
o
2
3
o
2
3
o
5
2
o
6
2
o
6
1
o
9
1
o
3
o
8
o
3
1
-
o
7
-
o
4
3
-
o
8
2
-
o
5
5
-
o
0
6
-
0
10
20
30
40
50
60
F
F
F
F
F
F
F
0
10
20
30
40
50
60
F
F
F
F
F
F
F
Shut-off Valve
w/Hose Connection
Throttling
Valve
Vent
Hole
Inhibited
Glycol
Reservoir
Pump
Shut-off Valve
w/Hose Connection
Drain
Vent
Figure 3 - Flushing System Diagram
ERV Fluid Coil IOM Supplement- December 2002