Preventative maintenance – A.O. Smith VB/VW-500 User Manual
Page 38
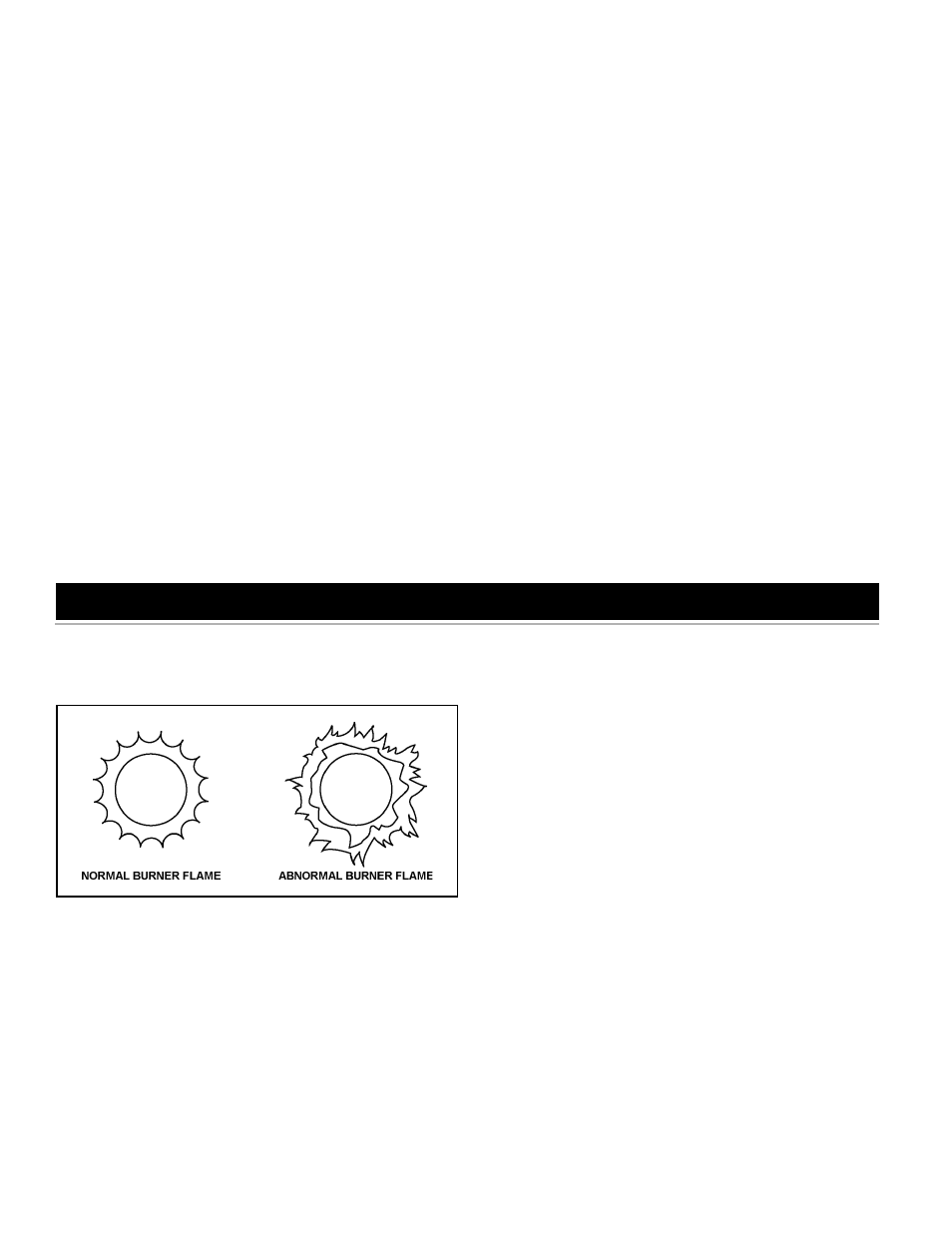
38
TROUBLESHOOTING GAS VALVE
Problem: Non-linear CO
2
curve on adjusted boiler (deviation
more than 3-6%)
1. Possible blockage at the air inlet that prevents uniform,
constant air flow.
2. The gas inlet pressure is too low at full load.
Problem: Unstable CO
2
level at minimum load
The minimum load (low fire) is too low. The pressure difference
on the pressure regulator at minimum load must be at least
0.2 in wc (50 Pa). If the pressure difference does not meet
this requirement, it may be necessary to adjust low fire
setting, see Setting Test Mode.
The pressure difference on the regulator can be measured between the
venturi and the feedback tube. It is necessary to unscrew the pressure tap
on the venturi for this measurement, and to close it afterwards.
With 17% of the reference load and a CO
2
level of 8.7%, it should
be possible to reach this minimum pressure difference. If the CO
2
level is higher, the minimum power also has to be proportionally
higher than 17%.
Problem: No gas, no burner start up
Check whether both coils of the two shutoff valves are energized
and whether both shutoff valves are opening (you should hear a
double “click” in the valve). Also check the gas inlet pressure.
Problem: Gas OK, no burner start up (both shutoff valves are
open, fan turns)
There is not enough gas to accommodate a start up. Turn throttle
screw ½ turn counterclockwise and try to start again with more
gas.
Problem: Boiler makes noise at high CO
2
level
Premix-boilers may have a loud whistle noise problem at
high CO
2
levels. This can sometimes be alleviated by
decreasing the CO
2
level.
Problem: Strong oscillations at burner start
It is normal for a small oscillation to occur in the first second of
the burner start. If the oscillation is very strong or lasts very
long, decrease the resistance of the chimney by using a shorter
tube with a larger diameter. An additional solution is to change
the start up power of the burner.
Problem: Nominal power of the mixing unit is unattainable
Possible causes for this issue are:
1. the boiler and burner head pressure drop is too large;
2. fan not turning at correct speed.
3. sensing tube is clogged or broken.
Problem: After some time, the pressure regulation of the
valve fails
Dirt in the valve finer than 0.013” (0.34mm) can prevent the correct
function of the servo pressure regulator. Replace the valve and
add a gas filter in front of the new valve.
PREVENTATIVE MAINTENANCE
This is a pre-mix burner system. The flame is not supposed to be
directly on the burner. The flame should be just above the burner
deck approximately 1/8” and blue in color, see Figure 20.
FIGURE 20. BURNER FLAMES
Visually check flame characteristics through the view port
located on the top head of the boiler. Figure 20 shows the
normal flame condition.
These boilers are designed to give many years of efficient
and satisfactory service when properly operated and
maintained. To assure continued good performance, the
following recommendations are made.
The area around the unit should be kept clean and free from
lint and debris. Sweeping the floor around the boiler should be
done carefully. This will reduce the dust and dirt which may
enter the burner and heat exchanger, causing improper
combustion and sooting.
MAIN BURNER
Check main burner every three months for proper flame
characteristics. The main burner should display the following
characteristics:
•
Provide complete combustion of gas.
•
Cause rapid ignition and carry over of flame across entire burner.
•
Give reasonably quiet operation during initial ignition, operation
and extinction.
•
Cause no excessive lifting of flame from burner ports, see
Figure 20.
If the preceding burner characteristics are not evident, check for
accumulation of lint or other foreign material that restricts or blocks
the air openings to the burner or boiler. To check burners:
1. Shut off all gas and electricity to unit. Allow unit to cool.
2. Remove main burners from unit.
3. Check that burner ports are free of foreign matter.
4. Clean burner with vacuum cleaner. DO NOT distort burner ports.
5. Reinstall burners in unit. Ensure that all the screws on the
burner flange are tightened securely so that the gasket will
provide a good seal.
6. Also check for good flow of combustion and ventilating air
to the unit.
After placing the boiler in operation, check the ignition system safety
shut-off devices for proper operation. To accomplish this with the
main burner operating, close the valve on the manifold. Within
four seconds the main burners should extinguish. If this does not
occur immediately, discontinue gas supply by closing main manual
shut-off and call a qualified serviceman to correct the situation. If
the burners extinguish, then light boiler in accordance with lighting
and operating instructions.