Technical data, Assembly – Burkert Type BBS-07 User Manual
Page 2
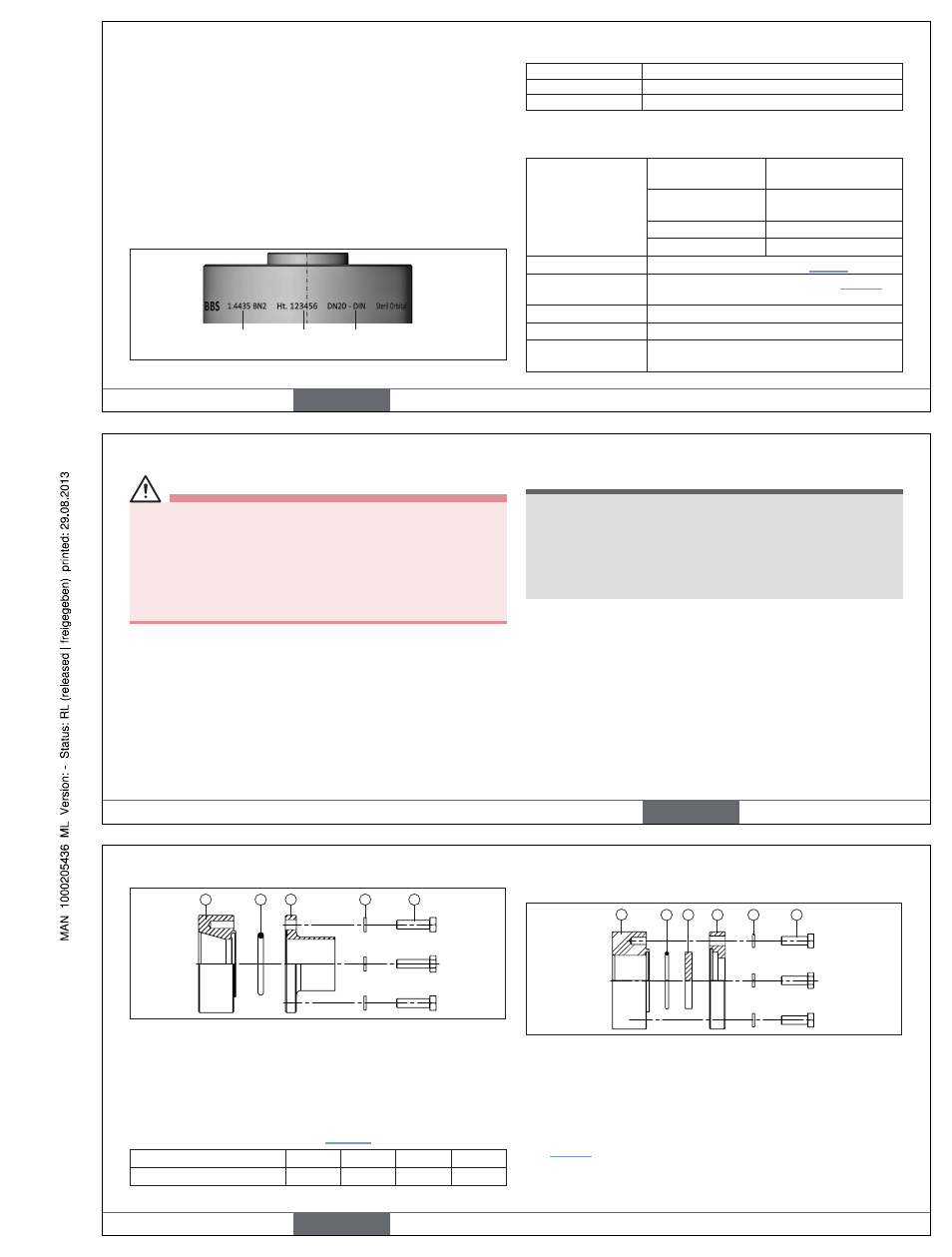
4
5. TECHNICAL DATA
5.1. Conformity
Type BBS-07 tank flange conforms to the EC directives according to
the EC Declaration of Conformity.
5.2. Standards (if applicable)
The applied standards which are used to demonstrate compliance with
the EC Directives are listed in the EC type test certificate and/or the
EC Declaration of Conformity.
5.3. Identification
Information on material, pipe and connection dimensions can be found
on the stamping on the product. The identification number of the
product can be found on the supplied 3.1 certificate.
Material Material
batch number
Nominal connection
diameter with pipe standard
Fig. 1:
Example of identification of the product
5.4. Sealing materials
Seal material
Operating temperature
EPDM
–40 °C to 90 °C, briefly up to 140 °C
FEP
–60 °C to 160 °C, briefly up to 205 °C
Tab. 1: Sealing materials BBS-07 tank flange
5.5. General technical data
Material
comes into contact
with medium
Stainless steel 1.4435
BN2 (316L)
does not comes into
contact with medium
Stainless steel 1.4401
or equivalent
Glass
Borosilicate glass
O-ring
EPDM/FEP
Pipe dimensions
see identification on product (“Fig. 1”)
Permitted appli-
cation temperature
Depending on sealing material, see “Tab. 1”
Ambient temperature –20 °C to +80 °C
Media
Fluids
Operating pressure
-1 to +25 bar (depending on temperature and
size, see data sheet)
english
5
6. ASSEMBLY
WARNING!
Danger – high pressure and discharge of medium!
• When working on the product or the system, always switch off the
pressure and relieve the lines/containers.
• Wear protective equipment if media is hazardous.
Risk of injury from improper assembly!
• Installation must only be carried out by authorized technicians and
with the appropriate tools!
• Secure system from unintentional activation.
6.1. Welding in the tank flange
NOTE!
Leak due to damaged sealing elements!
• Do not weld in the assembled product. It is essential to remove
the O-ring and, if required, glass pane before welding and to pro-
tect the product from dust, flying sparks and other influences!
Leak due to damaged sealing contour!
• To ensure the sealing function, protect the sealing contour during
installation, welding and cleaning procedures.
→
Connect the parts positively in a protective gas shield.
When cleaning the weld seam by grinding or acid cleaning, observe
the following before assembling the connection:
• Carefully remove all grinding dust and acid-cleaning residue.
• Do not damage the label.
• There must be no material abrasion on the sealing edges. Material
abrasion will result in sharp-edged sealing contours and a damaged
seal.
• Check sealing contour for damage.
We recommend preparing a welding report.
english
6
6.2. Assembling tank flange
1
2
3
4
5
Fig. 2:
Assembling BBS-07 tank flange
→
Insert O-ring (2) by hand (do not use any tools or sharp imple-
ments) into the welded-in block flange (1).
→
Carefully attach grooved flange (3) (or clamp). Ensure that the
O-ring is in the correct position.
→
Screw connection using washers (4) and screws (5) (or half
flanges, threaded pins, washers and hexagon cap nuts).
Observe tightening torques (see “Tab. 2”).
Bolt size
M 08
M 10
M 12
M 16
Tightening torque (Nm)
149
280
380
665
Tab. 2: Tightening torque Type BBS-07 tank flange
6.3. Assembling tank flange with inspection
glass
1
2
3
4
5
6
Fig. 3:
Assembling BBS-07 tank flange with inspection glass
→
Insert O-ring (2) by hand (do not use any tools or sharp imple-
ments) into the welded-in block flange (1).
→
Carefully attach glass pane (3). Ensure that the O-ring is in the
correct position.
→
Attach inspection glass cover or both half flanges (4), screw con-
nection using washers (5) and screws (6). Observe torques
(“Tab. 2”).
6.4. Disassembly
Disassembly is in reverse sequence to assembly.
english