Magnum Venus Plastech Hypaject MK III User Manual
Page 12
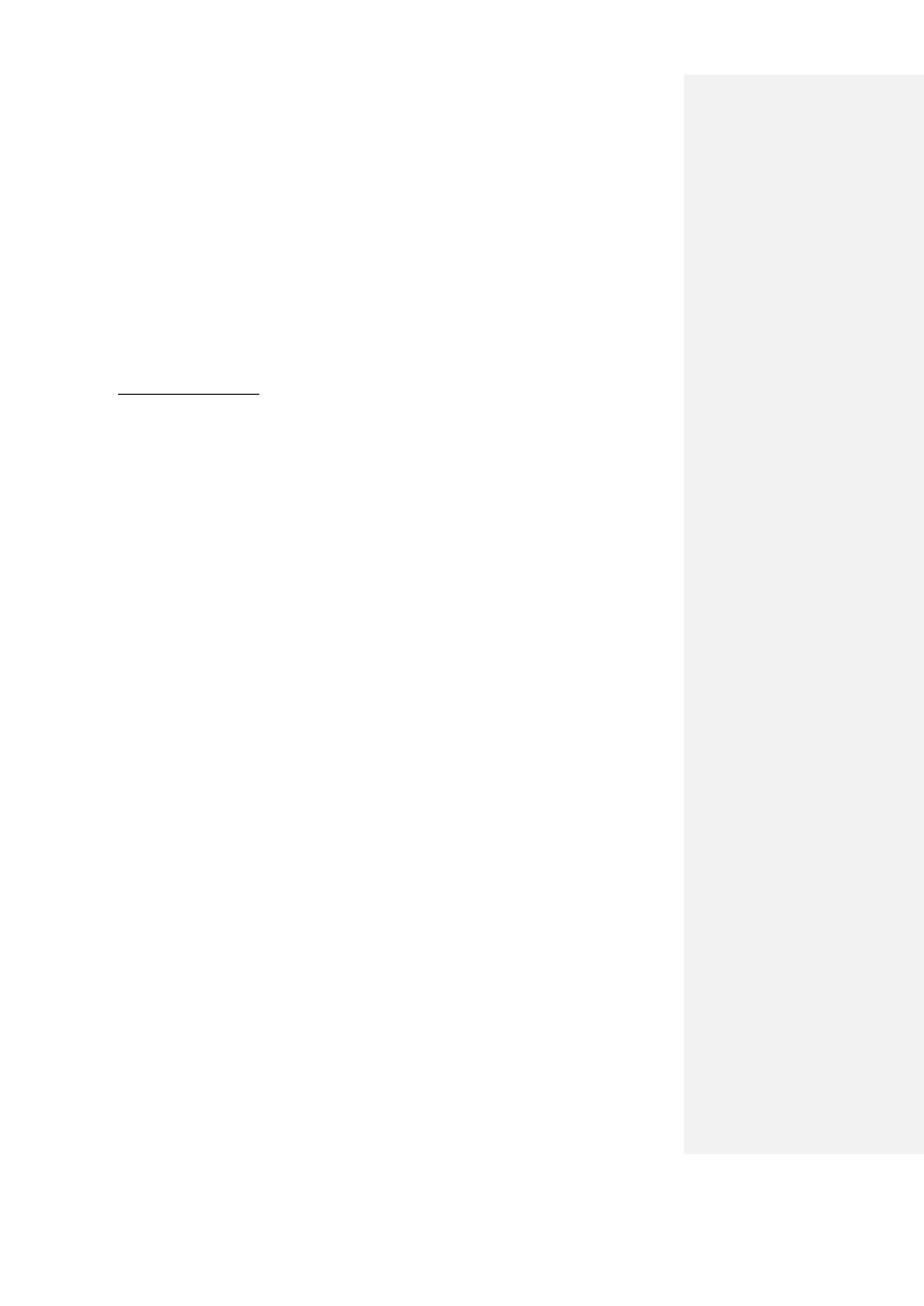
Hypaject MK III Instructions
Issue 07: April 2001-04-23
12
4.2
Procedure for set-up and use of High Temp Glass Faced Tool
1. Select the mould cavity thickness required and place the correct shims on the mould
clamps. With no shims in place the mould has a cavity of 1mm.
2. Seals
.The mould is fitted with a double ‘Dynamic Seal’. This seal is inflated with
compressed air and will allow sealing at the varying cavity thicknesses. The seal is
controlled via the control box mounted onto the back of the mould. The control box
includes a pressure on/off switch and pressure gauge. Do not attempt to inflate the seal
above 4 Bar.
The Pressure switch must be turned to the off position before the M24 Mould
clamp bolts are loosened.
The seal must not be inflated with the mould open or unclamped.
Dynamic Seal Safety.
The air supply to the control box is routed through a roller switch mounted onto one of
the mould clamps. This switch is actuated by the M24 bolt when the mould is closed and
is a safety mechanism only.
It should not be used as the method of controlling/inflating the seal.
When changing the cavity thickness the spring loaded roller switch actuator should
checked to ensure that it strikes the roller at the correct point e.g. when the mould is in
the closed position.
Always check that the seals are inflated prior to injection.
3. Make sure the reinforcement being used can be compressed to the mould cavity
thickness selected.
4. Carefully load reinforcement material into cavity, ensuring the fibre does not pass over
the inner seal.
5. Close the mould and tighten the M24 clamps.
6. Switch both dynamic seals to pressure and inflate the inner and outer Dynamic seals.
7. If using vacuum to assist injection this can now be tested to ensure the cavity is vacuum
tight.
Two corner vent points are provided.
If operating the mould at temperatures above 60
C, 6mm PTFE pipe must be used for
venting the mould cavity. 6mm nylon pipe can be used if working at lower temperatures.
The pipe is retained
by the brass fitting and ‘olive’ situated at each vent point. The vent
pipes must be routed to the vacuum supply via a suitable vacuum ‘catch-pot’ to prevent
excess resin from entering the vacuum pump.
Small amounts of fibre (surface tissue) positioned across the first resin seal at the final
point of fill will also act as a vent and allow injection without the use of the disposable
vent pipes. If this technique is to be used, the operator must observe carefully and
ensure that the mould is not ‘over injected’. If using this technique vacuum can be
applied via the fitting situated between the two Dynamic seals, and the two cavity vents
can be blocked. This technique avoids the requirement for disposable vent pipes and a
resin ‘catch-pot’.
8. Before starting the injection, make sure the mould and machine are at the correct
temperature. Injecting before the correct temperature can cause the mould cavity to
expand and result in cavitation.