Ab c d – SPP Pumps Auto Prime Q Series - Workshop Manual User Manual
Page 11
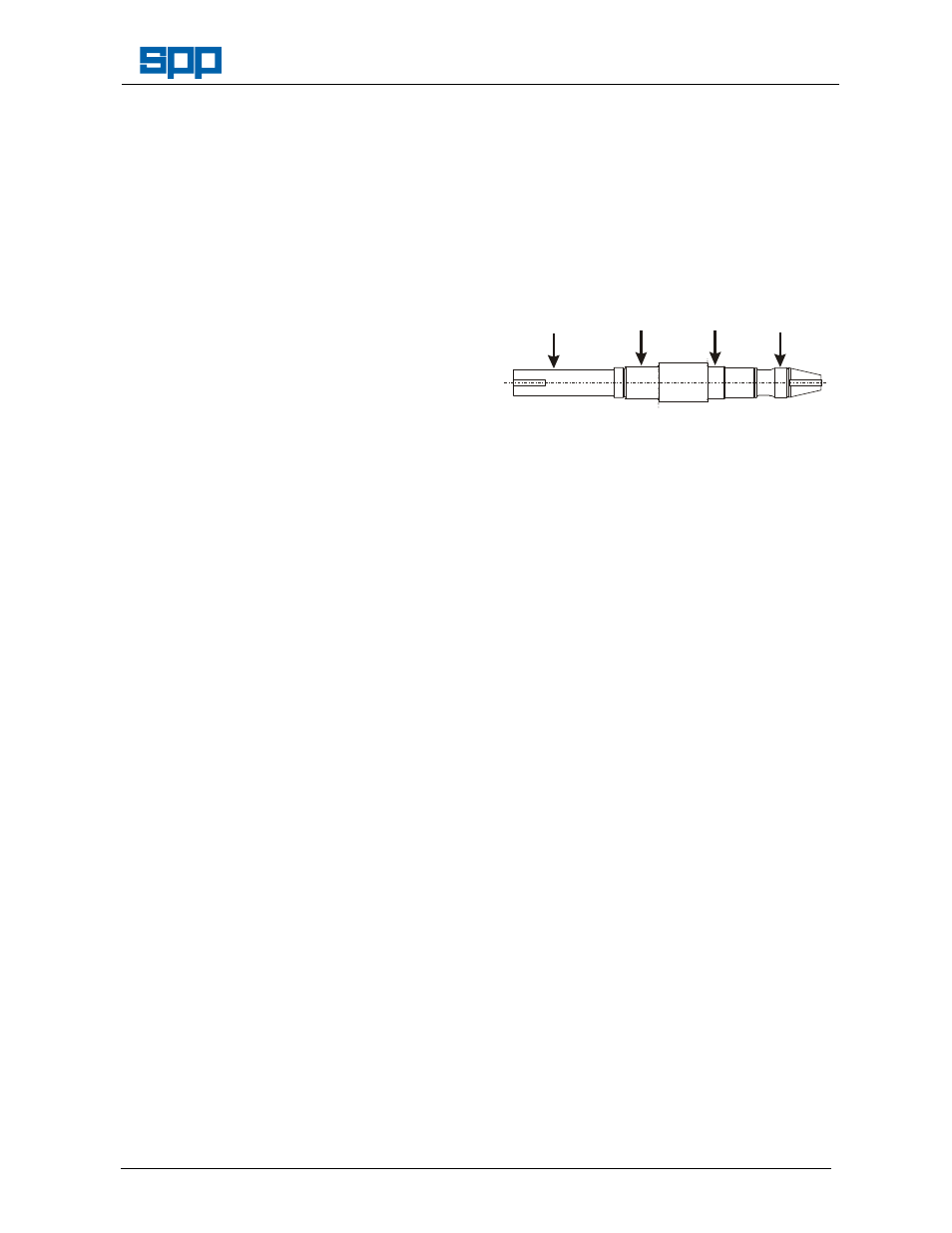
Workshop Manual for
AUTOPRIME Q Range Pump Unit
Manual No/Rev
W72-021E / 8
Our policy is one of continuous improvement and we reserve the right to alter specifications at any time
Page 11 of 36
the mechanical seal from the shaft.
Note: Mechanical seals are usually replaced
during pump maintenance, if the seals are
not being replaced, great care must be
taken not to touch or damage the sealing
faces, and parts from each seal should kept
for reassembly together.
7.
With a pair of circlip pliers, extract the
mechanical seal retaining circlip from the
shaft. Carefully withdraw the rotating part of
the mechanical seal from the shaft.
8.
Remove the 6 nuts (25) from the bearing
side of the pump casing and carefully
withdraw the back wear plate from the
pump casing. Take care not to damage the
stationery element of the mechanical seal if
this to be reused.
9.
With a pair of circlip pliers, extract second
the mechanical seal retaining circlip from
the shaft. Carefully withdraw the rotating
part of the mechanical seal from the shaft.
10.
Remove the 8 nuts from the bearing
housing studs and detach the pump casing
from the bearing housing.
11.
Remove the drive belts from the drive shaft
pulley, release the setscrews that lock the
drive pulley to the shaft and withdraw the
pulley.
12.
Remove the four screws and withdraw the
bearing cap from the bearing housing.
13.
Using a suitable C spanner undo and
remove the bearing retaining nut
14.
Mount the bearing housing in a press and
push the shaft, complete with drive end
bearings out from the bearing housing.
15.
If it is required to replace the bearings the
drive end bearings may be pushed of the
shaft, note that is important to replace them
as a pair.
16.
The non-drive end roller bearing may be
pushed out from the bearing housing using
screws in the threaded holes provided.
17.
The stationery part of the outer mechanical
seal may be pushed out from it’s seating in
the bearing housing, if it is to be replaced.
6.9 Inspection of Pump Parts
1.
Wash all old lubricant from ball bearings,
housings, caps and fittings with kerosene or
white spirit, and dry bearings thoroughly by
spinning by hand, or gently with clean dry
compressed air. Renew them if they do not
then rotate smoothly with no sign of
jamming, and freely but without slackness,
or if running surfaces of balls or races show
any deterioration. Coat bearings with rust
preventive oil and wrap in greaseproof
paper.
2.
Mount shaft between point centres or on
rollers, and place stem of dial indicator in
contact with shaft. Set the indicator dial at
zero and turn the shaft slowly by hand.
Reading at any point A, B, C, and D must
not vary more than 0.05mm (0.002").
A
B
C
D
3.
Scour any rust or scale from internal iron
non-fitting surfaces.
4.
Clean all threads followed by wire brushing,
and wrap shaft threads with protective
adhesive tape.
5.
If the unit is not to be reassembled
immediately, brush all bright iron and steel
surfaces with Shell Ensis rust preventive
fluid.
6.
Protect all parts (especially mechanical seal
parts and faces) against loss, weather or
mechanical damage.
7.
Re-examine all old parts intended for re-
fitting. Worn, damaged or corroded parts
should either be re-conditioned or, if
beyond this, be discarded and replaced by
new.
8.
Ensure that all parts to be refitted
(especially new parts) are free from burrs,
with screw threads and abutting faces clean
and free from damage.
9.
Examine 'O' rings and all mechanical seal
parts and renew if showing wear or
deterioration.
10.
Apply a few strokes of a grease gun to each
grease nipple and check that clean grease
comes through to the inside of the bearing
housing.
6.10 Coalescer Disassembly
(Refer to Parts Diagram 7.4.3)
Note The coalescer contains 5 litres of oil; this
must be drained for safe disposal before
disassembly.
SPP recommends that all filter elements and
mesh is replaced when the coalescer is
disassembled for maintenance.