Advanced instruments inc, Sampling, Standby – Analytical Industries GPR-2600 Series Oxygen Analyzer User Manual
Page 43
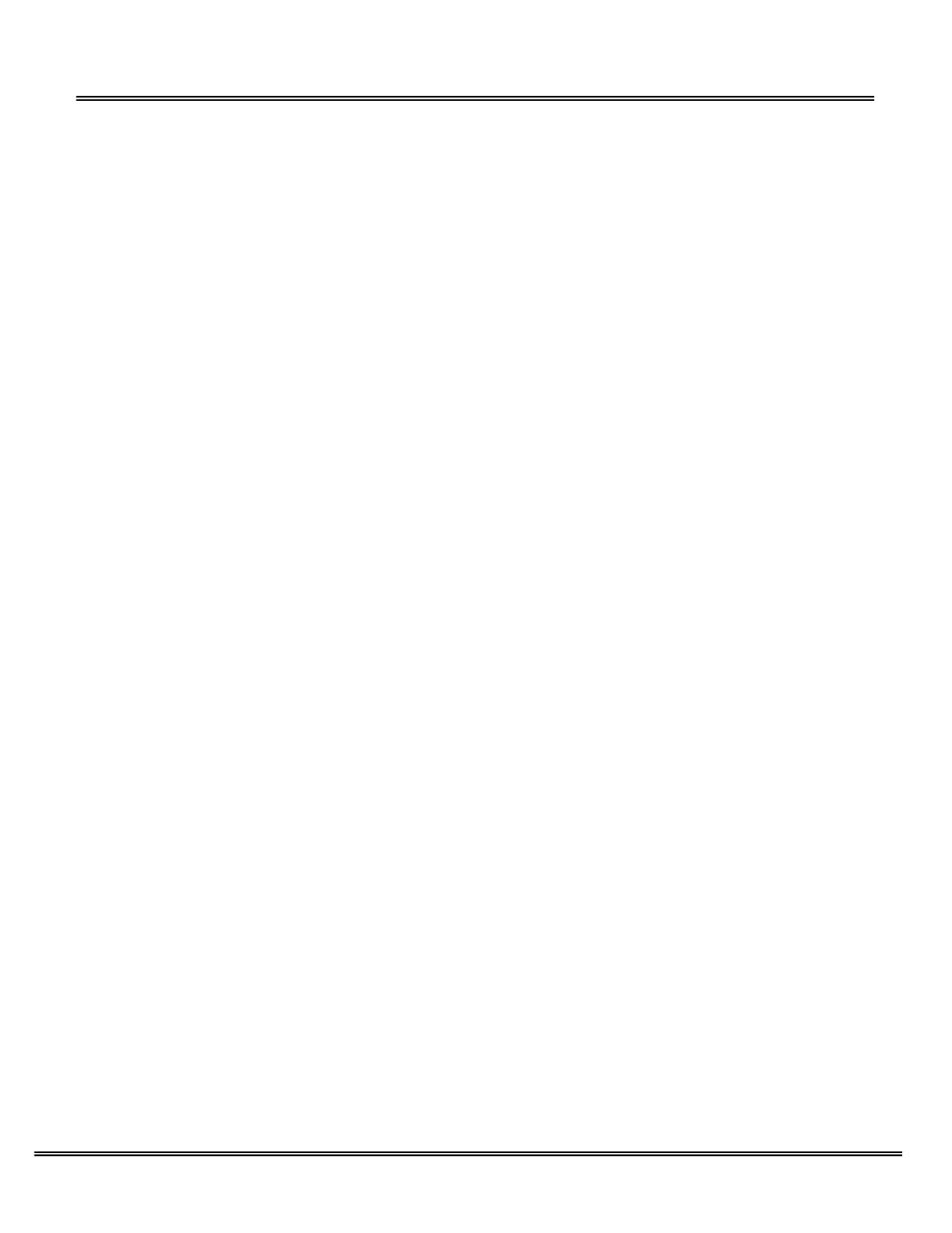
Advanced Instruments Inc.
43
Sampling
Process oxygen analyzers require positive pressure to flow the sample gas by the sensor to measure the oxygen concentration
in a sample gas. See Pressure & Flow under Installation in section 3 Safety Guidelines.
Generally, plastic tubing with a low permeability rating is adequate for most percentage measurements. However, to assure
optimal performance use gas lines of metal tubing, quality compression type fittings to minimize leaks.
The sample must be properly presented to the sensor to ensure an accurate measurement. In standard form the GPR-2600 is
designed with a flow meter upstream of the sensor that enables the user to control the flow rate.
Procedure:
Following calibration the analyzer returns to the SAMPLE mode after 30 seconds.
1. Select the desired sampling mode - auto or if manual, the range that provides maximum resolution – as described above.
2. Use the appropriate tubing to transport the sample gas to the analyzer.
3. The main consideration is to eliminate air leaks which can affect oxygen measurements above or below the 20.9% oxygen
concentration in ambient air - ensure the sample gas tubing connections fit tightly into the 1/8” male NPT to tube adapter,
and, the NPT end is taped and securely tightened into the mating male quick disconnect fittings which mate with the
female fittings on the analyzer
4. Assure there are no restrictions in the sample line.
5. For sample gases under positive pressure the user must provide a means of regulating the inlet pressure between 5-30 psig
and setting the flow rate of the sample gas at 2 SCFH (flow rates between .5 and 5 SCFH are acceptable).
6. For sample gases under atmospheric or slightly negative pressure an optional sampling pump is recommended to draw the
sample into the analyzer. Generally, no pressure regulation or flow control device is involved.
7. Caution: If the analyzer is equipped with an optional sampling pump and is intended for use in both positive and
atmospheric/slightly negative pressure applications where a flow meter valve is involved – ensure the valve is completely
open when operating the sampling pump. Refer to the Pressure & Flow section above.
8. Assure the sample is adequately vented for optimum response and recovery – and safety.
9. Allow the oxygen reading to stabilize for approximately 10 minutes at each sample point.
To avoid erroneous oxygen readings and damaging the sensor:
¾ Do not place your finger over the vent to test the flow indicator when gas is flowing to the sensor. Removing your finger
generates a vacuum on the sensor and may damage the sensor (voiding the sensor warranty).
¾ Assure there are no restrictions in the sample or vent lines
¾ Avoid drawing a vacuum that exceeds 14” of water column pressure – unless done gradually
¾ Avoid excessive flow rates above 5 SCFH.
¾ Avoid sudden releases of backpressure that can severely damage the sensor.
¾ Avoid the collection of particulates, liquids or condensation collect on the sensor that could block the diffusion of oxygen
into the sensor.
¾ If the analyzer is equipped with an optional integral sampling pump (positioned downstream of the sensor) and a flow
control metering valve (positioned upstream of the sensor), completely open the flow control metering valve to avoid
drawing a vacuum on the sensor and placing an undue burden on the pump.
Standby
The analyzer has no special storage requirements. The sensor should remain connected during storage periods. Store the
analyzer with the power OFF. If storing for an extended period of time protect the analyzer, cable and sensor from dust, heat
and moisture.