Internal cascade, External cascade, Setpoint master control – Red Lion PCU User Manual
Page 5
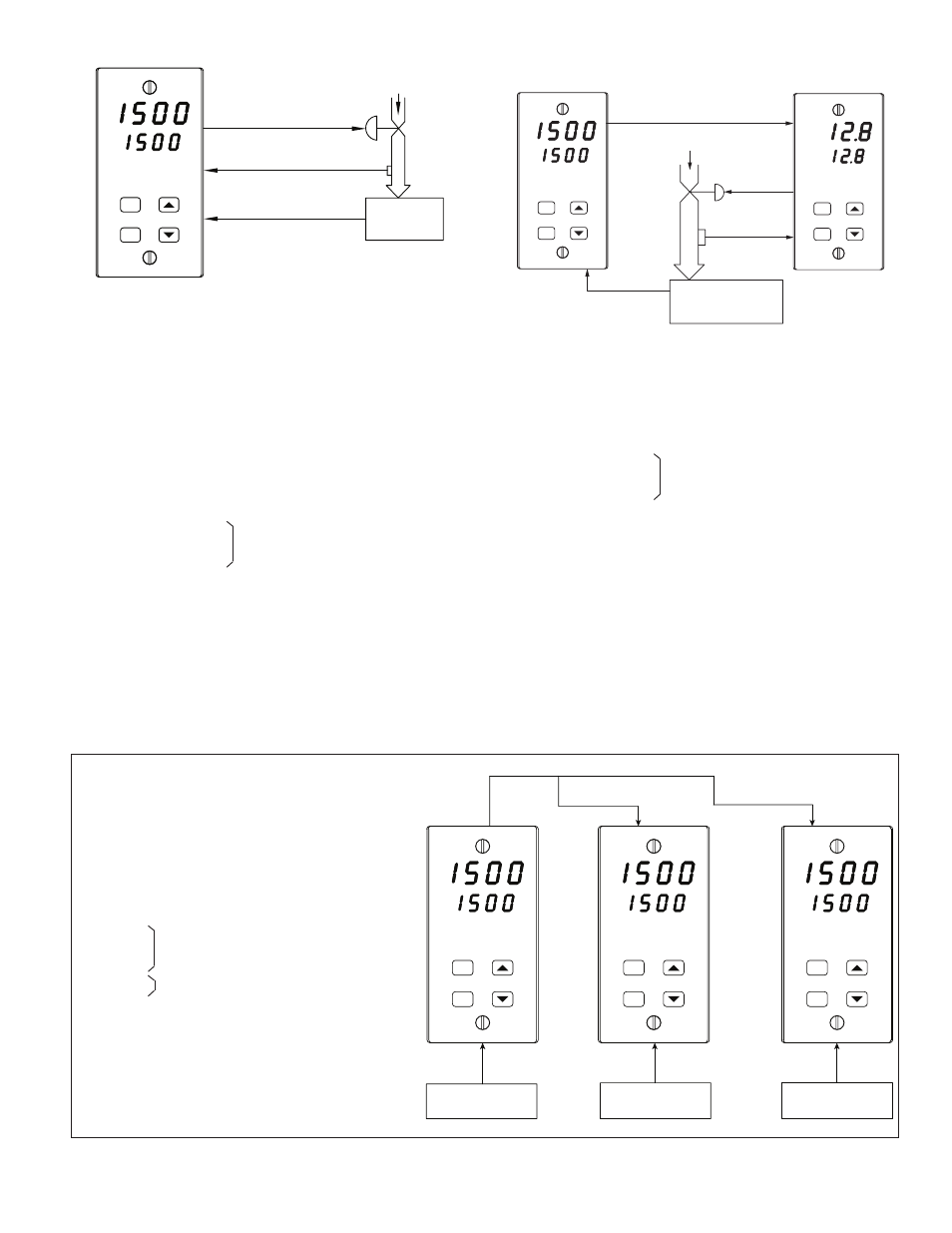
5
INTERNAL CASCADE
Cascade control allows the process to be divided into two control loops: the
primary control loop and the secondary control loop. The secondary loop receives
its setpoint from the primary loop to control an intermediate variable (steam
pressure). The control level of the intermediate variable is the input to the primary
process. The primary loop (main input) controller maintains loop regulation by
manipulating the setpoint of the secondary controller. The setpoint of the
secondary controller, in turn, changes the intermediate variable. The secondary
loop can react faster to disturbances of the intermediate variable, thereby
minimizing the effects to the primary control loop. Control loops cascaded in such
a manner provide greater control quality than would be possible with single loop
control. A single PCU can accomplish two-process cascade control.
Internal Cascade Configuration Parameters
“OPEr”
- Select cascade mode
“root”
- Select second input square root linearization
“dPt2”
- Select second input decimal point
“dSP1”
“INP1”
“dSP2” - Enter scaling units of second input
“INP2”
“OPd2”
- Output dampening of secondary
Internal Cascade Operational Parameters
“SP-2”
- View secondary setpoint value
“Pb-2”
- Enter secondary proportional band
“It-2”
- Enter secondary integral time
“dt-2”
- Enter secondary derivative time
EXTERNAL CASCADE
Similar to internal cascade control, external cascade control differs by the
employment of two controllers, one of which is equipped with a second analog
input configured as a remote setpoint. A PCU controls the secondary loop, while
a TCU controls the primary loop.
External Cascade Configuration Parameters
“OPEr”
- Select ratio mode
“root”
- Select second input square root linearization
“dPt2”
- Select second input decimal point
“dSP1”
“INP1”
“dSP2” - Enter scaling units of second input
“INP2”
“SPtr”
- Local/Remote select options
External Cascade Operational Parameters
“rtio”
- Remote setpoint ratio
“bIAS”
- Remote setpoint bias
DSP
PAR
%PW
SEC
REM
OP1
AL1
AL2
LINEAR DC OUTPUT
SECOND INPUT
STEAM PRESSURE
STEAM
FLOW
PROCESS
MAIN INPUT
(SECONDARY VARIABLE)
(PRIMARY VARIABLE)
DSP
PAR
%PW
DEV
MAN
OP1
AL1
AL2
OP1
REM
DSP
PAR
SEC
%PW
AL2
AL1
CONTROLLER
CONTROLLER
LINEAR DC
(PRIMARY OUTPUT)
SECOND INPUT
REMOTE SETPOINT
STEAM
LINEAR DC
OUTPUT
MAIN INPUT
PROCESS TEMPERATURE
(PRIMARY VARIABLE)
PROCESS
MAIN INPUT
STEAM PRESSURE
(SECONDARY VARIABLE)
PCU
TCU
SECONDARY
PRIMARY
DSP
PAR
%PW
SEC
REM
OP1
AL1
AL2
DSP
PAR
DEV
%PW
OP1 AL2
MAN AL1
REMOTE SETPOINT
MASTER
UNIT
SLAVE
UNIT #1
PROCESS #1
PROCESS #2
MAIN
INPUT
MAIN
INPUT
SECOND INPUT
%PW REM AL1
AL2
MAIN
INPUT
PROCESS "N"
DSP
PAR
OP1
SEC
REMOTE SETPOINT
SECOND INPUT
(UP TO 50)
SLAVE
UNIT `N'
LINEAR DC OUTPUT SETPOINT RE-TRANSMISSION
SETPOINT MASTER CONTROL
Setpoint Master Control allows automatic setpoint changes to
slave controller units (up to 50 units total) from a master PCU
controller. The linear DC output of the master is looped with the
second analog input of the slave PCU controllers. Each slave unit
can have unique remote setpoint ratio and bias values.
Setpoint Slave Configuration Parameters
“OPEr”
- Select remote setpoint mode
“root”
- Select second input square root
linearization
“dPt2”
- Select second input decimal point
“dSP1”
“INP1”
“dSP2”
- Enter scaling units of second input
“INP2”
“SPLO”
“SPHI”
- Limit range of remote setpoint
“SPrP”
- Limit rate of change of remote
setpoint
Setpoint Slave Operational Parameters
“rtio”
- Second input ratio
“bIAS”
- Second input bias