Warning – Cashco 987 User Manual
Page 4
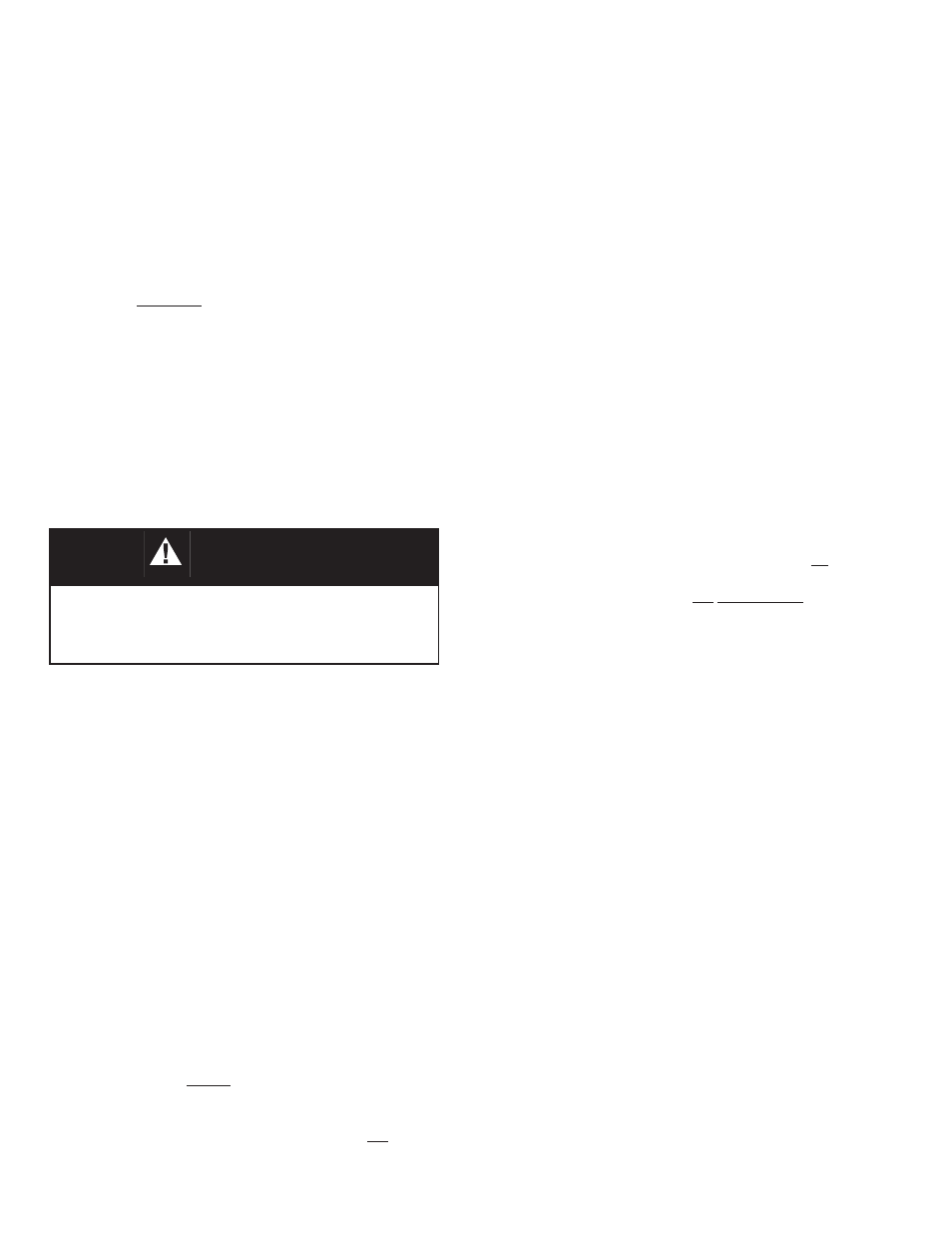
4
IOM-987
V. MAINTENANCE
WARNING
SYSTEM UNDER PRESSURE. Prior to performing any
maintenance, isolate the valve/actuator from the sys tem
and relieve all pressure. Failure to do so could result in
personal injury.
A. General:
1. Maintenance procedures hereinafter are
based upon removal of the valve/actuator
unit from the pipeline where installed.
2. Owner should refer to Owner’s procedures for
re mov al, handling and cleaning of non re us able
parts, i.e. gaskets, suitable sol vents, etc.
3. General service valves supplied from the fac-
tory do not require use of any gasket sealant.
(See below for “oxygen cleaned” valves.)
4. Valves originally supplied in accordance
with Option-55 require special cleaning pro-
ce dures. Refer to Cashco Specifi cation No.
S-1134 for details. When in compliance with
Spec. #S-1134, the valve is suitable for ox y-
gen service. Sealants and lubricants used in
reassembly of a valve unit for use in oxygen
service MUST be suitable for O
2
service.
5. All indicated Item Numbers that are with
re spect to the actuator assembly (AA) are in
parenthesis and underscored; i.e. (20). All
Item Numbers that are with respect to the body
assembly (BA) are not un der scored; i.e. (32).
Reference with respect to the positioner is in
double parentheses; i.e. ((AP)).
6. Special care must be exhibited when ro tat-
ing the plug stem (4) in the body to not mar
that portion of the surface of the stem (4)
where it contacts with the packing (10). To
rotate the stem (4) use the jam nuts or grasp
stem with soft-jawed pliers. NOTE: When using
the jam nuts (17) to rotate the stem (4), use
the upper jam nut to rotate the stem CW, and
the lower jam nut to rotate the stem CCW,
when viewed from above the valve stem.
7. Hereafter, whenever text has the following
notation, "(Note PA.)", the following text is
to be applied:
"For ATO-FC units ONLY, connect a
temporary air source to the actuator and
pressurize to a level suffi cient to initiate
travel to approximately mid-stroke."
8. Hereafter, whenever text has the following
notation, "(Note RP.)", the following text is
to be applied:
"For ATO-FC units ONLY, release all tem-
porary air pressure."
SECTION V
11. Attempt to develop manual control of the loop
by opening/closing the manual bypass as re-
quired, or by manually controlling main stream
fl ow as required.
12. When the control valve is partially open, crack
open slowly the closed block valve while si mul-
ta neous ly closing the bypass valve. Con tin ue
this procedure until the bypass is closed and
the block valves are both fully open. The
system is still under “manual” mode control,
but all fl ow is passing thru the control valve.
13. Vary controller “manual” SIG output until
match ing the “automatic” SIG output, then
change the mode of the controller over to
“automatic”, and the loop will experience a
minimum of upset conditions, and will be in
automatic control.
8. Confi rm the action of controller and positioner
– direct or reverse – are producing the de sired
response in the control unit. Con fi rm that the
control valve “fail” position is as re quired.
9. Hereafter, the procedure assumes that actual
fl uid fl ow may be established. This may not
be practical/possible in all cases; if so, vary
pro ce dure as required.
Always “heat” or “cool” down the system pip ing
SLOWLY by opening the control valve station
bypass valve in small increments.
10. With one of the control valve station block
valves still closed, and the loop controller still
in “manual” mode, open bypass valve and vary
fl ow rate manually to observe the re sponse of
the controller and control valve unit together.