Hoffman specialty – Bell & Gossett DN0162F HS Vented Boiler Feed Units Series HBF and VBF User Manual
Page 4
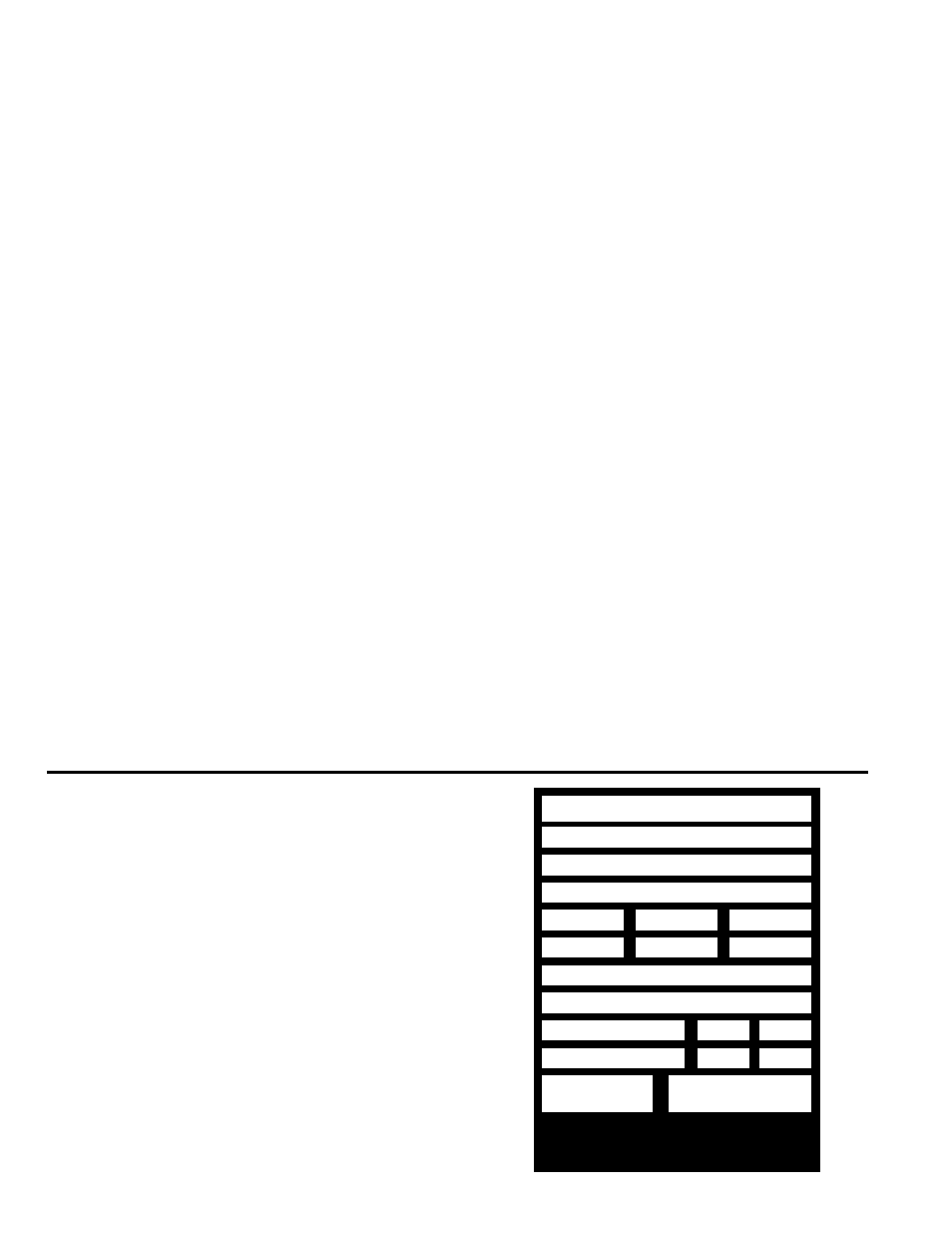
4
TROUBLE SHOOTING PROCEDURES
All units are thoroughly tested at the factory before shipment.
They should operate satisfactorily without further adjustment if
properly installed and provided they have not been damaged
by rough handling in transit. If system or unit performance is
not satisfactory, refer to the following check list.
Pump Will Not Start
1. The power supply has been interrupted, disconnect switch
is open or selector switch is improperly positioned.
2. Incorrect voltage for motor. Check voltage and wiring with
motor characteristics.
3. Incorrect starter coil for power supply.
4. The overload relays and the starter have tripped out and
must be reset. Ambient temperature may be too high.
5. Check pump controls or other controls for proper operation.
6. Wiring to control cabinet is incorrect or connections are loose.
7. The basket strainer is dirty thus restricting flow into the
receiver. Clean periodically.
8. Boiler is full or boiler control switch is defective.
Pumps Runs Continuously
1. Steam traps are blowing through causing condensate to re-
turn at excessive temperatures. This may reduce the capacity
of pump below its rating. Traps should be repaired or replaced.
2. Pump discharge pressure is less than operating pressure of
the boiler.
3. The total required pressure at the pump discharge is greater
than the pressure for which the pump was designed. Check
the total pressure which includes atmospheric pressure, the
friction head and the static head.
4. A valve in the discharge line is closed or throttled too tightly.
5. Check valve is installed backwards.
6. The impeller eye is clogged.
7. Pump is too small for system.
8. Pump is running backwards.
Boiler Feed Pump is Noisy
1. The pump is working against a lower pressure than
designed for. While pump is discharging, adjust plug cock
in discharge line until pressure at pump approaches pump
rated pressure.
2. Excessive condensate temperature. Correct system conditions.
3. Magnetic hum or bearing noise in motor. Consult motor
manufacturer's authorized serviced station nearest unit
location.
4. Starter chatters. Trouble is caused by low line voltage, poor
connections, defective starter coil, or burned contacts.
5. Pump is running backward.
The System is Noisy
1. Banging in the steam mains is usually caused by steam
passing by condensate that has collected in low lying points
in the line. These problems can be eliminated by dripping
low points, properly supporting the pipe, or by increasing
the pitch of the lines.
2. Improper dripping of the steam mains and risers; where
there is a rise in the steam main, or where it branches off
into a riser, a drip trap must be installed in the drain line.
3. The piping is too small to drain properly.
4. A defective steam trap is holding condensate in steam sup-
ply line.
5. Defective check valve permits steam, to vent thru pump into
the boiler feed tank.
6. A priming boiler is discharging water with the steam. Con-
sult boiler manufacturer.
Excessive Water Overflow From Unit
1. Receiver sized too small to accommodate system surges.
2. Water make-up valve open or float set too high.
3. Water make-up valve leaks.
4. Supply water pressure exceeds 30 psi (2.0 bar). Install
Pressure Reducing Valve.
HOFFMAN SPECIALTY
SERIES
MODEL
SERIAL
GPM
PSI
PUMP
CFM
IN. HG.
PUMP
DWGS
POWER V.
115
PH.
HZ 60
CONTROL V.
PH. 1
HZ 60
TOTAL
F.L. AMP.
LARGEST MOTOR
F.L. AMP.
Bell & Gossett
Morton Grove, IL, U.S.A.
DN0016
DEALER SERVICING
If trouble occurs that cannot be rectified, contact your local
B&G representative. He will need the following information in
order to give you assistance.
1. Complete nameplate data of pump and motor. SEE RATING
NAMEPLATE.
2. Suction and discharge pipe pressure gauge readings.
3. Ampere draw of the motor.
4. A sketch of the pump hook-up and piping.
5. Provide complete information on boiler control switches and
any motorized or solenoid valves in the boiler feed piping.
®