5 running the feed 5.4 loading the feed – PA Industries Edge Servo Roll Feed SRF-100(for Serial Numbers 7610697 and higher) User Manual
Page 8
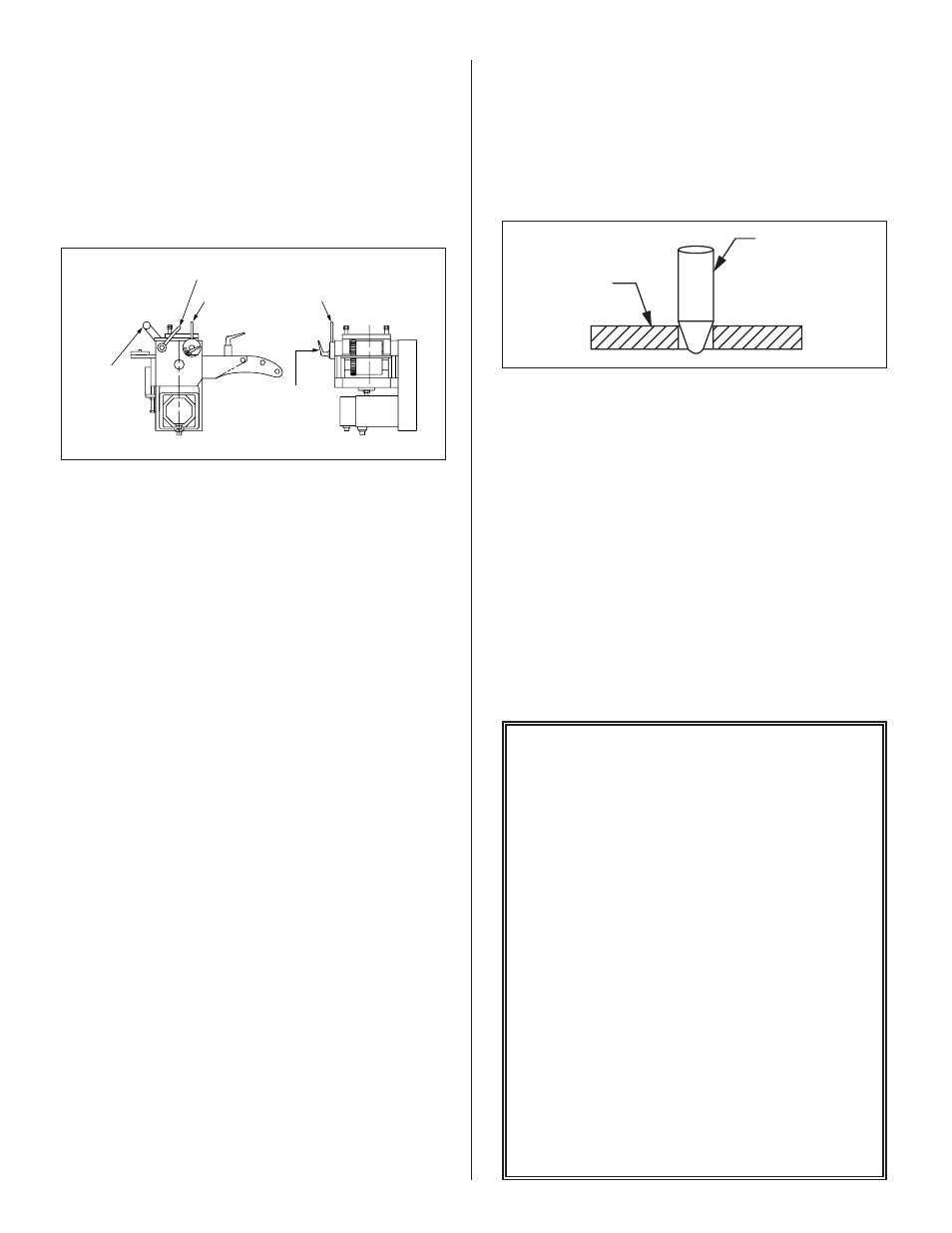
NOTE ABOUT CAMS:
The Feed Advance Cam (open tool): The
feed system uses this press cam for timing
the feeder to the press crankshaft. Although
no shafting or belts actually connect the
press to the feeder, the feed must be "told"
when it is safe to move the strip and when
the feed move must be completed.
• This “connection” is an electrical one,
and not a mechanical one. This gives the
operator/set-up personnel total flexibility in
deciding when the feed progression should
take place.
• Each die set can have a unique “feed
angle”. This “feed angle” is dependent
upon many variables; pilot and punch
length, press stroke, strip forming in the
die, etc.
8
Use the following steps to load the feeder:
(Refer to Figure 3)
1. Record the present settings of the feed advance
cam, continue cam, and pilot release cam into a job
set-up record sheet for future reference to the job
(see Programmable Limit Switch Job Set-Up Sheet).
2. Open the feed rolls by pulling on the Roll
Release Lever. Insert the material through the feed
rolls and close the feed rolls by releasing the Roll
Release Lever.
3. Adjust for the material thickness using the
Material Thickness Adjustment Cam and Adjustable
Lock Screw. Refer to the figure above for proper
setting.
4. Adjust the roll clamping force by pre-loading
the two die springs located on top of the feed
housing. Normal setting for the roll force spring
pre-load is two full turns clockwise from finger
tight. Be sure to use the jam nut to lock the
setting.
5. Using the ‘
JOG FORWARD
’ button on the jog
pendant, advance the material up to the entrance of
the die (but not too far, where the punches would
pierce the material).
6. Check the vertical alignment of the strip. If
necessary, adjust the pass line of the feeder so that
the material is at the proper height.
7. Assuming that the press shut height and the
tool are set up properly, jog the press one or two
strokes without the feed working.
8. Jog the press down slowly observing when the
longest pilot would engage the pilot hole in the
material if the material were there. (Refer to
Figure 4.) Note the press positional readout and
put this setting into your Programmable Limit
Switch (
PLS
) for the ‘
PILOT RELEASE TURN ON
’
setting. The ‘
PILOT RELEASE TURN OFF
’ setting
should be 180. (See Figure 5.)
9. Continue to jog the press slowly until the
longest pilot just comes above the material. Note
the press positional readout and put this setting into
your PLS for the ‘
FEED ADVANCE TURN ON
’
setting. Set the ‘
FEED ADVANCE TURN OFF
’
point approximately 30 degrees less than the pilot
release turn on point. (See Figure 5.)
10. Set the continue cam to turn on at 180 degrees
and to turn off at 200 degrees. This setting should
never need changing. (See Figure 5.)
5.5 RUNNING THE FEED
5.4 LOADING THE FEED
STRIP
PILOT PIN
Figure 4. PILOT PIN
related error. Under ‘
CYCLE STOP
’ or ‘
BATCH
COMPLETE
’ stopping, the output will turn off at
the beginning of the ‘
FEED CAM SIGNAL
’. This
should allow the press to stop near the top of the
stroke. Under ‘
SYNC FAULT
’ or other drive fault
conditions, the ‘
PERMIT PRESS RELAY
’ will turn
off immediately upon detection of the error.
EDGE SRF100-600
ADJUSTABLE
LOCK
SCREW
MATERIAL THICKNESS ADJUSTMENT CAM
ROLL RELEASE LEVER
DRAWING 17415-02
PILOT
LEVER
ADJUST CAM
WITH MAT’L. IN
FEEDER. SET
FOR MINIMAL
PLAY
IN PILOT
LEVER
Figure 3.
- Edge Servo Roll Feed SRF-125 (for Serial Numbers 7610697 and higher) Edge Servo Roll Feed SRF-200 (for Serial Numbers 7610697 and higher) Edge Servo Roll Feed SRF-300 (for Serial Numbers 7610697 and higher) Edge Servo Roll Feed SRF-400 (for Serial Numbers 7610697 and higher) Edge Servo Roll Feed SRF-500 (for Serial Numbers 7610697 and higher) Edge Servo Roll Feed SRF-600 (for Serial Numbers 7610697 and higher)