Em1-200, Ehtt, Ehtt-l – Vestil EM1 series User Manual
Page 2
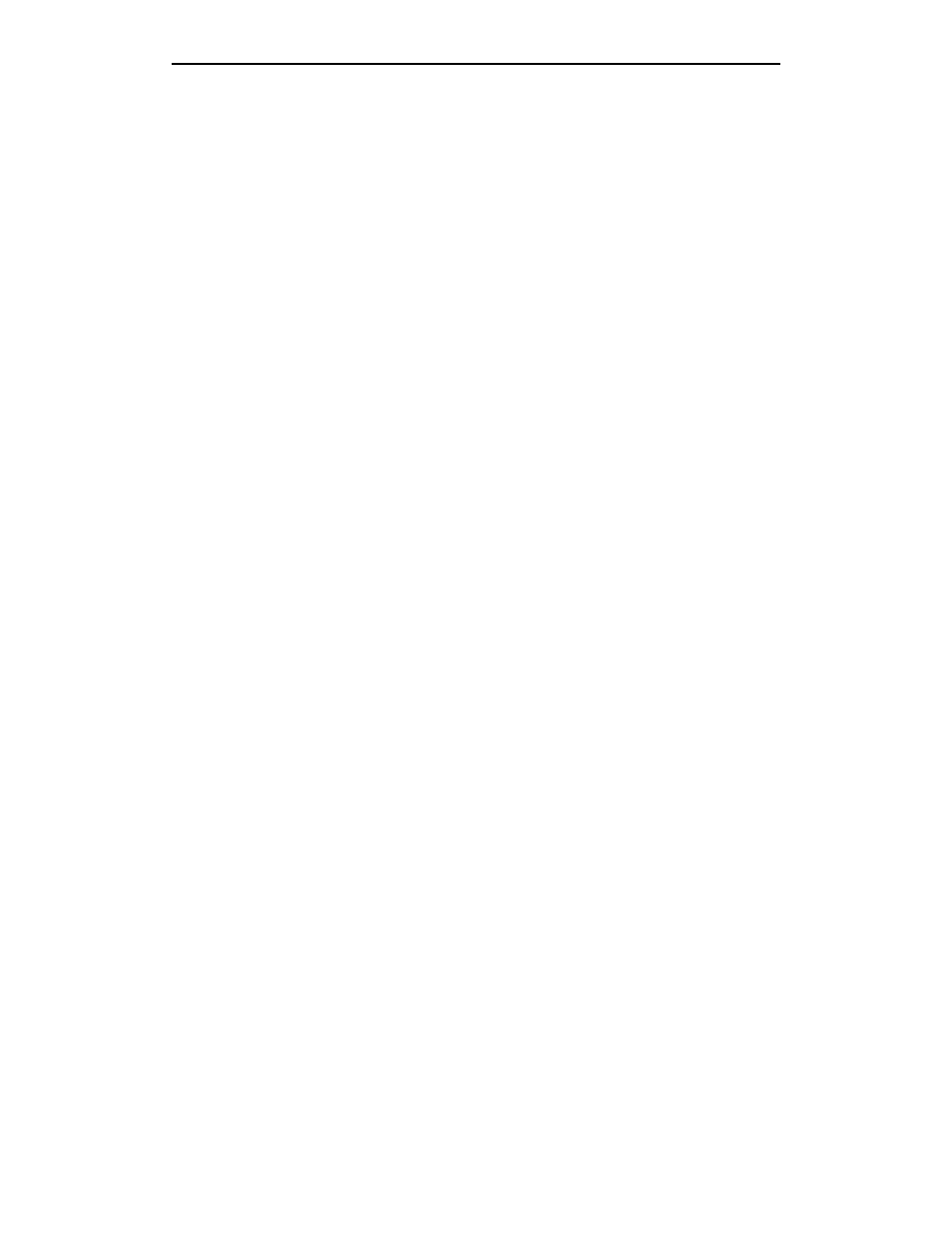
03/05
03-126-120.doc
V
ESTIL
M
FG
.
C
O
2
I
NSTALLATION
I
NSTRUCTIONS
–
EM1-200
&
-500,
EHTT,
EHTT-L
Review this entire page before installing the tilting table.
Consult the factory in the event there are any questions or problems at the time of installation, or for
information regarding optional features not covered by the owner’s manual.
The tilting table must be removed from the shipping wood and securely anchored to the floor before use! The
EM1-500 platform must be tilted to the 90° position, and supported if necessary, before removing the shipping wood.
• Modifications or additions to the tilting table without prior manufacturer’s authorization may void the unit’s
warranty. The addition of ancillary equipment to the platform may necessitate that its load capacity be reduced.
• The installation must be made so that it complies with all the regulations applicable to the machine and its
location. The end-user must verify that the supplied equipment is installed so it will be suited to the environment
in which it will be used.
• Installation must be performed by suitably trained personnel with access to the appropriate equipment. The
electrical aspects of the installation should be performed by an electrician.
---------------------------------------------------------------------------------------
For a typical installation of a standard tilting table you will need the following:
1. A fork truck or hoisting means to unload the tilting table from the freight truck and set it into place.
2. A smooth, level, and adequately strong concrete surface on which to mount and operate the tilting table.
3. Concrete anchors, a masonry drill, a masonry bit, hand tools, grout, and steel shims. Consult the building’s
architect or facility engineer to determine the best size and type of hardware with which to anchor the machine to
the floor.
• Units designed to be portable do not need to be anchored to the floor.
4. A power supply circuit and electrical disconnect matching the motor voltage and current requirements. Refer to
the machine’s dataplate, to the labels on the control enclosure, and to the electrical section in this manual for
more information. The end-user is responsible for supplying the branch circuit’s required ground fault and short-
circuit protection. (Motor overload protection is provided by a thermostat built into the motor.)
---------------------------------------
To install a standard non-portable tilting table:
1. Remove the shipping boards from underneath the tilter’s frame.
Caution: On EM1-500’s, tilt the platform down fully (the cylinder will be extended) before removing the boards.
Otherwise, the unit could be top-heavy and tip over unexpectedly.
2. Move the tilter into place with a fork truck having at least a 2,000 lb capacity.
3. Temporarily connect the power supply to the pigtail cord supplied with the tilting table, and tilt the platform to its
maximum angle so that the control enclosure is accessible.
o
If the platform must be tilted without first having the proper power supply connected, support under the backstop
side of the platform by either attaching rigging from a crane or hoist, or inserting a lift truck’s forks under the
platform. Carefully unpin one end of the cylinder(s) and allow the platform to tilt to its maximum angle. Once the
power supply is connected, press the LOWER pushbutton to allow the cylinders to retract. (Single-acting cylinders
must be manually compressed in order to retract.) Finally, reinstall the cylinder pin and its hardware.
4. Anchor the frame to the floor through each anchoring bracket located at the frame’s perimeter using appropriate
concrete anchors.
5. Make permanent connection to the power supply, using an appropriate wiring method.
6. Operate the tilting table through several full raise and lower cycles. Verify that the limit switch(es) functions
properly.
7. Check the hydraulic oil level. It should be within 1” of the reservoir’s fill hole with the cylinders retracted. If oil
is needed, use an anti-wear hydraulic oil with a viscosity grade of 150 SUS at 100°F (ISO 32 at 40°C) or a non-
synthetic automatic transmission fluid.
8. Clean up any debris or spilled oil, and verify that all of the warning and safety labels are in good condition.