Verification of flow element resistance – Fluid Components International RF83 Manual Troubleshooting User Manual
Page 2
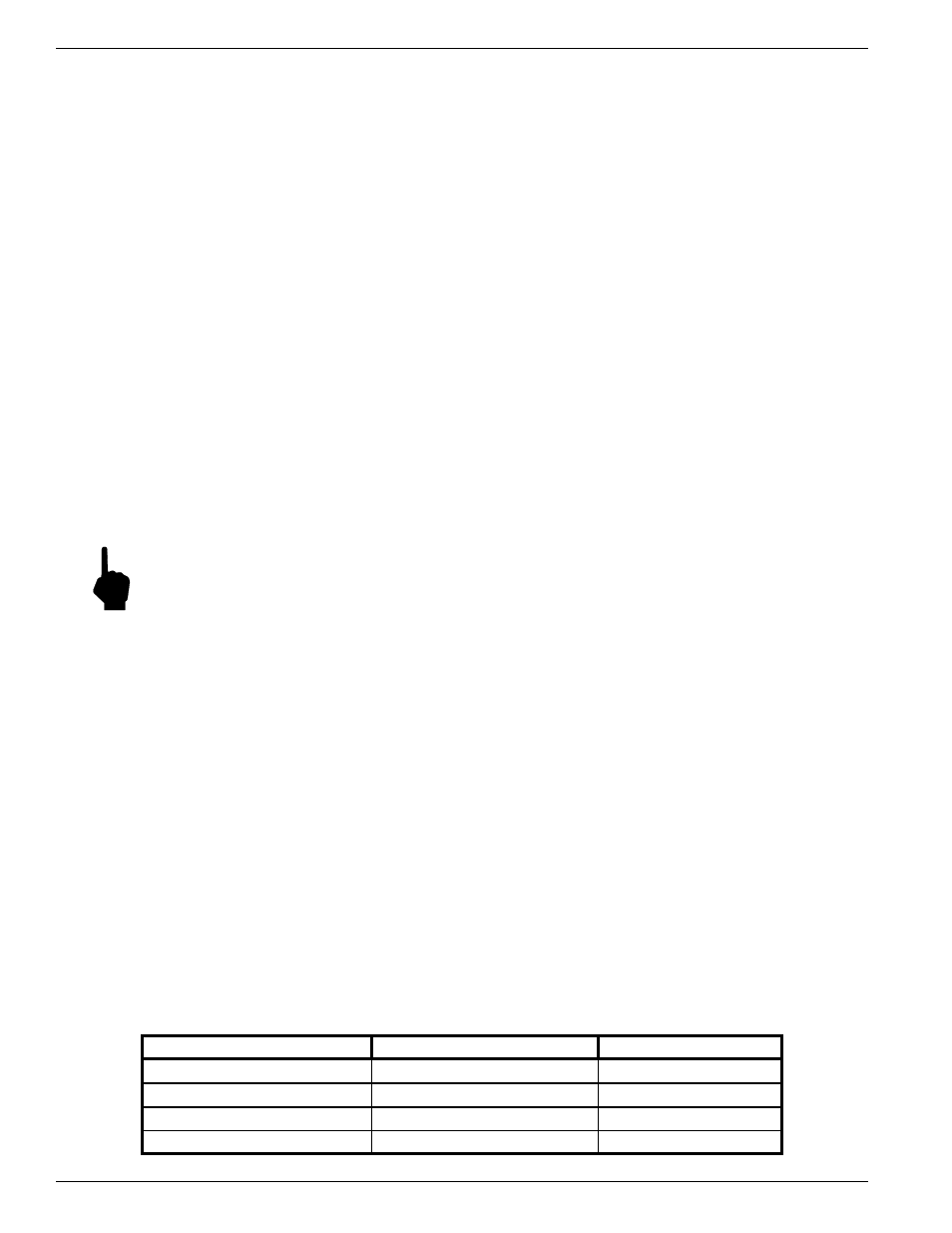
FLUID COMPONENTS INTL
CHAPTER 5 - TROUBLESHOOTING
Model RF83 Flow Switch
5 - 2
Doc. No. 003147 Rev. B
Check Application Design Requirements
Application design problems may occur with first time application instruments, although the design should also be
checked on instruments that have been in operation for some time. If the application design does not match field
conditions, errors occur.
1.
Review the application design with plant operation personnel and plant engineers.
2.
Ensure that plant equipment such as pressure and temperature instruments conform to the actual conditions.
3.
Verify operating temperature, operating pressure, line size, and gas medium.
Control Circuit Dash Number Specification
Verify that wiring is connected per the correct wiring diagram. To find the correct diagram look at the control circuit
dash number printed on the instrument name plate. Compare the dash number to Appendix A, Figure A-10. The
figure will then guide the user to find the appropriate wiring diagrams. If there is a space within the dash number
there is a standard option associated with the blank. See Note 4 in Figures A-10.
Verification of Flow Element Resistance
The measurements are based on a standard (4K ohm RTD at 70°F, or 21°C) flow element. Variation of
±
100 ohms
from nominal is to be expected, depending on temperature. The maximum allowable difference in resistance
between matched RTD's is 1% at ambient temperature (immersed in water). The heater resistance should be 430
±5
ohms for each heater. The heaters are connected in parallel, therefore the combined parallel resistance is 215 ohms.
Be sure to subtract the cable resistance to get the true resistance.
Note:
When the flow element is connected to a remote enclosure control circuit, a shielded cable is to be
used. Be sure that the cable shield is ONLY connected to the control circuit socket, terminal number 7.
The other end of the shield should be left floating.
1.
Turn off the operating power to the instrument.
2.
Gently remove (pull straight out) the control circuit from the socket. Using a DMM, measure the resistance of
sensor A and sensor B sensing elements.
3.
Measure the resistances as found in Table 5-1 to determine if the flow element is functional.
For remote instruments, if there is a faulty reading at the control circuit socket, (control circuit pulled out) make
the resistance measurements found in Table 5-2.
For the remote configuration (the control circuit is in a separate enclosure from the flow element), if an open circuit
exists for one RTD and a value of twice the resistance exists for the other RTD then there is probably a miswiring or
mislabeling problem.
For the local configuration (the control circuit is in the same enclosure as the flow element), if there is an indication
of an open or short in the RTD, the flow element will need to be replaced.
After replacing the flow element, it will be necessary to follow the set point adjustment procedures found in the
Operation Chapter before returning the instrument to service. If a millivolt output option is provided on the control
circuit, the zero adjustment procedure must be performed.
If the flow element resistance is correct, proceed to the voltage verification test.
Table 5-1. Local Flow Element Resistances In Ohms
(control circuit enclosure)
From Terminal (Pin)
To Terminal (Pin)
Expected Ohms*
Heater (7)
Heater (10)
215
Sen A (9)
Com Sen (8)
4000
Sen A (9)
Sen B (7)
8000
Sen B (7)
Com Sen (8)
4000