2 electrical installation, 3 electrical connections – PA Industries Magnum Servo Roll Feed SRF-M12/18/24/32/36/48 - Installation and Operating Instructions User Manual
Page 3
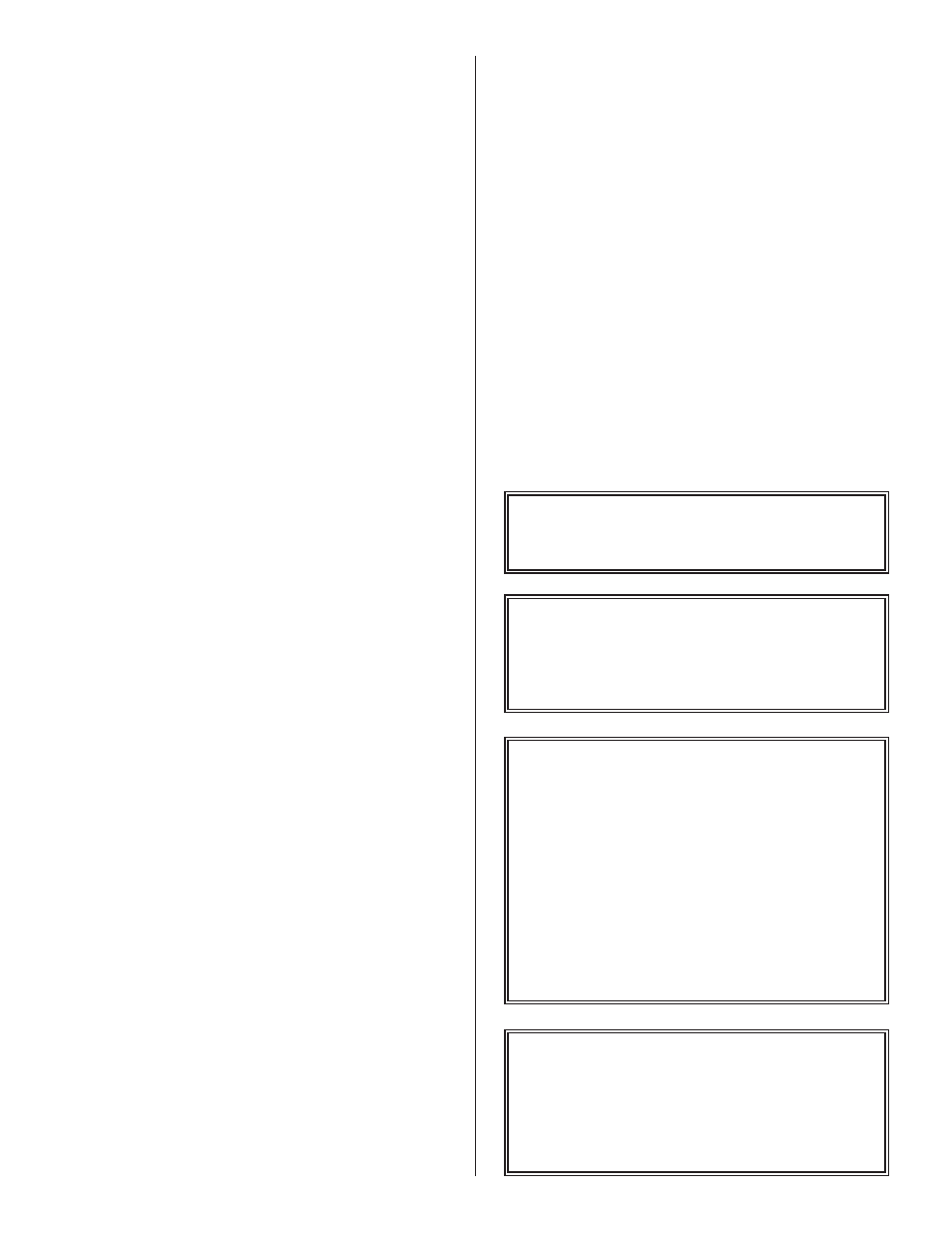
When a new feed pitch is entered into the system,
the built in computer calculates the correct number
of electronic “pulses” it must receive from the motor
mounted encoder in order to rotate the feed rolls
the correct amount. This will accurately position
the strip.
Fifteen and one-half revolutions of the servo motor
shaft produce 1 revolution of the feed rollers. The
motor-mounted optical encoder produces 8000
"pulses" for each revolution of the motor. The
circumference of the lower roll is 14.842 inches.
Example: If a feed pitch/length of 14.842 inches is
entered into the feeder, this will result in exactly
one revolution of the feed rolls. The motor will
accelerate and turn 15.5 turns. This will produce
(15.5 x 8000) =124,000 pulses of the encoder.
The feeder will decelerate and stop when 124,000
pulses are detected. The feeder is now on position.
This entire process happens very quickly, the end
result is an accurately positioned strip exactly
14.842 inches from its starting point. This entire
process happens in milliseconds.
3. INSTALLING YOUR
MAGNUM SERVO FEED
3.1 MECHANICAL INSTALLATION
The Magnum Servo Roll Feed is supplied with
a height adjustable mounting bracket for the feeder.
The adjustment is (± 2.0 inch) from middle
position. The feeder should be securely mounted to
the press frame. A transition bracket is sometimes
required in certain applications requiring more
adjustment.
The feeder should be centered, square, and
perpendicular to the pass line of the press. Use the
24 millimeter square keys on the front mounting
plate for alignment and leveling the feeder. The
feeder should be mounted at a height that will
accommodate the appropriate die sets. Refer to
Figure 2 on Page 4.
The feeder can be used to push or pull stock.
3.2 ELECTRICAL INSTALLATION
The Magnum Servo Roll Feed has been designed
to make electrical connections quickly and easily.
A clean 220 VAC single phase 20 ampere source is
required for trouble free operation. The inputs and
outputs to your press control (i.e. Emergency stop,
Feed advance cam contact, Continue cam contact,
Pilot Release Cam Contact (if used), and Taut
or No Loop Input) must be connected according
to the electrical schematic instructions included
with machine. The motor connects by a factory
installed "Amphenol" (Military Specifications)
3
NOTE:
All connections should be made in accordance
with National Electrical Code (NEC)
requirements and must comply with all local
ordinances.
IMPORTANT!
A #12 MTW grounding conductor must be
installed for proper machine grounding.
NOTE:
A word about electrical “noise”. Most pressroom
environments contain considerable electrical noise.
It is emitted from electro-mechanical press relays,
contacts, and solenoids. While The Magnum
Servo Roll Feed has been designed to minimize
"self generated" electrical noise, it is difficult to
provide protection for all applications. If erratic
system behavior is experienced, then the source
of the "noise" must be suppressed with either a
resistive/capacitive type of suppressor on AC
coils, or “Avalanche” type diodes on DC coils.
NOTE:
The Magnum Servo Roll Feed is fully protected
by a disconnect switch and line fuses. If it
becomes necessary to replace the fuses, use only
exact equivalent fuse types to prevent serious
damage to the system.
Quick connectors. The electrical Control Enclosure
is supplied with a stand/support which may be
placed in any convenient location. The enclosure
may also be mounted in any fixed location as long
as cabling is adequate to reach the feeder. It is not
recommended that the Electrical Enclosure be
mounted directly to the press. The vibrations
caused by the press may result in damage to the
control system.
3.3 ELECTRICAL CONNECTIONS
For more detailed wiring information, refer to
Electrical Schematic A-17514-01 for 220 VAC
or 440 VAC
The main power for the feed system requires a
“clean” 220 VAC single phase 20 ampere source.
A terminal strip is provided in the main control
enclosure to facilitate wiring connections. It is
recommended that #12 MTW (Machine Tool Wire)
be used for the primary power supply input.