KB Electronics KBRC-240D User Manual
Page 9
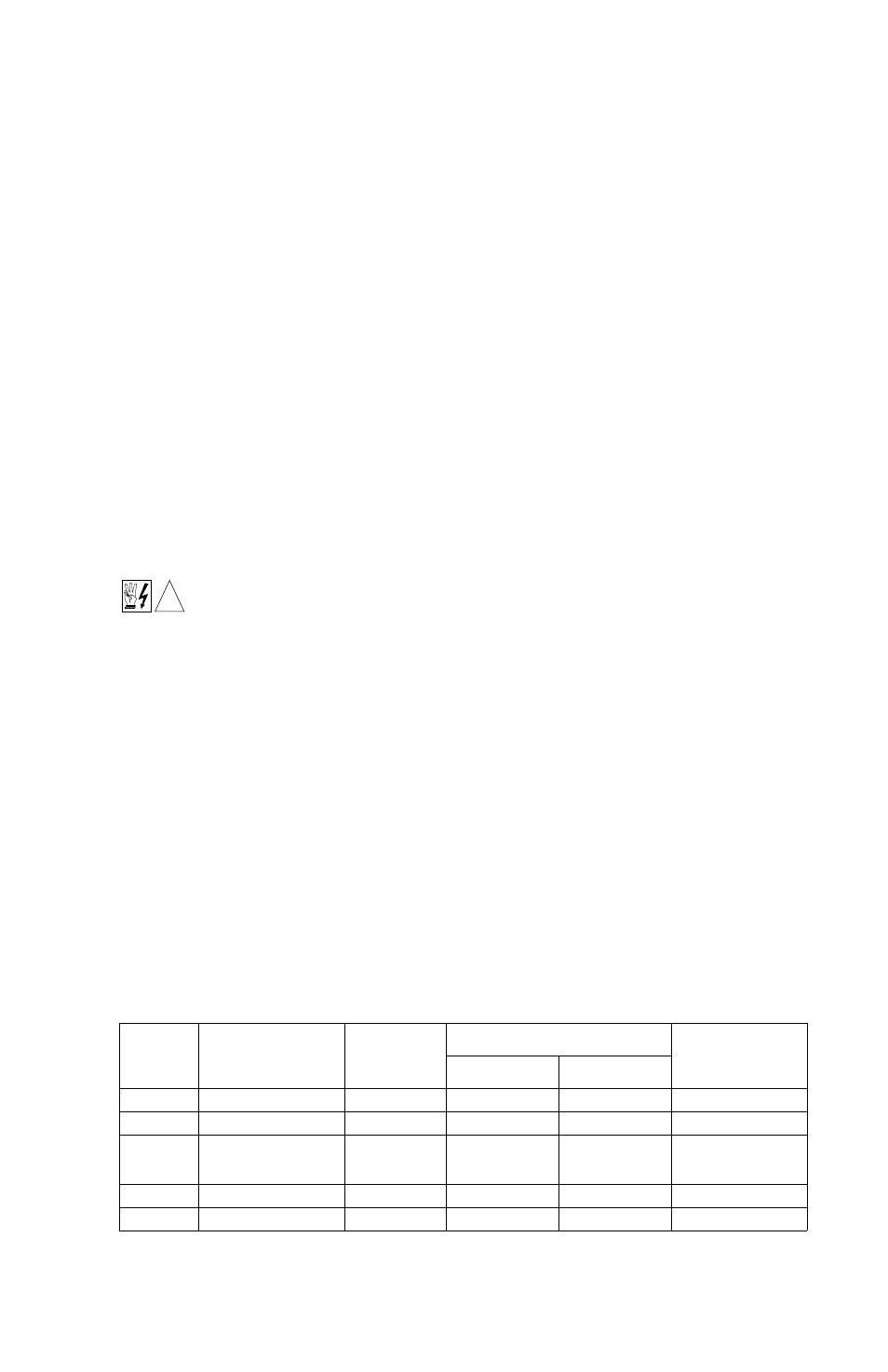
9
STANDARD FEATURES
A. Short Circuit Protection – Protects the control from a short circuit at motor connections.
B. Electronic Motor Burnout Protection (I X t) – Shuts down the control if a prolonged
overload condition exists.
C. Start/Stop Switch – Provides electronic start/stop function.
D. Diagnostic LEDs – For power on (ON), stop (STOP) and motor overload (OL).
E. Selectable Jumpers – Provide settings for AC line input voltage (J1 and J2), armature
voltage or tach-generator feedback (J3), motor current (J4), analog input voltage (J5),
control mode (J6), torque mode (J7), current limit mode (J8), stopping mode (J9), run
relay output contacts (J10) and enable (J11). See Section III, on page 14.
F. Trimpots – Provide adjustment for offset (OFFSET), forward acceleration (FACC),
reverse acceleration (RACC), maximum speed (MAX), forward current limit (FWDCL),
reverse current limit (REVCL), IR compensation (IR), response (RESP), deadband (DB)
and timed current limit (TCL). See Section VIII, on page 19.
G. Barrier Terminal Blocks – Facilitate wiring of AC line, motor armature and field, tach-
generator and run relay output.
H. Quick-Connect Terminals – Facilitate connecting the Forward-Stop-Reverse Switch,
Power On/Off Switch, Start/Stop Switch, Auto/Manual Switch and Enable Switch.
II.
WIRING INSTRUCTIONS
Warning! Read Safety Warning, on page 5, before using this control. Disconnect
the AC line before wiring.
Note: To avoid erratic operation, do not bundle AC line and motor wires with wires from
signal following, Start/Stop Switch, Enable, or any other signal wires. Use shielded cables
on all signal wiring over 12” (30cm). The shield should be earth grounded on the control
side only. Wire the control in accordance with the National Electrical Code requirements
and other codes that may apply to your area. See Figure 4, on page 10, Table 3 and Table
4, on page 11.
Be sure to properly fuse each conductor that is not at ground potential. Do not fuse neutral
or grounded conductors. See Section VII, on page 18. A separate AC line switch or con-
tactor must be wired as a disconnect so that each ungrounded conductor is opened. An
accessory Power On/Off Switch (P/N 9486) may be used in lieu of, or in addition to, the
Start/Stop Switch. The switch can be wired for single pole or double pole operation, as
required.
To maintain the watertight integrity of the control, be sure to use suitable watertight connec-
tors and wiring which are appropriate for the application. Two 7/8” (22.2mm) knockout holes
are provided for standard 1/2” knockout connectors (not supplied) for wiring. A watertight
plug is provided if only one knockout is required.
!
TABLE 3 – TERMINAL BLOCK WIRING INFORMATION
Terminal
Block
Designation
Connections
Supply Wire Gauge (AWG-Cu)
Maximum
Tightening Torque
(in-lbs)
Minimum
Maximum
TB1
AC Line Input
L1 and L2
22
12
12
TB1
Motor Armature
M1 and M2
22
12
12
TB2
Motor Field (Shunt
Wound Motors Only)
F1 and F2
24
14
3.5
TB3
Tach-Generator
T+ and T-
24
14
3.5
TB3
Run Relay
RELAY
24
14
3.5