8 various kinds of tach simulators, 9 commutation using resolver, Vs a two/three phase input current mode amplifier – CONTREX CXB2040 User Manual
Page 20: 11 protection circuits
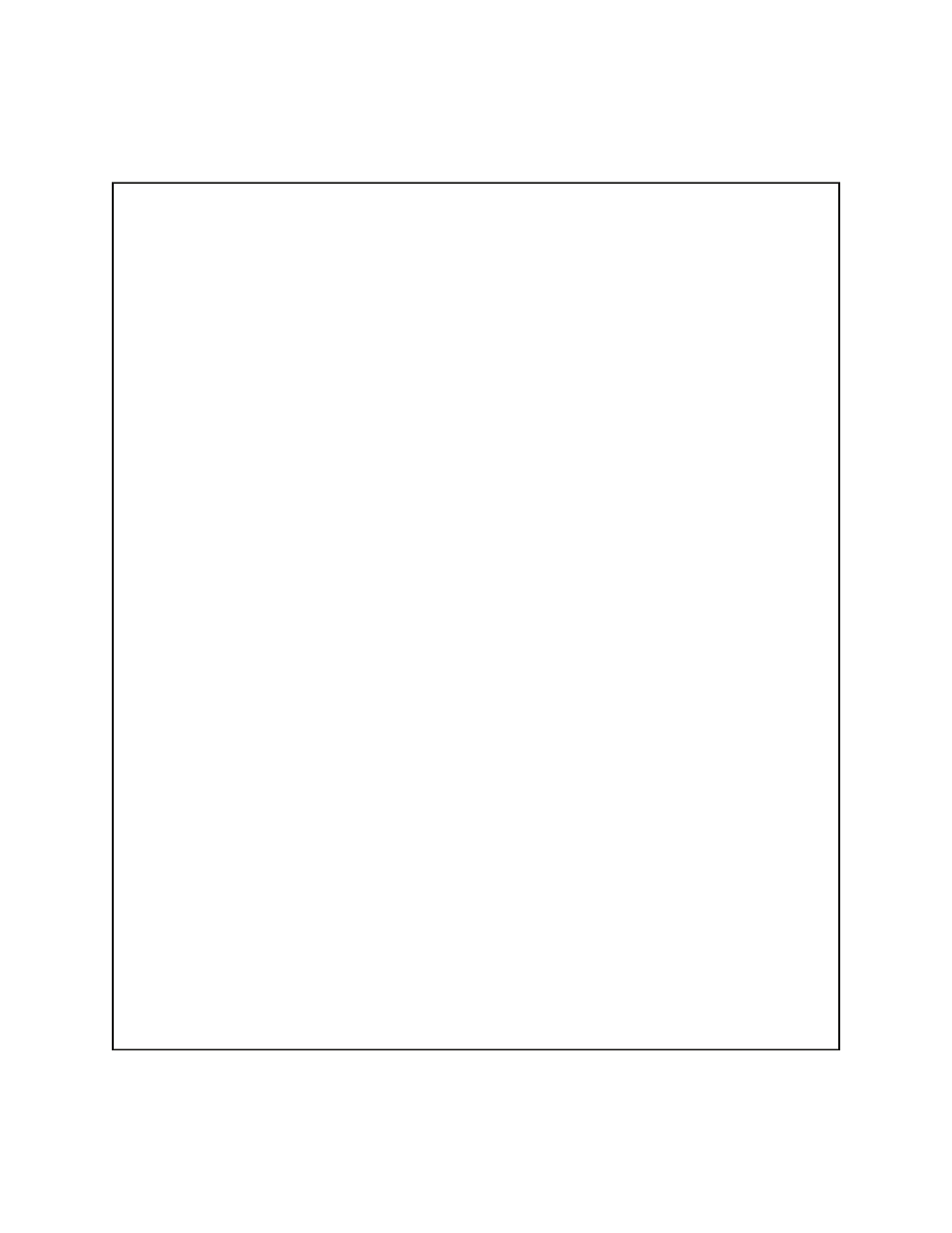
8900 Zachary Lane N., Maple Grove, MN 55369 U.S.A.
17
CHAPTER 2: THEORY OF OPERATION
2.10 CURRENT MODE IN SINE/RESOLVER OR TRAPEZOIDAL AMPLIFIER
vs. TWO OR THREE PHASE INPUT CURRENT MODE AMPLIFIER:
The fundamental difference between the current mode in sine/resolver or trapezoidal amplifiers and
the two or three phase input current mode amplifiers is that in the former case, the commutation of the
command and feedback signals is done within the amplifier itself. The latter case accepts two or three
120
o
out of phase commutated drive signals. In other words, the user’s controller has to do the
commutation of the command and feedback signals themselves. The user can either input two or three
commutated drive signals. If the user has chosen two phase input, the third phase is generated as the
negative sum of the other two inputs.
2.8 TACHOMETER (VELOCITY MODE) FEEDBACK OPTIONS:
The following is a list of ways one can choose to implement tachometer feedback in order to drive
the motor through a velocity controlled servo loop:
Brush-type and brushless DC mechanical tachometer.
Simulated tachometer using the motor commutation signals (PSEUDO-TACH).
Sinusoidal resolver.
Simulated tachometer using the encoder signals.
The simplest way to simulate the actual velocity of the motor is by installing a mechanical brush-type
or brushless DC tachometer on the motor shaft which converts the velocity of the motor into DC voltage.
The second method is to synthesize a digital tachometer using the motor commutation signals (refer
to section 2.6).
In the third method, with a sine/resolver amplifier an analogue tachometer signal is generated as part
of the Resolver-to-Digital conversion process and is immediately available for use thru the dip-switch
options for velocity mode(S1-7).
The fourth method is to have an optical encoder installed on the motor shaft to determine the
direction and position of the motor as it runs. The incoming encoder signals are converted into quadrature
clock pulses. The frequency of this clock pulses changes with the velocity of the motor and the up/down
clock output signals change with the direction of which the motor is running at. The frequency of the
clock is then converted into the tach DC voltage signal using the Frequency-to-Voltage converter.
2.11 PROTECTION CIRCUITS:
The High- and Low-Speed Electronic Circuit Breakers(HS/ECB and LS/ECB) protect the amplifier
and motor from being damaged by high motor current(specified max. peak and rms current values). The
Over Temperature and Over Voltage detection circuits will shut off the amplifier when the temperature of
the amplifier or the buss(B+) voltage exceeds a specified limit. Also, there are circuits which limit the
motor from running in either or both directions.
2.9 COMMUTATION USING RESOLVER:
The Resolver-to-Digital converter generates the necessary excitation for the resolver, and converts the
resolver’s sine and cosine signals into position data. This position information is used to amplitude
modulate the velocity error signal into three-phase, sinusoidal and current-error signals like the one in
section 2.3.