Van Air Systems HL-2500 User Manual
Page 19
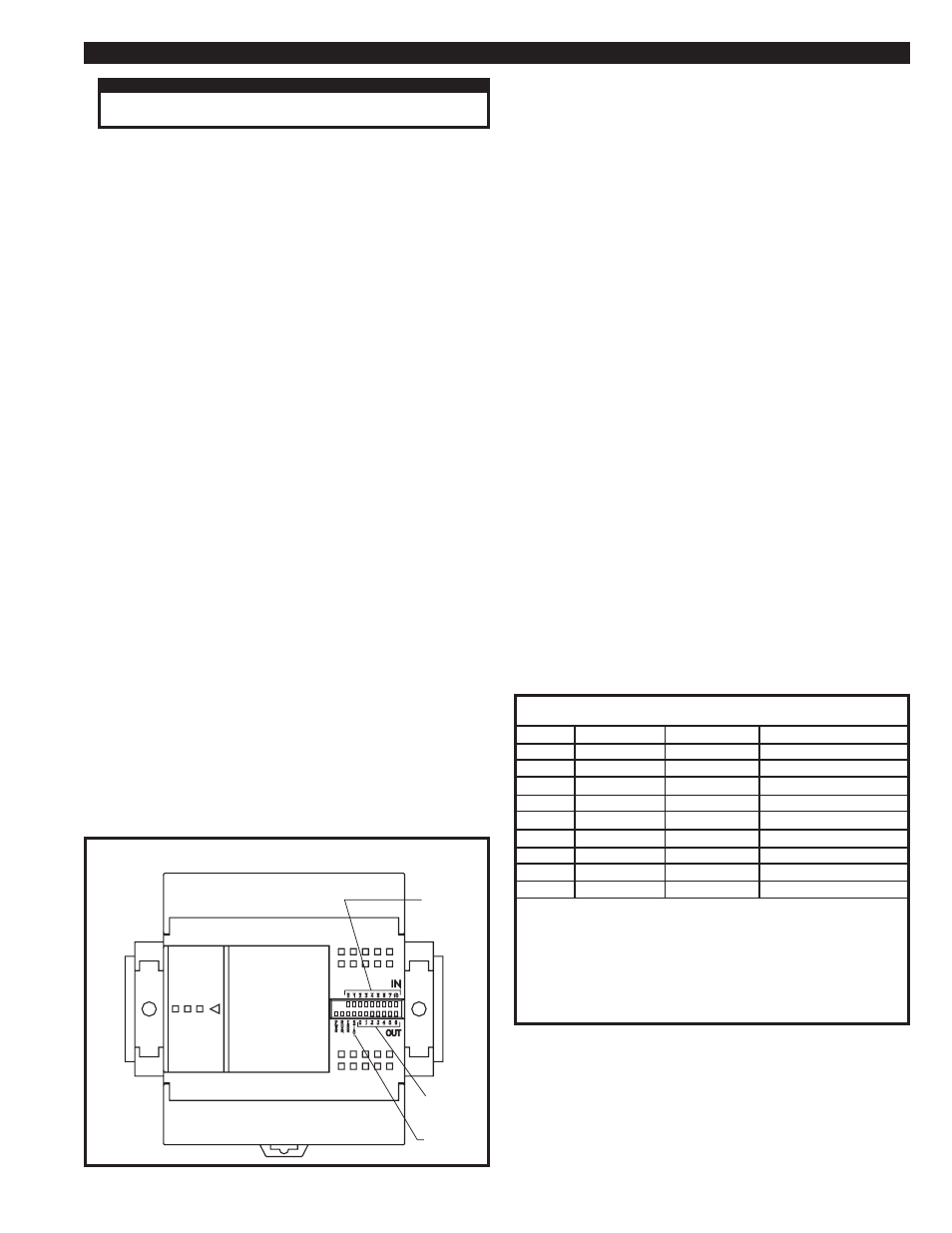
PAGE 19
OUTPUT DEVICES
0 SV1 & PL7
1 SV2 & PL8
2 SV3 & CR1
3 PL2 & CR2
4 PL3 & CR3
5 PL4
6 SPARE
MAINTENANCE & TROUBLESHOOTING
SECTION 11
FIGURE 11A PROGRAMMABLE CONTROLLER DETAIL
FIGURE 11B INPUT AND OUTPUT LIST (EMCON II)
INPUT
DEVICES
0
PB1
1
PS1
2
PS2
3
PB2
4
CDP1
5
PB3
6
SW1
7
CDP2
10
SPARE
NOTE:
The general alarm contact is a normally open dry contact which is wired to terminals #5 and
#6.
The lights are run off 120 volts AC which is reduced to 24 volts DC through resistors
and diodes on the printed circuit board.
The control relays (CR1, CR2, CR3) are mounted on the board which is mounted to the
back of the control box door. CR2 and CR3 are the control relays which give you the
general alarm contact.
11.5-2B TESTING THE INPUT DEVICE
EMCOM II MODELS ONLY:
The PLC supplies a 24 volt DC signal to the input devices and alarm
contacts. If the input device is activated, it will cause that input LED
to light. The input LEDs are labeled 0 to 7.
The input devices can be easily tested for proper operation. With
power to the control box, set the Power ON/OFF Push-button (PB1)
to the OFF position, then the ON position. This should cause LED 0
to light. Pushing the failure to switch light (PB2) should cause LED 3
to light. Pushing the high humidity light (PB3) should cause LED 5 to
light. The fixed/auto selector switch can be tested as follows. In the
fixed mode, LED 6 should be off. In the auto mode, LED 6 should be
lighted. If these input devices do not function as described, they
should be replaced.
The pressure switches monitor the failure to switch option. The
inputs from the pressure switches (PS1, PS2) can be observed while
the dryer is in operation. Any time there is more than 30 psig
pressure in the left tower, pressure switch (PS1) should cause LED 1
to light. Any time there is more than 30 psig pressure in the right
tower, pressure switch (PS2) should cause LED 2 to light. If the
pressure switches do not respond as previously explained, replace
them.
To check input 4 or 7, follow the procedures in Section 11.5-9 for
calibrating the outlet humistat.
If the input devices are activated and LED is not illuminated, take a
voltage measurement across the input terminals. If the device is
faulty, it must be replaced. If the device is working properly, check
the wiring from the PLC. If the wiring and device are good, the PLC
is faulty and should be replaced. Reference Figure 11I DRYER
WIRING DIAGRAM for wiring and terminal numbers.
Reference Sections 11.5-2B and 11.5-2C for procedures to verify
that the input and output devices are operating properly. If the
devices are operating properly, the PLC will need to be replaced.
11.5-2C TESTING THE OUTPUT DEVICES
EMCON II MODELS ONLY:
The microprocessor’s outputs are 120 volts AC. The output LEDs
are labeled 0 to 5. If the output’s LED is illuminated, that output is
supplying 120 volts AC to its component.
To check outputs 0 through 2, follow the procedures in Section
11.5-3.
INPUT
LEDs
OUTPUT
LEDs
NOT
USED
WARNING
THE POWER ON/OFF PUSH-BUTTON ON THE CONTROL BOX
DOES NOT TURN THE POWER OFF TO THE PLC.
The PLC is wired so it is energized when power is supplied to the
control box, even if the power on/off push-button is in the off
position. This is to prevent loss of retentive counter memory. The
counters are used to monitor run time and cycle life of components.
The retentive memory will hold the data safely for at least 30 days.
The information stored in memory is accessible with a HMI Kit (not
supplied).
11.5-2A (Optional) HMI KIT
EMCON II MODELS ONLY:
A Human Machine Interface is available for this dryer. The
monitor can be fastened to the PLC. It will allow the operator to
view the counters and registers in the program on the PLC.
With the purchase of this HMI kit, a list of the counters and
registers will be included. With the list and monitor, the operator
can find out the following information:
• How long the dryer has been in operation.
• How many times the valves have been activated.
• How many times the HIGH HUMIDITY ALARM has been
activated.
• How many times the FAILURE TO SWITCH ALARM has been
activated.
• How long the dryer has operated in ENERGY SAVINGS.
• How long the dryer has operated in the CALIBRATION
CYCLE.
The PLC has power, run and error LEDs. If there is power to the
PLC, the power LED will be illuminated. If the power LED is not
illuminated, check the power supply to the PLC. If there is power
present, the PLC is faulty.
If the error LED is lighted, an error has occurred in the program
logic. Consult factory.
The run LED must be on for the PLC to operate. If the run LED is
off, turn the main power to the dryer off and on again. The PLC
should reset and the run LED should turn on. If the LED does not
turn on, consult factory.
If the power and run LEDs are on and the error LED off, the PLC
may still be faulty. To verify that the input and output of the PLC
are operating properly, the input and output devices must be
checked. Figure 11B lists the inputs and outputs on the PLC and the
corresponding devices.