Spencer 4BOB Multistage Centrifugal Blowers User Manual
Page 6
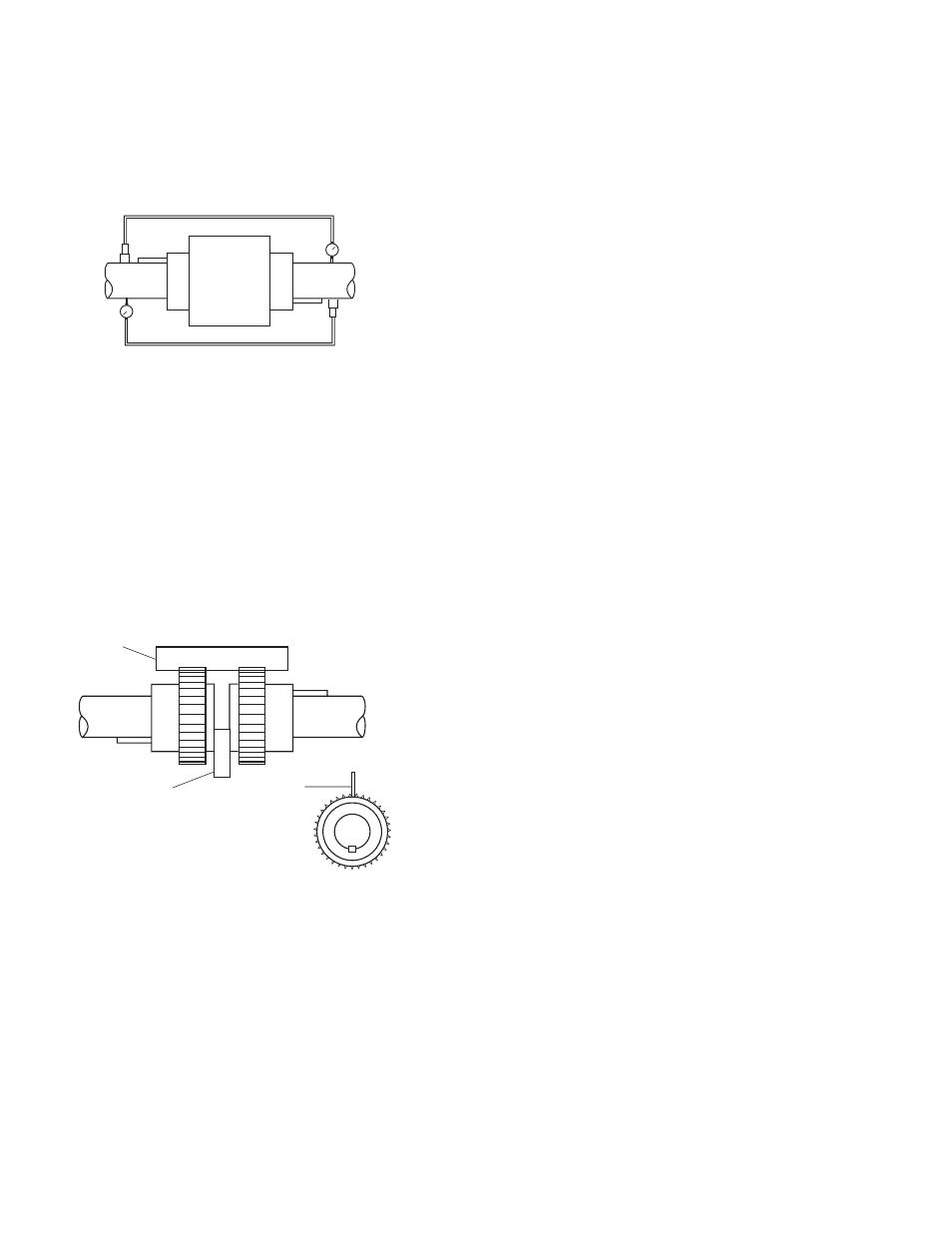
66
LLaasseerr AAlliiggnnm
meenntt TTeecchhnniiqquuee ((RReeccoom
mm
meennddeedd))
Laser systems have significant advantages such as reduced
maintenance costs and energy consumption; prolonged life for
bearings, seals and couplings; decreased bearing temperatures
and lower vibration levels. Many laser systems also identify and
measure soft foot conditions.
NOTE: Consult an alignment specialist if laser equipment is not
available.
RReevveerrssee IInnddiiccaattoorr M
Meetthhoodd ((PPeerrm
miissssiibbllee))
This method may be done electronically following the instru-
ment manufacturerʼs instructions or by means of dial indicators
as follows:
1. Reinstall the coupling sleeve, seal and snap ring.
2. Clamp dial indicators on shafts 180° apart as shown.
3. Place indicator probes on opposite shafts as shown.
4. Rotate both shafts simultaneously in the correct operating
direction, taking readings at 90° intervals.
5. Adjust motor to achieve parallel and angular alignment. If
questions arise, contact the Spencer Service Department.
SSttrraaiigghhtteeddggee M
Meetthhoodd ((PPeerrm
miissssiibbllee))
1. Remove old lubricant and clean the hub teeth.
2. Set a machine shop quality straightedge across the coupling
hubs (at the root diameter of the gear teeth).
3. Adjust the motor so the straightedge is evenly supported
between the coupling hubs at the 3, 6, 9 and 12 oʼclock
positions.
4. Using a feeler gage, measure the clearance between the
coupling hubs at the 3, 6, 9 and 12 oʼclock positions.
5. Adjust the motor so the gap is identical at all four positions
and in accord with the table of hub to hub gaps.
CCoouupplliinngg AAlliiggnnm
meenntt wwiitthh SSlleeeevvee BBeeaarriinngg M
Moottoorrss
CCAAUUTTIIO
ONN:: CCoom
mpplleettee tthhee ffoolllloowwiinngg pprroocceedduurreess bbeeffoorree
aatttteem
mppttiinngg ccoouupplliinngg aalliiggnnm
meenntt wwiitthh sslleeeevvee bbeeaarriinngg m
moottoorrss..
Use a flange-type gear coupling for both 1800 and 3600 RPM
motors. Do not use a sleeve-type coupling.
Sleeve bearing motors have a specified end play. End play limits
and the magnetic center (where motor will run) should be
scribed on the shaft by the manufacturer.
Use the following procedure to align a sleeve bearing motor
with a blower.
1. Make sure the motor shaft is level.
2. Position the motor so that when the rotor is pushed toward
the blower as far as it will go, there will 0.030" clearance
between the ends of the motor and blower shafts (or the
alignment faces on the coupling hubs).
3. Proceed with coupling alignment using the appropriate
instructions.
AAlliiggnnm
meenntt TTiippss
• Make sure the blower is level before alignment.
• Mark the axial location of the motor before alignment as a
reference point to be sure it does not move.
• Avoid disturbing any factory-installed shims unless they are
to be replaced.
• Do soft foot corrections first; loosen all mounting bolts before
correcting any foot.
• During the final vertical adjustment of the motor, work on
one side at a time, loosening the jack bolts first so the motor
does not move laterally as mounting bolts are loosened.
• Use the smallest shim that will slide over the mounting bolts.
• Minimize the number of shims. One thick shim and 2-3 thin
shims are usually satisfactory.
• Remove all traces of dirt or contaminants from shims and
machine parts.
• Use stainless steel shims only.
• Never reuse shims.
CCAAUUTTIIO
ONN:: AAfftteerr eeaacchh aalliiggnnm
meenntt cchheecckk,, aadddd ccoouupplliinngg lluubbrrii--
ccaanntt iiff rreeqquuiirreedd..
W
WAARRNNIINNG
G:: RREEPPLLAACCEE TTHHEE CCO
OUUPPLLIINNG
G G
GUUAARRDD BBEEFFO
ORREE
RREESSTTAARRTTIINNG
G TTHHEE BBLLO
OW
WEERR..
Blower Shaft
Motor Shaft
Blower Shaft
Motor Shaft
Straightedge
Straightedge
Feeler Gage
Motor
Shaft