Safety summary, Specifications – Red Lion PCU User Manual
Page 2
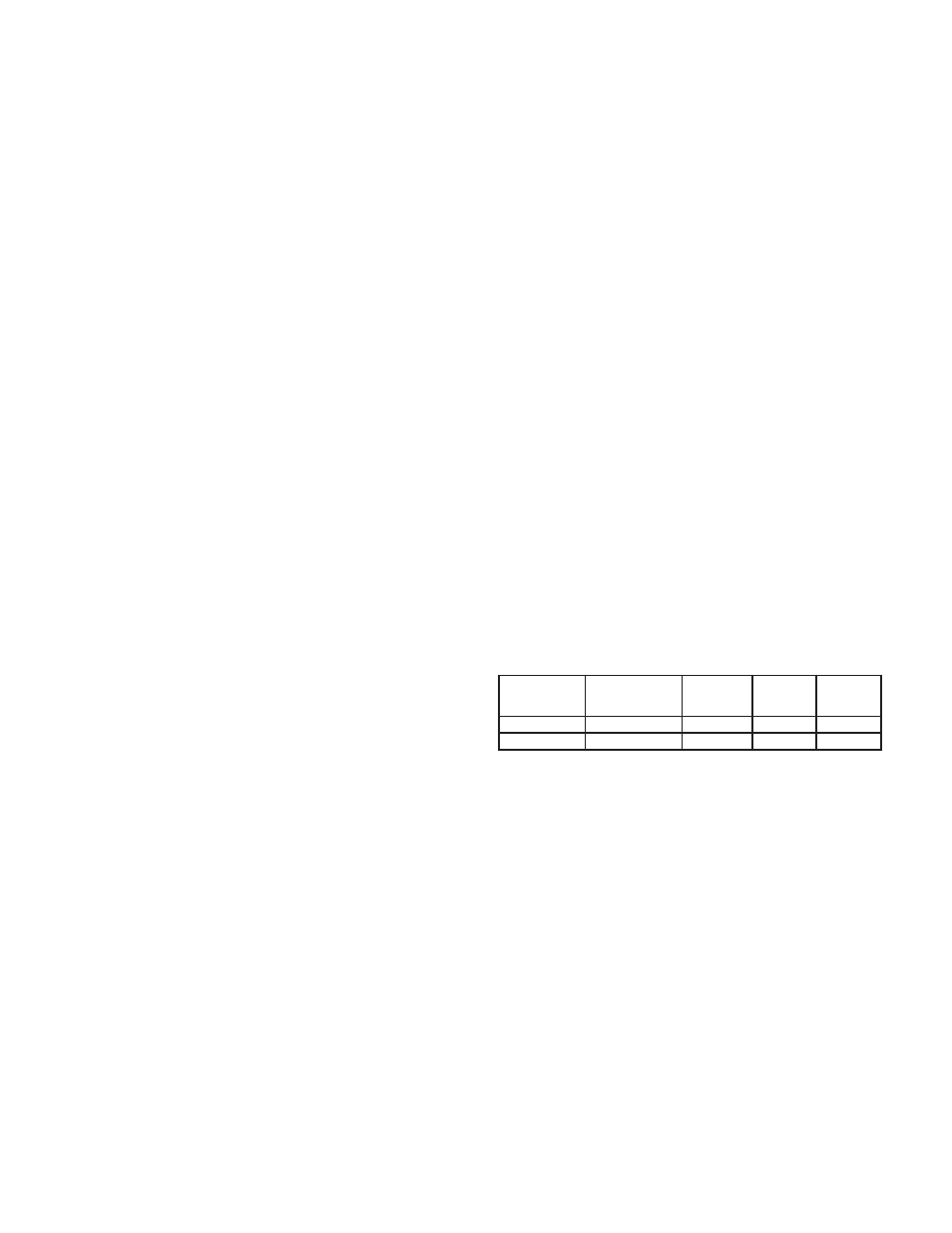
2
OPTIONS
Optional dual alarms can be configured to activate according to a variety of
actions (Absolute HI or LO, Deviation HI or LO, Band IN or OUT and Valve
Fail Detect) with adjustable hysteresis. A standby feature suppresses the output
during power-up until the process stabilizes outside the alarm region. An
optional secondary output is available (for processes that require cooling) that
provides increased control accuracy and response.
A linear 4 to 20 mA or 0 to 10 VDC output signal is available to interface
with actuators, chart recorders, indicators, or other controllers. The output signal
can be digitally scaled and selected to transmit one of the following: % output
power, measurement value, process measurement value deviation or setpoint
value. Valve Positioner and Second Analog Input Models have the adjustable
output demand dampening, output deadband and output update time parameters
to expand the versatility of the PCU to control devices.
The optional Motorized Valve Positioner directly controls the position of a
valve by the use of twin outputs (open and close) to control the direction of
motor rotation. The motor position defines the opening position of the valve.
Two control modes are possible: position control, that makes use of the
slidewire feedback signal supplied with the positioner and velocity control, in
which no slidewire feedback signal is used. Parameters are provided to adjust
the operation of the valve. These include:
- Valve activity hysteresis
- Valve update time
- Variable control dampening
- Slidewire signal fail action
- Adjustable valve position limits
The Valve Positioner PCU achieves tight process control, yet minimizes
unnecessary valve activity. An alarm event output or display alarm can be
programmed under loss of slidewire feedback or under valve fail detection.
The optional Second Analog Input (0 to 20 mA DC) can be configured as a
remote setpoint signal or as a secondary process signal. Configuration of the
second analog input as a remote setpoint signal allows ratio control, master
setpoint/multiple slave operation, and the ability to cascade the PCU with
another controller (external cascade). Configuration of the second input as a
secondary process signal allows operation as a two-process cascade controller
within a single unit (internal cascade). In either control mode, parameters are
provided to scale, configure, communicate and monitor the activity of both
analog inputs. A square law linearizer function can be used to linearize signals
derived from flow transmitters.
The optional RS485 multidrop serial communication interface provides two-
way communication between a PCU unit and other compatible equipment such
as a printer, a programmable controller, or a host computer. In multipoint
applications the address number of each unit on the line can be programmed
from zero to ninety-nine. Up to thirty-two units can be installed on a single pair
of wires. The Setpoint value, % Output Power, Setpoint Ramp Rate, etc. can be
interrogated or changed by sending the proper command code via serial
communications. Alarm output(s) may also be reset via the serial communications
interface option.
An optional Type 4X/IP65 rated bezel is available for wash down and/or dirty
environments, when properly installed. Modern surface-mount technology,
extensive testing, plus high immunity to noise interference makes the controller
extremely reliable in industrial environments.
SAFETY SUMMARY
All safety related regulations, local codes and instructions that appear in the
manual or on equipment must be observed to ensure personal safety and to
prevent damage to either the instrument or equipment connected to it. If
equipment is used in a manner not specified by the manufacturer, the protection
provided by the equipment may be impaired.
Do not use the PCU to directly command motors, valves, or other actuators
not equipped with safeguards. To do so, can be potentially harmful to persons
or equipment in the event of a fault to the unit. An independent and redundant
limit indicator with alarm outputs is strongly recommended. The indicators
should have input sensors and AC power feeds independent from other
equipment.
SPECIFICATIONS
1. DISPLAY: Dual 4-digit
Upper Process Display: 0.4" (10.2 mm) high red LED
Lower Auxiliary Display: 0.3" (7.6 mm) high green LED
Display Messages (Model dependent):
“OLOL” - Appears when measurement exceeds +105% input range.
“ULUL” - Appears when measurement exceeds -5% input range.
“SENS” - Appears when measurement exceeds “OLOL” & “ULUL”
range.
“....”
- Appears when display values exceed + display range.
“-...”
- Appears when display values exceed - display range.
“SLid”
- Appears when loss of slidewire signal is detected.
“VALV”
- Appears when valve actuator error is detected.
2. POWER: Switch selectable 115/230 VAC (+10%, -15%) no observable line
variation effect, 48 to 62 Hz, 10 VA.
3. ANNUNCIATORS:
LED Backlight Status Indicators (Model dependent):
%PW
- Lower auxiliary display shows power output in (%).
DEV
- Lower auxiliary display shows deviation (error)
from process setpoint.
OP1
- Main control output is active.
AL1
- Alarm #1 is active.
AL2
- Alarm #2 is active (for Dual Alarm Option).
OP2
- Secondary output is active
(for Secondary Output Option).
OPN
- Valve positioner OPEN output is active
(for Valve Positioner Option).
CLS
- Valve positioner CLOSE output is active
(for Valve Positioner Option).
SEC
- Lower auxiliary display shows second analog input
(for Second Analog Input Option).
MAN
- Flashing: Controller is in Manual control mode.
REM
- ON: controller is in remote setpoint mode
(Second Analog Input Option).
- OFF: controller is in local setpoint mode
(Second Analog Input Option).
- Flashing: controller is in Manual control mode
(Second Analog Input Optional).
4. CONTROLS: Four front panel push buttons for modifying and setup of
controller functions and one external input for parameter lockout or other
functions.
5. SIGNAL INPUT:
Sample Period: 100 msec typ.
Response Time: 300 msec typ. (to within 99% of final value w/step input)
Signal Overdrive Threshold:
10 V Range: 13 V typ.
20 mA Range: 26 mA typ.
Signal Overdrive Response:
Main Control Output: Programmable preset output
Display: “SENS”
Alarms: Upscale drive
DC Linear: Programmable preset output
Normal Mode Rejection: 40 dB typ. @ 50/60 Hz (improves with increased
digital filtering).
Common Mode Rejection: 100 dB typ., DC to 60 Hz
Protection: Input overload 120 VAC for 30 seconds.
Range And Accuracy:
SIGNAL RANGE
ACCURACY (% OF
UNSCALED
READING)
MAXIMUM
INPUT
INPUT
IMPEDANCE RESOLUTION
0 to 10 VDC
±(0.15% + 3 mV)
300 VDC
1M Ω
10 mV
0 to 20 mADC
±(0.15% + 6 µA)
200 mADC
10 Ω
10 µA
6. OUTPUT MODULES [Optional] (For All Output Channels):
Relay:
Type: Form-C (Form-A with some models. See Ordering Information.)
Rating: 5 Amps @ 120/240 VAC or 28 VDC (resistive load), 1/8 HP @
120 VAC (inductive load) max.
Life Expectancy: 100,000 cycles at max. load rating. (Decreasing load
and/or increasing cycle time, increases life expectancy).
Logic/SSR Drive: Can drive multiple SSR Power Units.
Type: Non-isolated switched DC, 12 VDC typ.
Drive: 45 mA max.
Triac:
Type: Isolated, Zero Crossing Detection
Rating:
Voltage: 120/240 VAC
Max. Load Current: 1 Amp @ 35°C
0.75 Amp @ 50°C
Min. Load Current: 10 mA
Off State Leakage Current: 7 mA max. @ 60 Hz
Operating Frequency: 20 to 400 Hz
Protection: Internal Transient Snubber, Fused
7. MAIN CONTROL OUTPUT:
Control: PID or ON/OFF
Output: Time proportioning or linear DC
Hardware: Plug-in, replaceable output modules
Cycle time: Programmable
Auto-tune: When selected, sets proportional band, integral time, and
derivative time values.
Signal Overdrive Action: Programmable