Cashco 987 User Manual
Page 11
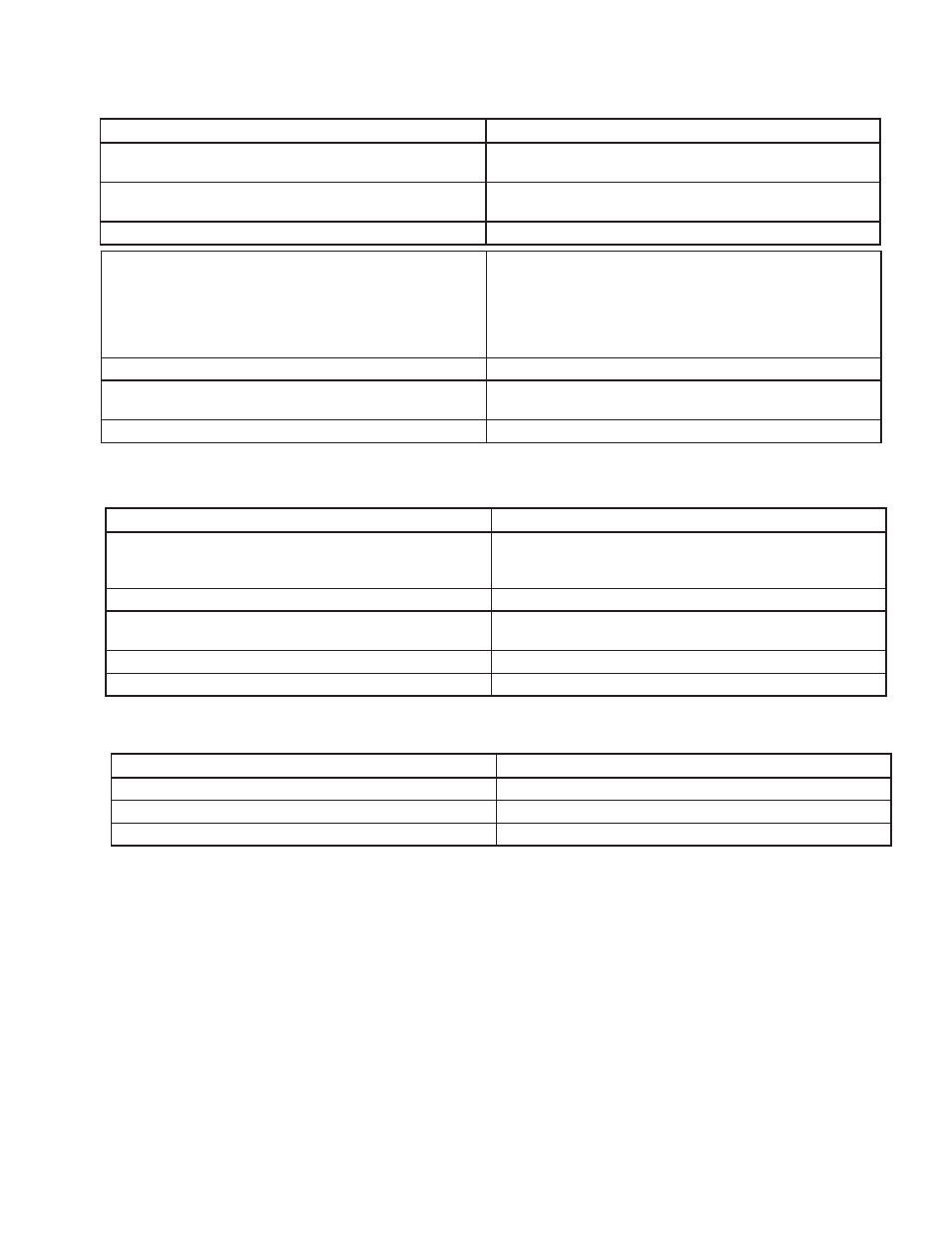
11
IOM-987
Possible Cause
Remedy
A. Excess pressure drop.
A1. Reduce pressure drop conditions.
A2. Convert to reduced trim.
B. Improper actuator bench setting.
B1. Calibrate actuator-to-valve.
B2. Assure proper engagement of act.stem to valve stem.
C. Metal seat design instead of composition seat design. C. Convert valve to composition seat.
4. Valve exhibits "excess" seat leakage.
Possible Cause
Remedy
A. Over-temperature.
A1. Bring process temperature to 450
°
F (232
°
C) or less.
A2. Remove insulation along bonnet; allow direct contact
with ambient air.
B. Misalignment.
B. Realign body-stem-actuator.
C. Wear.
C1. Remove dirt/grit from fl uid.
C2. Reduce cyclic travel.
D. Improper design for applied service.
D. Install alternate packing design.
E. Corrosion of stem.
E. Consider use of Model 988 or 989 or 2296.
Possible Cause
Remedy
A. Improper bonnet bolting draw down.
A. Replace bonnet o-ring and draw down bolting evenly.
B. Corrosion.
B. Consider use of Model 988 or 989 or 2296.
C. Over-temperature.
C. Bring process temperature to 450
°
F (232
°
C) or less.
D. Excess wear.
D1. Oversized valve operating too close to seat, convert to
reduced trim.
D2. Remove particulate.
D3. Possible excess cavitation in liquid service, change
operation parameters.
D4. Re-lap plug-seat surface.
E. Misalignment.
E. Realign body-stem-actuator.
F. Composition seat failure.
F1. Replace soft seat.
F2. Remove "dirty" portion of fl uid causing failure.
G. Seat ring gasket failure.
G. Replace seat ring o-ring.
5. Premature packing leakage.
6. Bonnet gasket leaking.