Advanced instruments inc – Analytical Industries GPR-2600 Series Oxygen Analyzer User Manual
Page 7
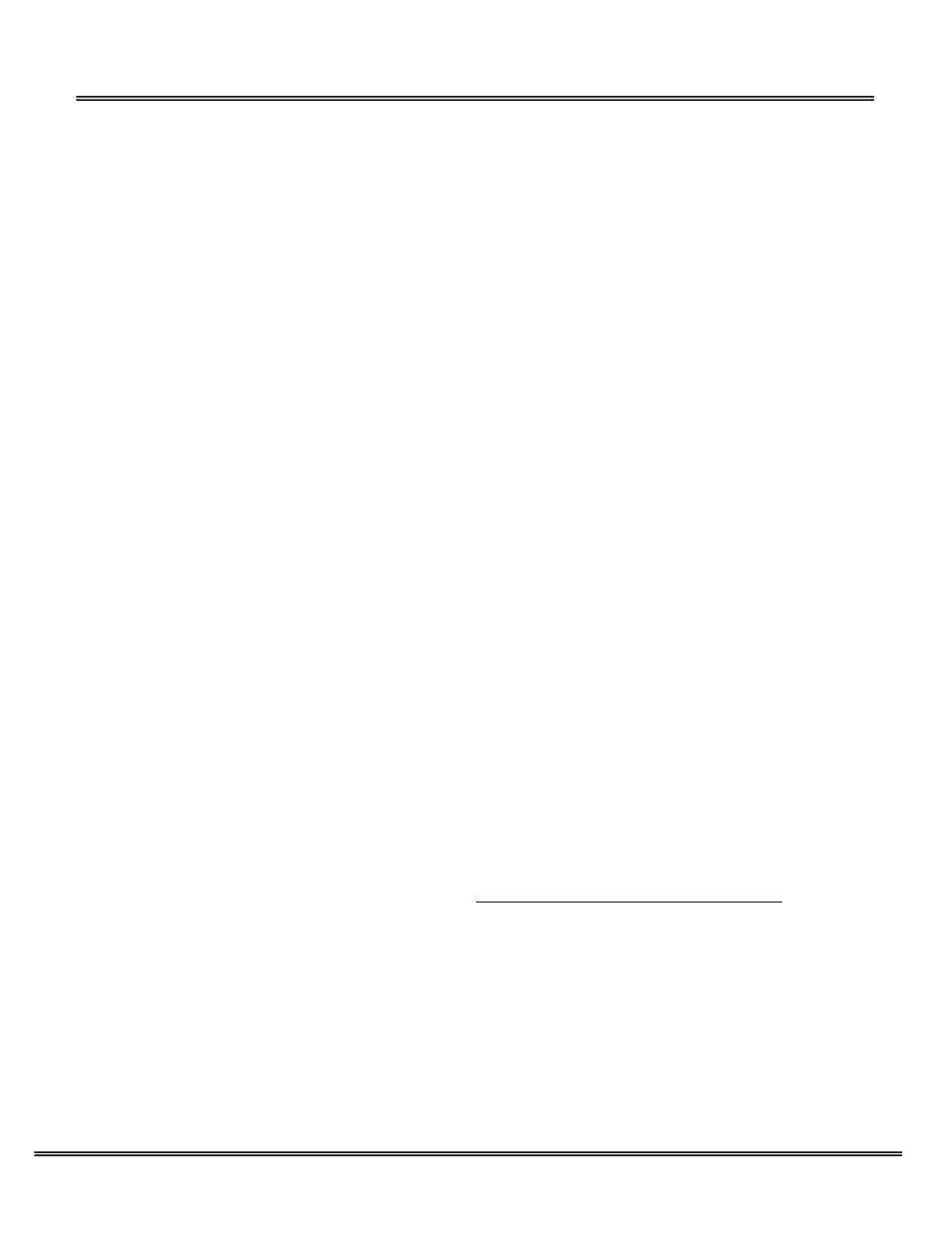
Advanced Instruments Inc.
7
Outlet Pressure: In positive pressure applications the vent pressure must be less than the inlet, preferably atmospheric.
Flow Rate: Flow rates of 1-5 SCFH cause no appreciable change in the oxygen reading. However, flow rates above 5 SCFH
generate backpressure and erroneous oxygen readings because the diameter of the integral tubing cannot evacuate the sample
gas at the higher flow rate. The direction the sample gas flows is not important, thus either tube fitting can serve as the inlet or
vent – just not simultaneously.
A flow valve upstream (with flow indicator positioned downstream) of the sensor is recommended as a means of controlling the
flow rate of the sample gas, minimizing air leaks and produce optimum accuracy. A flow rate of 2 SCFH or 1 liter per minute is
recommended for optimum performance.
Caution: Do not place your finger over the vent (it pressurizes the sensor) to test the flow indicator when gas is flowing to the
sensor. Removing your finger (the restriction) generates a vacuum on the sensor and may damage the sensor (voiding the
sensor warranty). To avoid generating a vacuum on the sensor (as described above) during operation, always select and install
the vent fitting first and remove the vent fitting last.
Application Pressure - Positive: A flow indicator with integral metering valve positioned upstream of the sensor is
recommended for controlling the sample flow rate between 1-5 SCFH. To reduce the possibility of leakage for low ppm
measurements, position a metering needle valve upstream of the sensor to control the flow rate and position a flow indicator
downstream of the sensor. If necessary, a pressure regulator (with a metallic diaphragm is recommended for optimum
accuracy, the use of diaphragms of more permeable materials may result in erroneous readings) upstream of the flow control
valve should be used to regulate the inlet pressure between 5-30 psig.
Caution: If the analyzer is equipped with a H2S scrubber as part of an optional sample conditioning system, inlet pressure
must not exceed 30 psig.
Application Pressure - Atmospheric or Slightly Negative: For accurate ppm range oxygen measurements, an optional
external sampling pump should be positioned downstream of the sensor to draw the sample from the process, by the sensor
and out to atmosphere. A flow meter is generally not necessary to obtain the recommended flow rate with most sampling
pumps.
Caution: If the analyzer is equipped with an optional flow indicator with integral metering valve or a metering flow control
valve upstream of the sensor - open the metering valve completely to avoid drawing a vacuum on the sensor and placing an
undue burden on the pump. If pump loading is a consideration, a second throttle valve on the pump’s inlet side may be
necessary to provide a bypass path so the sample flow rate is within the above parameters.
Recommendations to avoid erroneous oxygen readings and damaging the sensor:
¾ Do not place your finger over the vent (it pressurizes the sensor) to test the flow indicator when gas is flowing to the
sensor. Removing your finger (the restriction) generates a vacuum on the sensor and may damage the sensor (thus voiding
the sensor warranty).
¾ Assure there are no restrictions in the sample or vent lines
¾ Avoid drawing a vacuum that exceeds 14” of water column pressure – unless done gradually
¾ Avoid excessive flow rates above 5 SCFH which generate backpressure on the sensor.
¾ Avoid sudden releases of backpressure that can severely damage the sensor.
¾ Avoid the collection of liquids or particulates on the sensor, they block the diffusion of oxygen into the sensor - wipe away.
¾ If the analyzer is equipped with an optional integral sampling pump (positioned downstream of the sensor) and a flow
control metering valve (positioned upstream of the sensor), completely open the flow control metering valve to avoid
drawing a vacuum on the sensor and placing an undue burden on the pump.
Moisture & Particulates: Installation of a suitable coalescing or particulate filter is required to remove condensation, moisture
and/or particulates from the sample gas to prevent erroneous analysis readings and damage to the sensor or optional
components. Moisture and/or particulates do not necessarily damage the sensor, however, collection on the sensing surface can
block or inhibit the diffusion of sample gas into the sensor resulting in a reduction of sensor signal output – and the appearance
of a sensor failure when in fact the problem is easily remedied by blowing on the front of the sensor. Consult the factory for
recommendations concerning the proper selection and installation of components.
Moisture and/or particulates generally can be removed from the sensor by opening the sensor housing and either blowing on
the sensing surface or gently wiping or brushing the sensing surface with damp cloth.