Rma-303 direct charge - operation – Ransburg RMA Direct A12867 User Manual
Page 57
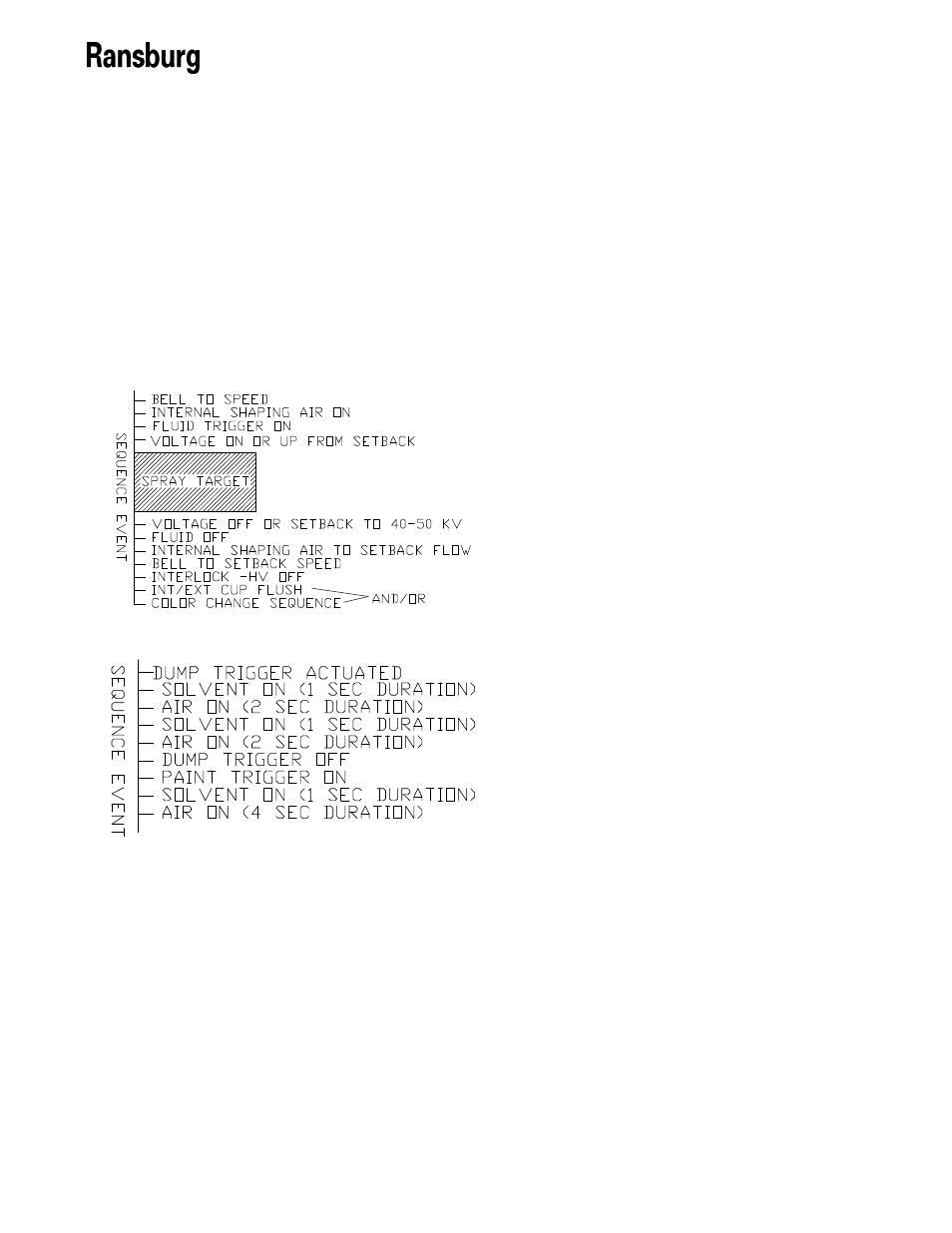
RMA-303 Direct Charge - Operation
LN-9266-11.3
54
5. Use an alternating trigger sequence of sol-
vent/air to create a chopping effect. Al-
ways ensure that the last step in the se-
quence is an air push.
6. A typical sequence is .3 seconds solvent,
1.7 seconds air push, repeat 3 times.
This sequence may be modified for other
paint and applications.
Typical Paint Sequence
Typical Color Change Sequence
Sequence Event Explanation:
1. Bell to Speed - This is accomplished by a
set point command from either the PLC,
robot, or other input device, through the I/
O module.
2. Shaping Air - Set to 350-400 SCFM while
performing a cup flush.
3. Voltage On - The voltage is turned on
from a signal to the MicroPak. The lag
time to full voltage may be reduced if a
setback voltage is used. Recommended
setback voltage is between 30 kV and 50
kV.
4. Trigger Fluid - An air signal is sent
through the PT line of the tubing bundle.
This should occur when the target is 6-12-
inches (152.4-304.8mm) from the applica-
tor centerline. (Not to be confused with
target distance.)
5. Voltage Off/Setback Voltage - Immedi-
ately precedes the trigger off. Using a set-
back voltage shortens the cascade volt-
age ramp up time.
6. Fluid Trigger Off - This should occur
when the target is typically 0-6-inches (0-
152.4mm) past the applicator centerline.
7. Shaping Air to Setback - The setback
flow of air should never be below 70 slpm
(2.6 SCFM) for the shape air.
8. Color Change Sequence - Used when
color is changed one to the other. Typical
sequence is shown in “Typical Color
Change Sequence” figure in the
“Operation” section. (Note: During this
sequence, the applicator should be
moved to a position to collect the
waste material.)
The sequence shown is
a starting point for processing, but the final
sequence will depend on the material be-
ing sprayed and the solvent used to purge
the applicator with.