Dwyer CPF User Manual
Page 6
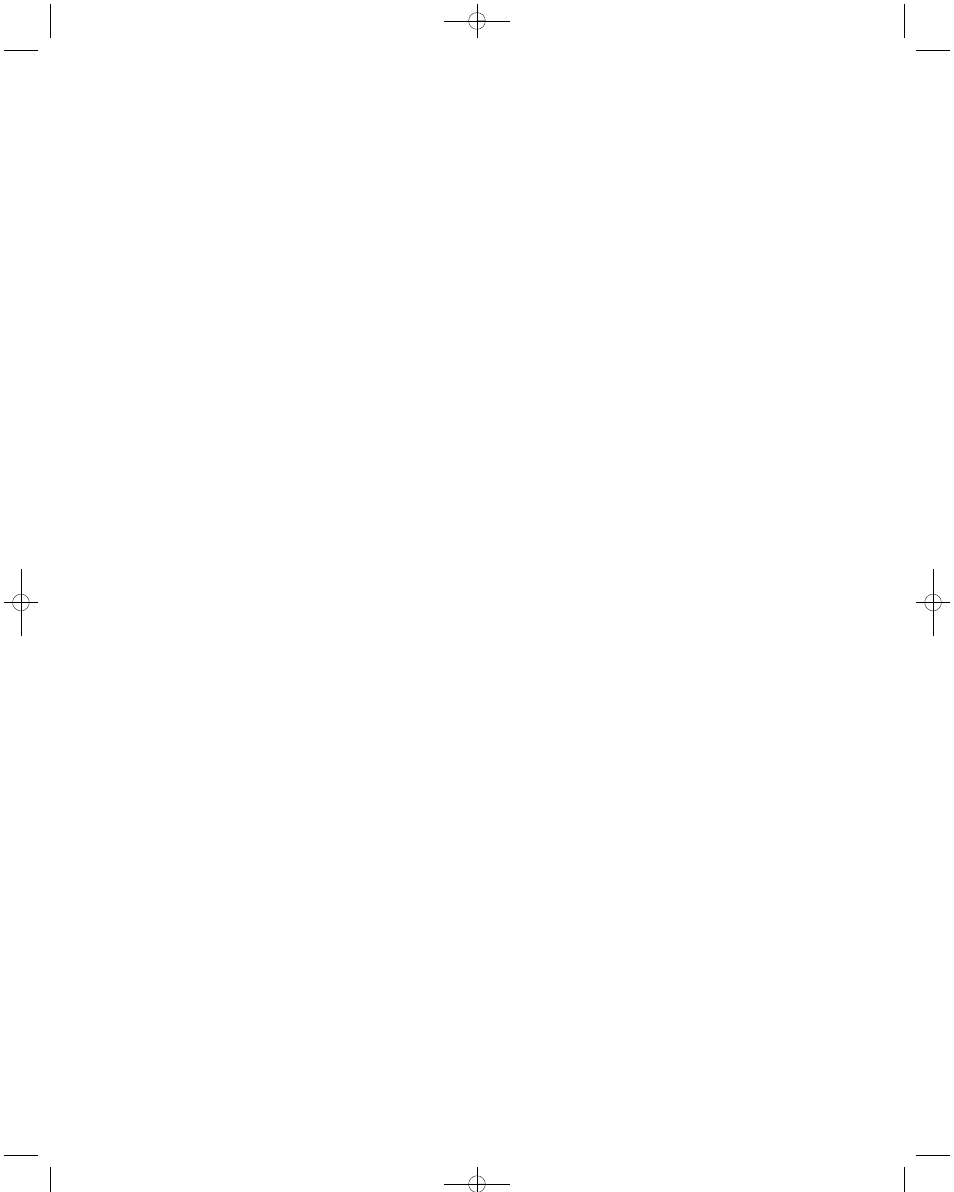
REPLACEMENT PARTS
Under proper care, there should be no need to stock
replacement parts.
Otherwise, parts only need to be replaced if damaged. Any
visible damage to the entire surface of the O-ring or sight tube
(particularly from the bottom edge) indicates need for
replacement. To insure accuracy, the inside surface of the meter
core tube, slot edges, and OD of the float piston should be free
of nicks, chips, with no visible erosion of any surfaces.
STORAGE REQUIREMENTS
There are no special requirements for Series PVF and CPF
flowmeters and parts. They should be kept in a reasonably clean
location away from excessive heat (over 120°F, 48ºC.) or
chemical or solvent fumes and vapors.
MAINTENANCE
Upon final installation of the Series PVF and CPF Flowmeters,
no routine maintenance is required. A periodic check of system
calibration is recommended. The Series PVF and CPF is not
field serviceable and should be returned if repair is needed (field
repair should not be attempted and may void warranty). Be sure
to include a brief description of the problem plus any relevant
application notes. Contact customer service to receive a return
goods authorization number before shipping.
ASSEMBLY
Replace all parts in reverse order of disassembly. Note the small
key on the core tube that must be aligned with a corresponding
keyway in the meter body. Seat the O-ring on the sight tube
before assembly (put the metal back-up ring on first for glass
sight tube models). Lubricate the O-ring with a small amount of
service compatible silicone grease or petroleum jelly to facilitate
replacement.
After replacing the internals, using hands only, press the sight
tube firmly down into the meter body with a twisting motion. Be
careful not to rock the sight tube side to side and bend the
snorkel tube/guide inward where it might interfere with float
movement. Rotate sight tube as necessary for scale visibility
and/or alignment of slots for lock ring tabs. Reinsert lock rings
and cotter pins, lower flange and snap ring (be sure snap ring
engages groove in body), or flange bolts (do not over tighten).
If reassembled correctly, the top edge of the indicator disk or
center of the ball should line up with the scale “zero” (either
dotted black or scribed line). If it does not, disassemble the
meter completely and carefully reassemble it, making sure core
tube is completely seated in the body.
If new flow internals are used, the scale may have to be
remounted on the sight tube. Depending on the model type, this
can be done either by loosening the mounting screw, or
reattaching the scale with double sided adhesive (new flow
internals are shipped with a new scale).
F-23:TEMPLATE 10/27/09 4:07 PM Page 6