13 applying force to transducers, 14 calibration accuracy considerations – Cleveland Motion Controls ULTRA ISC CARTRIDGE TRANSDUCER REV AA User Manual
Page 34
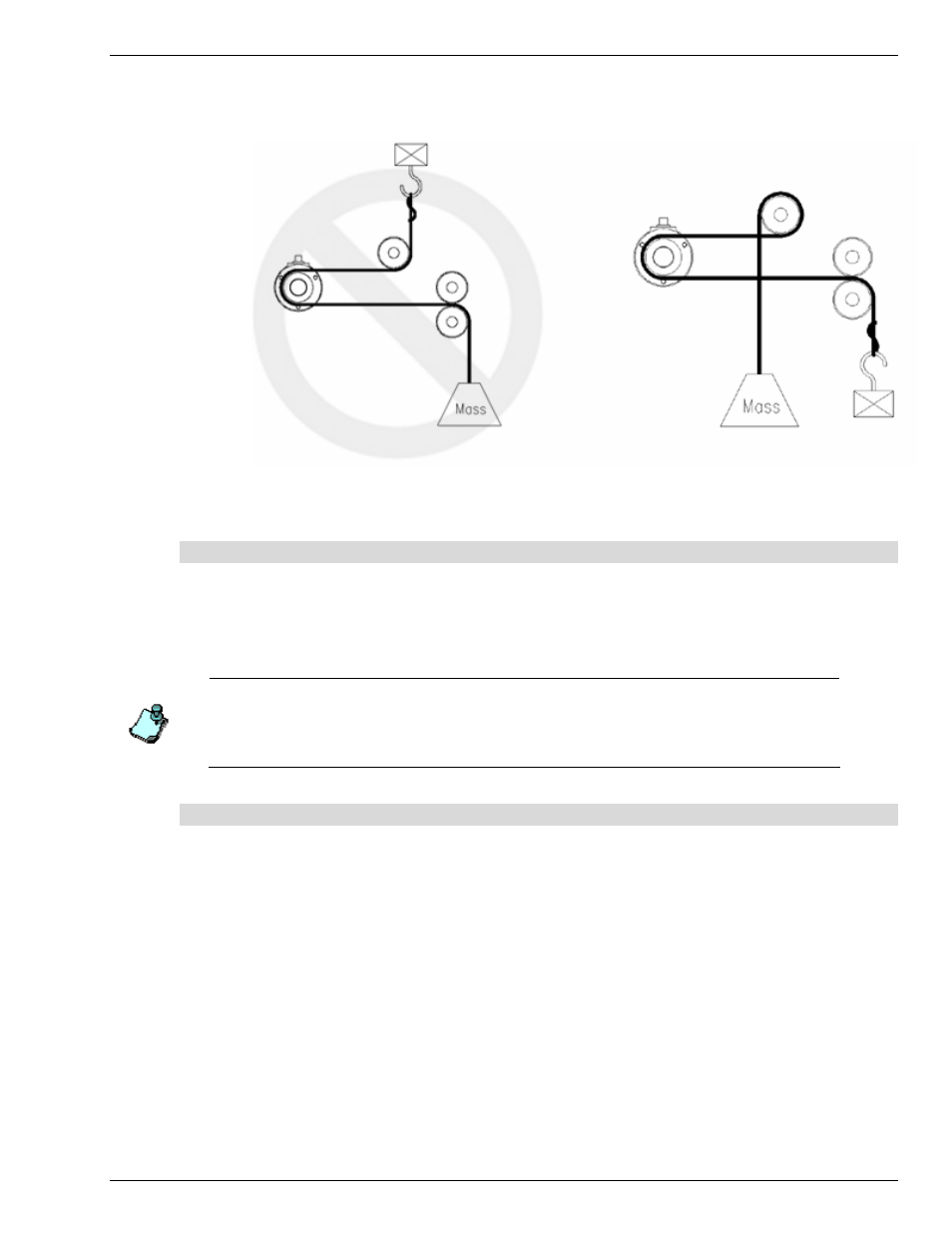
U
LTRA
S
ERIES
S
TATIONARY
S
HAFT
T
RANSDUCER
T
ECHNICAL
M
ANUAL
MAN-70430-0
R
EV
AA
26
4.13 Applying Force to Transducers
The application of an accurate calibration force can be a challenge. Keep the following points in mind:
Allow the transducer and amplifier to reach thermal equilibrium before conducting calibration.
Ideally, the temperature should reflect the expected operating conditions.
With very low force transducers, consider that connecting a test mass will involve some finite cord
mass.
When conducting a calibration that involves a large mass, it is often practical to use a series of smaller masses
added in succession. Consider performing an initial Zero and Gain adjustment when the first 20% of the
weights have been applied. By performing the calibration using this method, the Zero and Gain adjustments
can be made approximately correct earlier in the calibration effort (before many weights have been handled).
When the full calibration load is applied, there is a better chance that only minor adjustments will be needed.
4.14 Calibration Accuracy Considerations
The application of an accurate calibration force requires careful attention to minimizing the non-ideal
effects of the real world. Keep the following points in mind:
Allow the transducer and amplifier to reach thermal equilibrium before conducting calibration.
Ideally, the temperature should reflect the expected operating conditions.
The test force should be a moderate percentage of the intended working force of the transducer
and never over the 100% Maximum Working Force (MWF) or, you risk calibrating with an
overloaded (“clipped”) transducer signal.
Cycle the load on the transducer a number of times with the test force to pre-condition or “set” the
transducer prior to calibration. Repeat this procedure again before calibrating if the transducer has
been disturbed (i.e. roll remounted or any mounting bolts re-torqued).
Always apply and remove the test load in a continuously increasing or decreasing manner, so that
the force changes are monotonic. This helps to avoid disturbing any hysteresis component of the
transducers force signal.
With very low force transducers consider that connecting a test mass involves some finite cord
mass.
Examples of Force Loss due to Friction at Driven Roll
In this example, only a fraction of the test force is
transferred to the transducer due to drag from the
driven roll.
In this example, by rearranging the anchor point
and the force location as well as utilizing the idle
roll, the frictional losses are minimized.