CEMB USA K9 (B) User Manual
Page 11
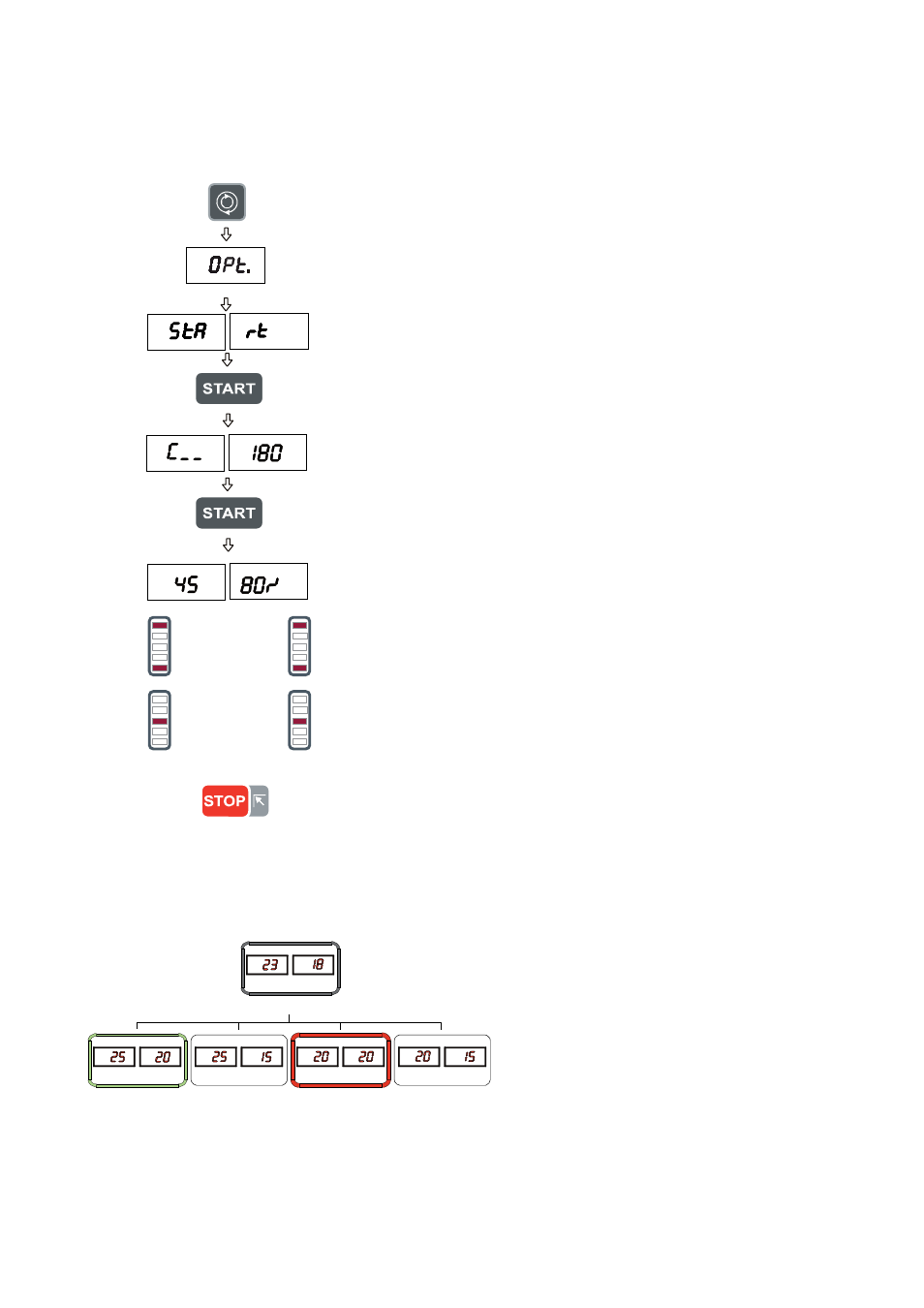
I 0672
- 11
s
sx
x
g
g
g
g
d
dx
x
5
50
0°°
s
sx
x
g
g
g
g
d
dx
x
4
4 g
g
3
3 g
g
1
1 g
g
6
6 g
g
s
sx
x
g
g
g
g
d
dx
x
s
sx
x
g
g
g
g
d
dx
x
s
sx
x
g
g
g
g
d
dx
x
GB
5.2.6 - UNBALANCE OPTIMIZATION
►
This function serves to reduce the amount of weight to be added in order to balance the wheel
▪
It is suitable for static unbalance exceeding 30 g.
▪
This operation is required if no unbalance has been measured previously; other-
wise go to the next step
Mar
▪
k with chalk a reference point on the adapter and rim
With the aid of a tyre changer, turn the rim on the tyre by 180°
▪
Refi t the wheel with the reference mark coinciding between rim and adapter
▪
RH di
▪
splay: percentage reduction
LH display: actual static unbalance which can be reduced by matching
▪
Mark the two positions of the rim and tyre, and turn the rim on the tyre until
▪
the positions correspond in order to obtain the optimization results shown on
the
display.
CANCEL OPTIMISATION IN ANY PHASE.
5.2.7 - AUTOMATIC MINIMIZATION OF STATIC UNBALANCE
►
This program is designed to improve the quality of
balancing without any mental effort or loss of time by
the operator. In fact by using the normal commercially
available weights, with pitch of 5 in every 5 g, and by
applying the two counterweights which a conventional
wheel balancer rounds to the nearest value, there
could be a residual static unbalance of up to 4 g.
The damage of such approximation is emphasized
by the fact that static unbalance is cause of most
of disturbances on the vehicle. This new function,
resident in the machine, automatically indicates
the optimum entity of the weights to be applied by
approximating them in an “intelligent” way according
to their position in order to minimize residual static
unbalance.
TYRE
POSITION
RIM
POSITION
Initial unbalance
phase shift
Possible approximations
residual static
r
esidual static
residual static
Choice with minimum
static residual
With conventional
wheel balancer
residual static