Hardware features, Setpoint features, Input features – Red Lion PCU User Manual
Page 4: Output features, Auto-tune, Options, Ratio control, Motorized valve positioner
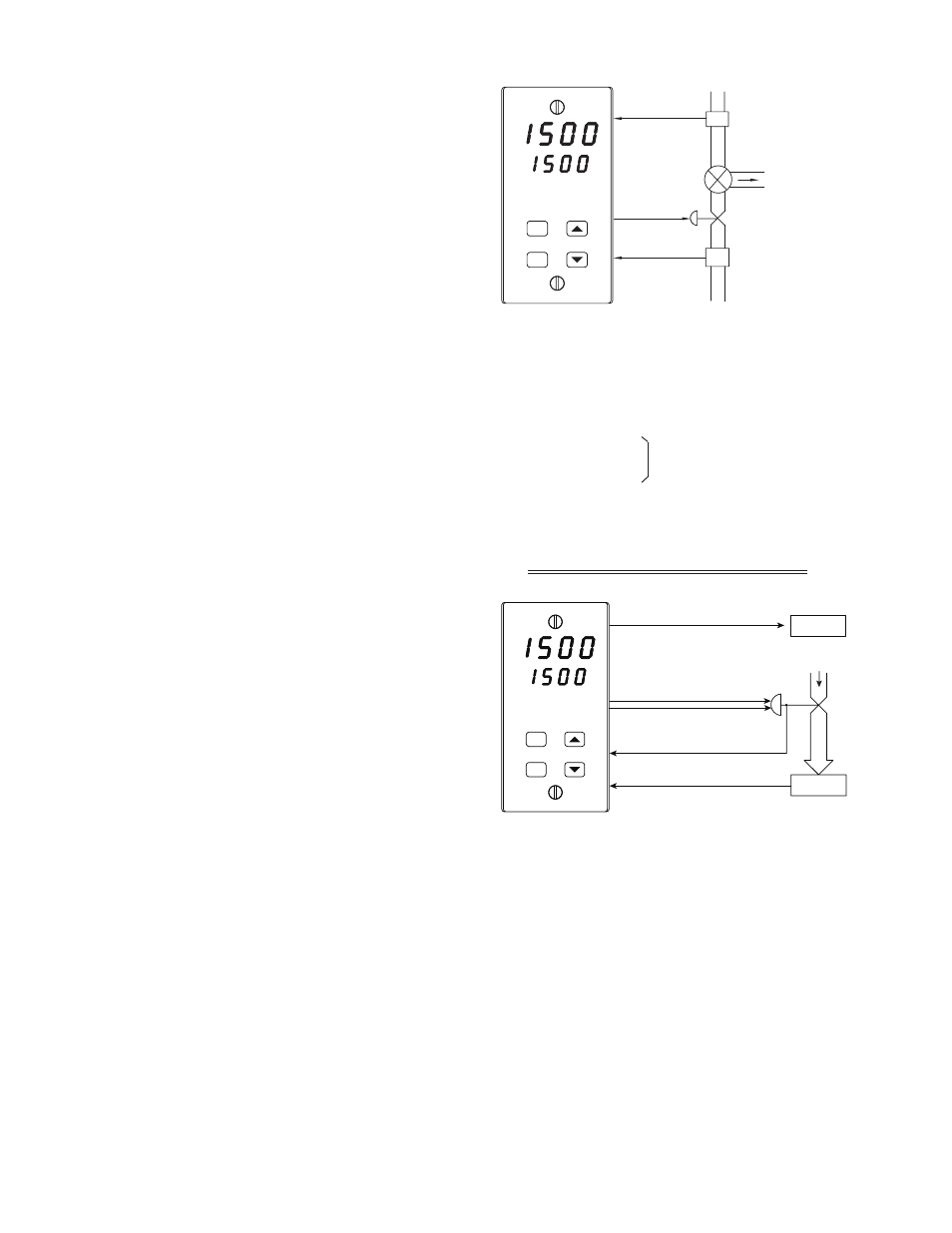
4
HARDWARE FEATURES
The fast 100 msec input sampling rate provides quick controller response to
a process disturbance, thus providing excellent process control. Measurement
accuracy of 0.15% or better, provides closer process control conforming to the
desired control setpoint value. The unit accepts either a 0 to 10 VDC or a 0 to
20 mA DC input signal. The AC input power is switch selectable, allowing the
unit to operate from either 115 VAC or 230 VAC. Since the controller is
serviceable from the front of the panel, the output modules may be easily
changed or replaced without disturbing the wiring behind the panel. No
re-programming is required when changing or replacing modules.
The optional Type 4X/IP65 rated model utilizes two bezel securing screws
and a neoprene gasket to guarantee a water tight seal, when properly installed.
The standard model simply requires pressing a latch to remove the unit.
Low-drift, highly stable circuitry ensures years of reliable and accurate
process control. The recommended two-year re-calibration interval is easily
accomplished via the programming menu.
SETPOINT FEATURES
The controller setpoint can be protected from out of range values by
programming the setpoint range limit values. Additionally, safeguards from
inadvertent data entry can be programmed.
The setpoint ramp feature ramps the setpoint value at start-up or any time a
setpoint change is made, at a user programmable rate. This feature reduces
shock to the process and helps to minimize overshoot. The setpoint may also be
transmitted by the optional linear DC output for slave control loops.
The second analog input may be configured as a remote setpoint. As such, the
controller is easily switched from local/remote setpoint operation via the front
panel or user input. Ratio and bias parameters provide on-line scaling of the
remote setpoint. Absolute limit values and maximum rate of change of the
remote setpoint further enhance controller flexibility.
INPUT FEATURES
A programmable input filter can be used to stabilize readings from a process
with varying or oscillating characteristics, helping to provide better process
control. Programmable scaling points allow the controller to display in any
engineering unit; flow, level, pressure, etc. Scaling points are used in
conjunction with the programmable rounding increment to stabilize a jittery or
otherwise hard to read process signal for better indication.
The programmable User Input can be used to control a variety of functions,
such as auto/manual transfer of the controller, reset alarm output(s), etc.
The second analog input has independent scaling parameters to match the
units of other processes or transmitters, or to match the controller’s range.
OUTPUT FEATURES
Programmable output power limits provide protection for processes where
excessive power can cause damage. Automatic signal overdrive detection, for
fail-safe operation, causes the controller to default to a programmed output
power (upscale or downscale burnout). With adjustable time proportioning
cycle time, and programmable DC linear output, the controller can satisfy a
wide variety of output requirements.
Programmable dampening output hysteresis and output update time parameters
can dramatically reduce actuator activity without degrading control accuracy.
The RS485 Communication option allows the user to access various
controller parameters such as the setpoint, % output power, % proportional
band, etc. The controller may be set up to transmit various parameters at a
programmable automatic print rate.
AUTO-TUNE
The PCU has an auto-tune feature that, on demand, automatically determines
the PID control parameters for a particular process. After completion of auto-
tune, the PID parameters are automatically optimized for that process and
loaded into nonvolatile memory. The operator may view and modify the
parameters as desired.
Auto-tune may be invoked either at start-up or at setpoint, depending on the
process requirements. An auto-tune programmable dampening factor produces
various levels of process control and response characteristics.
OPTIONS
RATIO CONTROL
The PCU configured for ratio operation controls a process as a ratio of
another process or to another variable. Ratio control is commonly used for flow
applications, however, any two process variables can be controlled in a
ratio mode.
Ratio Control Configuration Parameters
“OPEr”
- Select ratio mode
“root”
- Select second input square root linearization
“dPt2”
- Select second input decimal point
“dSP1”
“INP1”
“dSP2” - Enter scaling units of second input
“INP2”
“SPtr”
- Local/Remote Select options
“InPt”
- Program User Input for Local/Remote
Setpoint selection
Ratio Control Operational Parameters
“rtio”
- Remote setpoint ratio
“bIAS”
- Remote setpoint bias
MOTORIZED VALVE POSITIONER
The motorized valve positioner controls the position of a valve directly, by
use of “open” and “close” control outputs. The slidewire feedback signals of
the valve may optionally be connected to the controller. Alternatively, the
controller may be configured for linear input valve control using the 4 to 20 mA
DC output.
Motorized Valve Positioner Configuration Parameters
Position mode: “VPS1”
- Enter or measure valve closed position
“VPS2”
- Enter or measure valve open position
“VUdt”
- Enter Valve update time
“VPdb”
- Enter valve control deadband
“VFAL”
- Enter valve fail detect time
“Act1”
- Program alarm as valve fail output
Velocity mode: “VUdt”
- Enter Valve update time
“VOPt”
- Enter valve open time
“VCLt”
- Enter valve close time
“VOnt”
- Enter valve control deadband
(minimum on time)
DSP
PAR
%PW
SEC
REM
OP1
AL1
AL2
SECOND INPUT
UNCONTROLLED
FLOW
LINEAR DC
OUTPUT
MAIN INPUT
CONTROLLED
FLOW
FLOW C = FLOW A + FLOW B
FLOW A
FLOW B = [RATIO * FLOW A] + BIAS
DSP
PAR
%PW
DEV
MAN
AL1
OPN
CLS
VALVE OPEN OUTPUT
VALVE CLOSE OUTPUT
SECOND INPUT
VALVE POSITION
MAIN INPUT
PROCESS
STEAM FLOW
VALVE FAIL
ALARM
AL1 OUTPUT