3 electrical connections, 2 electrical installation – PA Industries Edge Servo Roll Feed SRF-100(for Serial Numbers 7610697 and higher) User Manual
Page 3
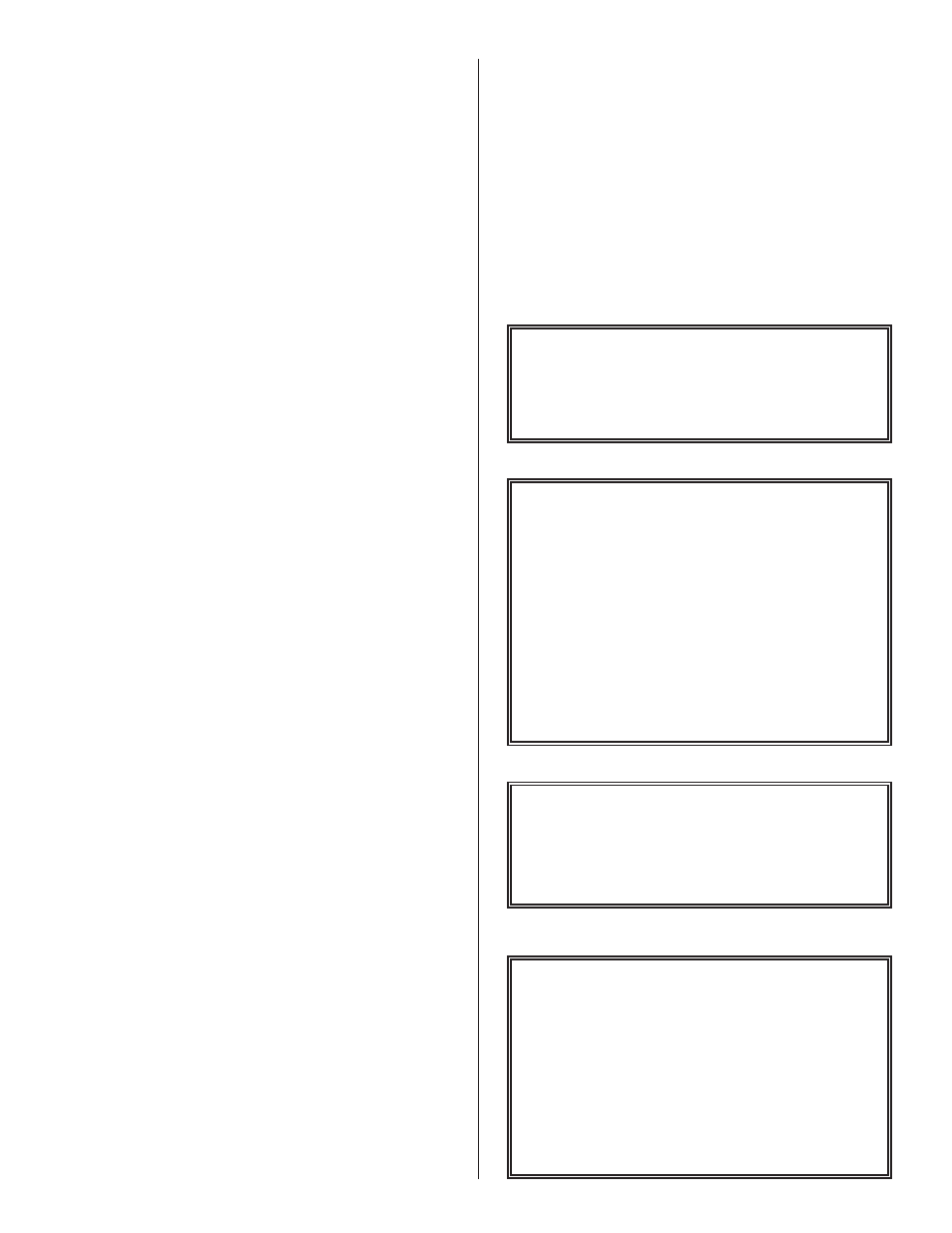
Each revolution of the servo motor produces 8000
encoder pulses. Every 2.909 revolutions of the
servo motor shaft produce 1 revolution of the feed
rollers. The circumference of the lower roll is
approximately 11.142 inches (on the SRF-125).
When a new feed pitch is entered into the system,
the built in computer calculates the correct
number of electronic "pulses" it must receive from
the motor mounted encoder in order to rotate the
feed rolls the correct distance.
Example: If a feed pitch/length of 11.142 inches is
entered into the feeder, this will result in exactly one
revolution of the feed rolls. The motor will acceler-
ate and turn 2.909 turns. This will produce (2.909
x 8000 = 23,272) pulses of the encoder. The feeder
will decelerate and stop when 23,272 pulses are
detected. The feeder is now on position. The end
result is an accurately positioned strip exactly
11.142 inchs from its starting point. This entire
process happens in milliseconds.
3. INSTALLING YOUR EDGE
SERVO FEED
3.1 MECHANICAL INSTALLATION
The Edge Servo Roll Feed is supplied with an
adjustable mounting bracket. The feed should be
securely mounted to the press frame. (A transition
bracket is sometimes required in certain
applications). The feed should be centered, square,
and perpendicular to the pass line of the press.
It should be mounted at a height that will
accommodate the appropriate die sets. The feed
has a pass line height adjustment of ±1.2 inches
(Note: The centerline of the Feeder is NOT the
centerline of the rolls.) Refer to Figure 2 on
Page 4 for dimensioning.
The feeder may be used to push or pull strip stock
through the die.
If pilot locating pins are used in your die sets, the
optional mechanical roll release bracket should be
attached to the press ram. It must be mounted in
such a way as to provide roll release at the proper
time and be adjustable for different die sets.
If the optional electro-pneumatic piloting is
used, another cam switch will be necessary for
controlling feed roll opening and closing.
3.2 ELECTRICAL INSTALLATION
The Edge Servo Roll Feed has been designed to
make electrical connections quickly and easily.
Simply connect the power plug to a "clean" 120
VAC single phase 15 ampere source. (Note: Avoid
having other equipment share the same circuit as the
feeder.) The inputs and outputs to your press control
(i.e. Emergency Stop, Feed Advance Cam Contact, Pilot
Release Cam Contact, Continue Cam Contact, End
of Strip Input) must also be connected for proper
operation. The motor connects by factory installed
"Amphenol" (Military Specifications) Quick connectors.
3.3 ELECTRICAL CONNECTIONS
For more detailed wiring information, refer to
Electrical Schematic A-17557-01 for 115 VAC and
Electrical Schematic A-17557-02 for 230 VAC.
NOTE:
All connections should be made in accordance
with National Electrical Code (NEC)
requirements and must comply with all local
ordinances.
NOTE:
A word about electrical “noise”. Most pressroom
environments contain considerable electrical noise.
It is emitted from electro-mechanical press relays,
contacts, and solenoids. While The Edge Servo
Roll Feed has been designed to minimize
"self generated" electrical noise, it is difficult to
provide protection for all applications. If erratic
system behavior is experienced, then the source
of the "noise" must be suppressed with either a
resistive/capacitive type of suppressor on AC
coils, or "Avalanche" type diodes on DC coils.
NOTE:
The Edge Servo Roll Feed is fully protected
by line fuses. If it becomes necessary to replace
the fuses, use only exact equivalent fuse types to
prevent serious damage to the system.
NOTE:
The electrical control enclosure is supplied with
a stand/support which may be placed in any
convenient location. The enclosure may also be
mounted in any fixed location as long as the
cabling is adequate to reach the feed. It is not
recommended that the electrical enclosure be
mounted directly to the press. The vibrations
caused by the punch press can result In
damage to the control system.
3
- Edge Servo Roll Feed SRF-125 (for Serial Numbers 7610697 and higher) Edge Servo Roll Feed SRF-200 (for Serial Numbers 7610697 and higher) Edge Servo Roll Feed SRF-300 (for Serial Numbers 7610697 and higher) Edge Servo Roll Feed SRF-400 (for Serial Numbers 7610697 and higher) Edge Servo Roll Feed SRF-500 (for Serial Numbers 7610697 and higher) Edge Servo Roll Feed SRF-600 (for Serial Numbers 7610697 and higher)