Spencer 4BOB Multistage Centrifugal Blowers User Manual
Page 13
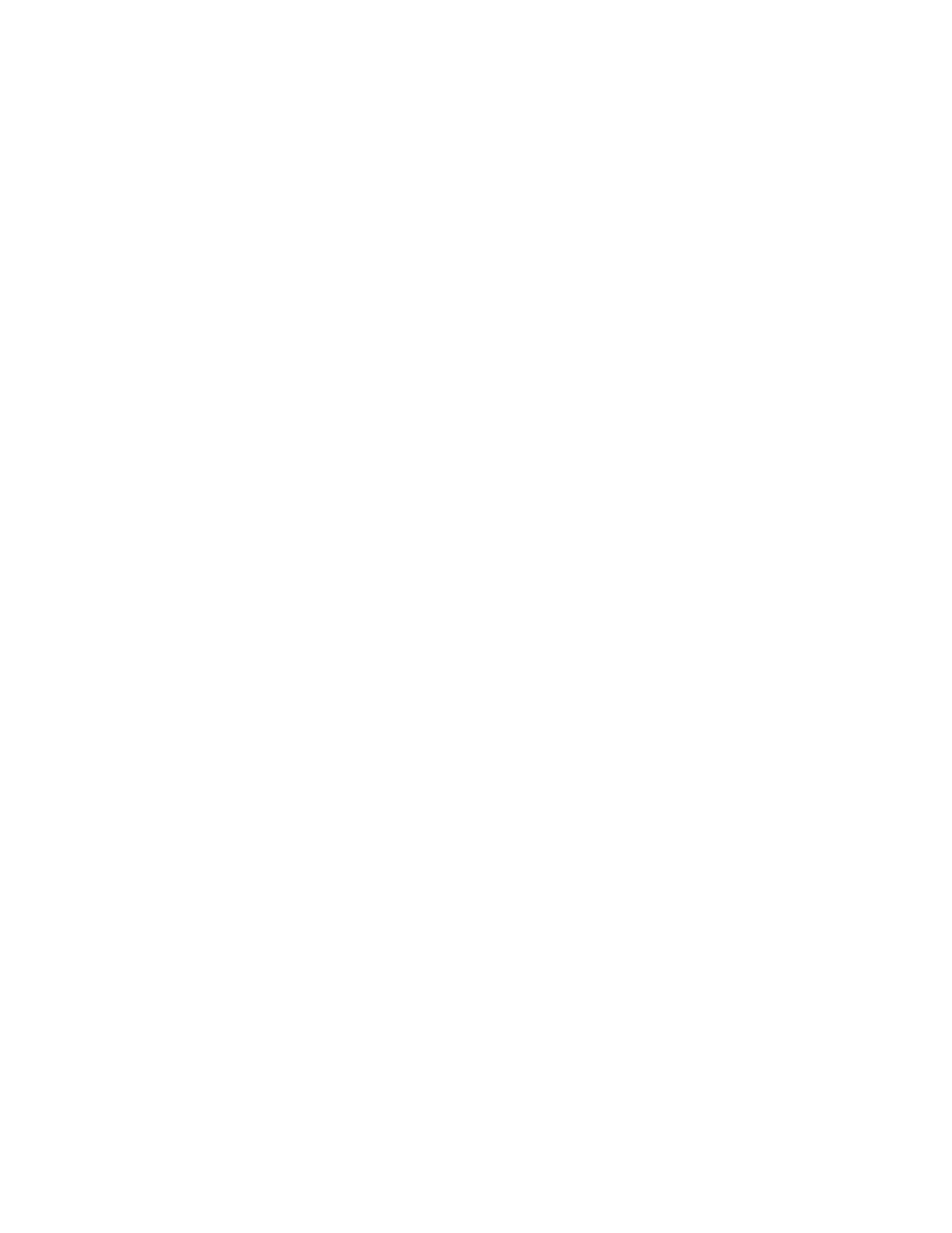
1133
DDiissaasssseem
mbbllyy aanndd RReeaasssseem
mbbllyy
IInnssttrruuccttiioonnss,, 44BBO
OHH
W
WAARRNNIINNG
G:: DDIISSCCO
ONNNNEECCTT AANNDD LLO
OCCKK O
OUUTT EELLEECCTTRRIICCAALL
PPO
OW
WEERR BBEEFFO
ORREE PPEERRFFO
ORRM
MIINNG
G M
MAAIINNTTEENNAANNCCEE..
CCAAUUTTIIO
ONN:: PPaarrttss m
muusstt bbee rreeaasssseem
mbblleedd iinn eexxaaccttllyy tthhee ssaam
mee
rreellaattiivvee ppoossiittiioonn.. TThheerreeffoorree,, iitt iiss rreeccoom
mm
meennddeedd tthhaatt eeaacchh ppaarrtt
bbee ttaaggggeedd aass iitt iiss rreem
moovveedd ffrroom
m tthhee m
maacchhiinnee ttoo ffaacciilliittaattee llaatteerr
rreeaasssseem
mbbllyy.. iitt iiss eessppeecciiaallllyy iim
mppoorrttaanntt tthhaatt tthhee llooccaattiioonn ooff
eeaacchh iim
mppeelllleerr,, aass wweellll aass iittss ppoossiittiioonn oonn tthhee sshhaafftt,, bbee m
maarrkkeedd..
When ordering replacement impellers and deflectors, refer to
notes on accompanying illustrations.
DDiissaasssseem
mbbllyy
1. Remove End Head Bolts (8) and End Head (11).
2. On other than keyed construction, mark the shaft (13) and
impeller (10) hub with an arbitrary 12 oʼclock reference point.
Remove the first stage impeller (10A) and mark it for refer-
ence during reassembly. On keyed construction, remove
snap ring. Remove impeller (10A) and its hub spacer and any
shims, marking them for replacement in their proper position.
3. Check axial position of each deflector (9) at four radial points
with reference to end of housing and record for reference
when reassembling unit.
4. Remove spacer (15) holding rope packing (18) in place.
Mark spacer for reference during reassembly.
5. Remove rope packing (18) holding deflector in place.
Remove deflector (9). Mark for reference during reassembly.
6. Proceed to remove remaining stages in the same way,
marking each component to insure proper reassembly.
Note: Division Head (4) cannot be removed.
7. Rotate the blower shaft (13) so that the keyway is in the 12
oʼclock position. Mark the motor shaft and coupling hub to
show the corresponding 12 oʼclock position. Remove snap
ring on blower side of coupling (1) and slide coupling sleeve
back.
8. Remove motor mounting bolts and slide motor (23) back.
Identify and secure individual motor shim packs under each
motor foot for reassembly.
9. Unbolt division head packing plate (6A) and slide packing
plate and packing (6) back on the shaft.
10. Mark the blower end and coupling ends of the bracket (7) for
reference. Remove bearing bracket hold-down bolts and
slide bracket/shaft assembly out of the housing.
11. Using heat and a puller, remove the coupling hub from the
shaft.
12. Unbolt the bearing caps and remove. These caps are NOT
identical so label the coupling end and blower end caps
clearly. Remove the bearings (5 & 5A) from the shaft.
Remove the shaft from the bracket.
RReeaasssseem
mbbllyy
1. Assemble the shaft (13) in the bracket with new bearings (5
& 5A) and grease. Assemble the caps, being careful to place
the correct cap on each end.
2. Using heat, assemble the coupling hub on the shaft (13).
3. Place the division head packing plate (6A) and packing (6)
on the shaft. If for any reason the packing (6) is damaged,
replace it. Install the bracket/shaft assembly into the housing
in its original position. Be sure that the shaft is centered in
the housing. Assemble the packing (6) and packing plate
(6A) to the division head.
4. Move the motor (23) back into its original position. Insure an
adequate gap between the coupling hubs. Align the motor
(23) to the blower shaft (13) following the instructions on
page 5 of this manual.
5. Rotate the blower shaft to the 12 oʼclock position and align
the corresponding mark on the motor coupling hub. Recouple
the motor (23) to the shaft (13) and run the assembly to
check for vibration. If excessive vibration is present, check
the shaft (13) for runout.
6. On keyed construction, the impellers (10), spacers and
shims are reassembled in precise reverse order of their dis-
assembly. Verify clearance at each stage. On other than
keyed construction, place the first impeller (10C) on the shaft
up against the division head (4). Mark the shaft (13) approxi-
mately 1/8” behind the impeller and withdraw the impeller to
this point. This will insure a clearance of 1/8” behind the
impeller. Tighten the hub securely.
7. Inspect the interstage packing (14A), if applicable, on
deflector (9B) and replace if damaged.
8. Place deflector (9B) back tightly against the stops in the
casing. Install the rope packing (18) firmly into the groove,
using a suitable tool.
9. Install the next impeller (10B) on the shaft up against the
deflector (9B). Mark the shaft approximately 1/8” out and
withdraw the impeller to this point. Tighten the hub securely.
10. Install the spacer (15) into the housing. Make sure spacer
and deflector (9B) are pressed back tightly and at a uniform
distance from the end of the housing at four points.
11. Proceed in a like manner with remaining impellers, spacers
and deflectors.
12. Reassemble the end head (11) to the housing using a new
end head gasket (16).
BBaallaanncciinngg
Each machine is fully tested before leaving the Spencer factory
to be sure vibrations, if any, are well within specifications for that
particular machine. However, rough handling during shipment or
improper disassembly and reassembly of a machine can upset its
balance and/or result in excess vibration.
If there is any excessive vibration due to an unbalanced condition
after assembly, use the following procedure:
1. Check coupling for misalignment. If realignment does not
correct the vibration, change the relative position of machine
shaft and motor shaft in increments of 90° until the smoothest
position is found.
2. If vibration persists, shut the blower down. Mark the position
of end impeller hub on the shaft. Loosen bolts or screws
securing the impeller. Rotate impeller 90° on shaft. Retighten
impeller. Run machine again at operating speed, and check
for vibration. Repeat this process until the best position is
located for impeller on shaft so that there is no vibration in
the machine.
NOTE: In the event of problems following repair procedures,
contact the Spencer Service Department or your Spencer
Representative, describing the nature of the difficulty. Also furnish
the machine serial number.