Brooks Instrument SLA7810/20 User Manual
Page 24
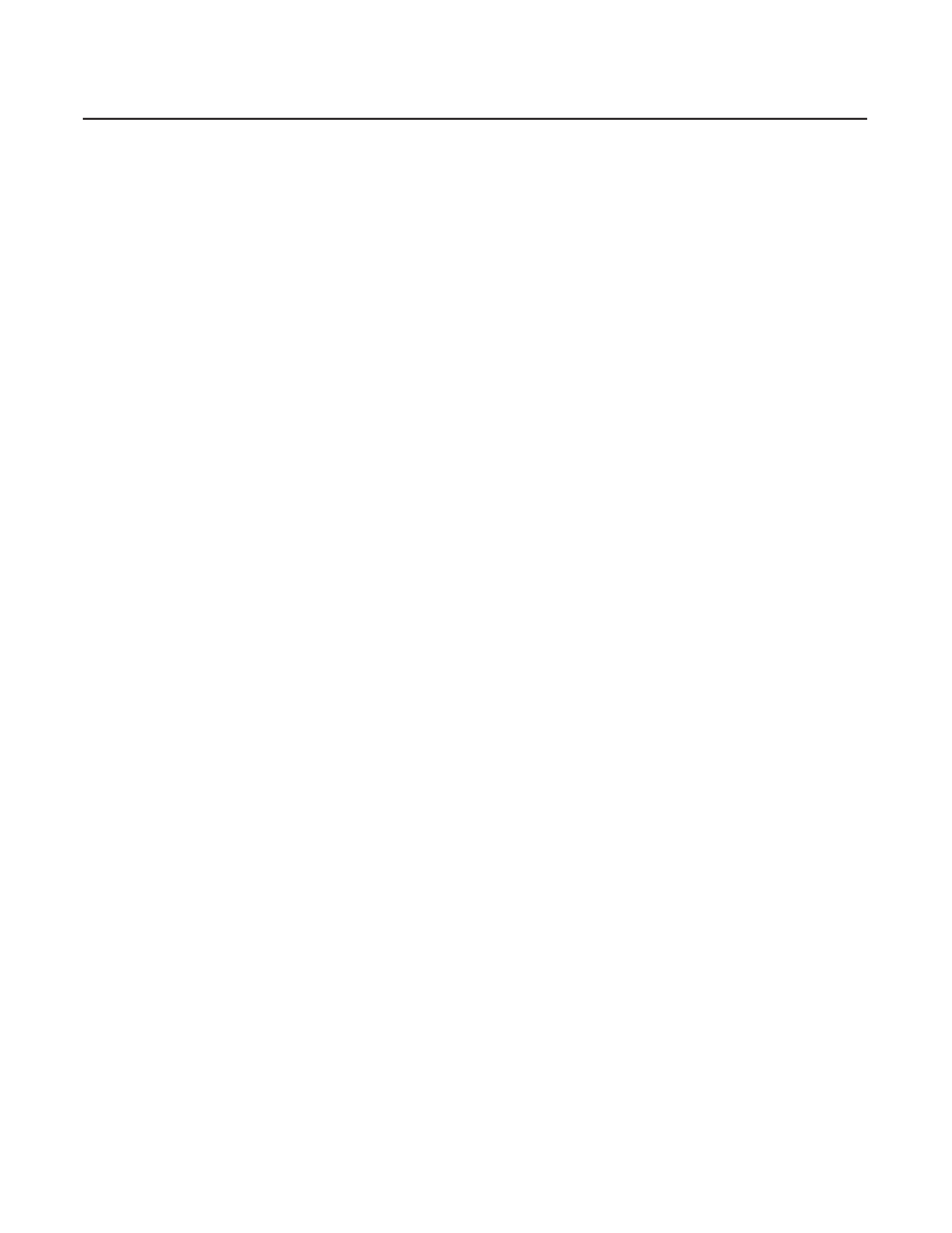
3-2
Section 3 Operation
Installation and Operation Manual
X-PR-SLA7800-PC-eng
Part Number: 541B047AAG
December, 2008
Model SLA7810 & SLA7820
Integral Control
Integral or reset action is an integration of the input error signal over time.
This means that with integral action the value of the manipulated variable
changes at a rate proportional to the error. With integral action present
there can be no offset at steady state since the manipulated variable will
continue to change as long as an error is present.
Characteristics of P.I. Control
By using both proportional and integral control actions, rapid control can be
achieved with out a steady state offset. Typically there is a slight decrease
in system stability due to the presence of the integral mode. The dynamic
response of the system is better than the response would be with integral
alone. Because the two controller modes are interactive the P.I. controller
is somewhat more difficult to tune.
Tuning the P.I. control
Using the Brooks Service tool, read the current values of P. and I. It is
highly recommended that the P. and I. values be recorded before
adjustment. This will allow easy return to the factory settings. The Brooks
Service tool is covered in another document. Increasing the P. parameter
will increase the proportional band thus increasing the system response
time. If the proportional band is too high, the system may overshoot the
setpoint, or oscillate.
Increasing the Integral parameter will increase the integration time, making
the system respond slower, but more stable.
Most applications require fast response time. This can be achieved by
using a low Integral number and a high Proportional number. P. and I.
should be adjusted so the controller reaches setpoint in the minimum time,
without overshoot or oscillation.
Check the adjustment in the system over the expected range of pressures
and flows.