Wellsaw 1016 User Manual
Page 8
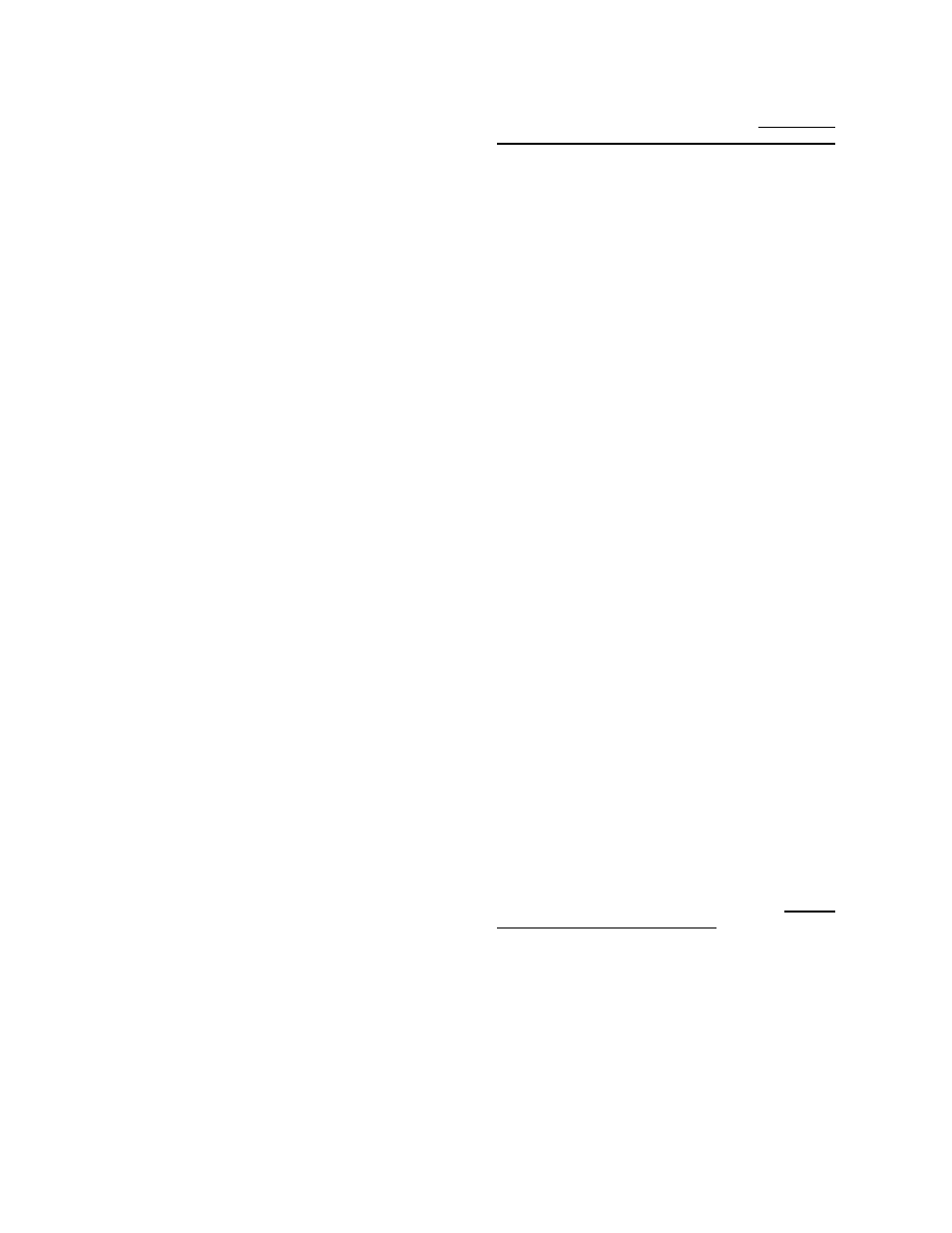
7
Dash Pot
Machines are equipped with a dash pot (frame check) for the
purpose of stabilizing downward travel of the saw frame,
thereby protecting the saw blade from damage. The action
of the dash pot is hydraulic and controlled by fluid being
passed through an orifice in the piston on the downward
stroke.
Fill withing 1" of the top of the bottom cylinder with Mobil
Velocite Oil #6 or equivalent.
Frame Weight Adjustment
Before adjusting the frame spring at motor end, remove the
hydraulic dash pot and move the sliding weight to the rear
position (motor end). The frame spring should be adjusted
for approximately 16 pounds of weight at the frame handle.
Too much frame weight will cause the blade to make
crooked cuts!
Feeding Pressure
For saws before S/N 3319 feed pressure is varied by moving
the weight on the top side of the frame. Blade pressure
increases as the weight is moved toward the open end of the
saw. For saws starting at S/N 3319 feed pressure is varied
by turning the needle valve mounted on the side of the
dashpot cylinder. Excessive pressure may cause a run-out
of the blade (see Feed & Speed chart for recommendations).
Hydraulic Feed Control
The feed rate is hydraulically controlled with a needle
valve located on the side of the cylinder. Caution: Do not
attempt to loosen or remove hoses until the saw frame is
supported in its “Down” position.
Speed Selection
Saws are equipped with step pulleys providing blade speeds
of 50, 100, 175 and 275 feet-per-minute. High speeds are
suggested for cutting thin wall tubing, channels, aluminum,
brass or any metal that will not burn the blade teeth. Use
medium speed for general cutting such as cold rolled,
machine steels, heavy channels, etc. Run at low speed for
cutting nickel steels or any metal requiring a slow speed on
a lathe. When cutting brass, use a blade that has not been
used on other metals and apply beeswax to the teeth.
Variable Speed Drive
Model 1016 may be equipped with variable speed pulleys
providing infinite speed selection between 70 and 375 feet-
per-minute. See Cutting Speed Chart for settings.
To vary blade speed, rotate handwheel clockwise to increase
speed or counter-clockwise to decrease speed. Do not adjust
the speed unless the pulley system is in operation (spinning).
The handwheel drag is set at the factory during assembly.
This drag prevents handwheel “creep” during operation but
still permits easy adjustment. Due to normal wear and
environment, the drag setting may change. To readjust,
tighten set screw in thrust nut.
Belt
Pivoted mounting provides for quick belt change. With the
belt in pulley grooves for the desired speed, swing motor to
put proper tension in the belt. Tighten thumb screw to hold
motor in proper operating position.
Fixed Vise Jaw
The two pins in the fixed vise jaw should be kept in place in
order to ensure square cuts. For cutting angles, the pins must
be removed and the turned to the desired position and
tightened with clamp bolts. These pins enable operators to
quickly relocate the fixed vise jaw for approximate 90
cutting. For final, accurate cutting, the fixed vise jaw should
be squared with the blade. (See Guide Alignment)
Sliding Vise Jaw
The sliding vise jaw is fitted with a lift plate and ratchet dog
for quick action. A hand wheel tightens the vise on the
workpiece.
Excessive pressure is not required to hold
workpiece securely.
Maximum Capacity
To obtain maximum vise capacity, remove vise jaw pins and
move fixed vise toward motor end to the last two holes in the
bed. Make sure the stock in the vise will not strike the ratchet
arm.
Placing the Blade on Saw
1. Raise saw head part way.
2. Open idle and drive wheel guards.
3. Loosen Rite Tension® by turning “T” handle Counter-
Clockwise (CCW) at least six (6) times. Gently pushing in on
the handle while turning will ensure that the device will reset
properly.
5. Open each carbide guide (if equipped). Reach behind each
blade guide assembly and turn the black knurled knob
Counter Clockwise (CCW) until it stops. This pulls the
carbide block away from the blade.
6. Remove the blade. Always wear gloves when handling
bandsaw blades.
7. Install the blade on the bandwheels making sure the teeth
are pointing in the direction of travel (toward the motor). If
not turn the blade inside out. Fit the blade into the guides and
close the carbides by turning the black knob clockwise until