Ingalls 38545 User Manual
Ingalls
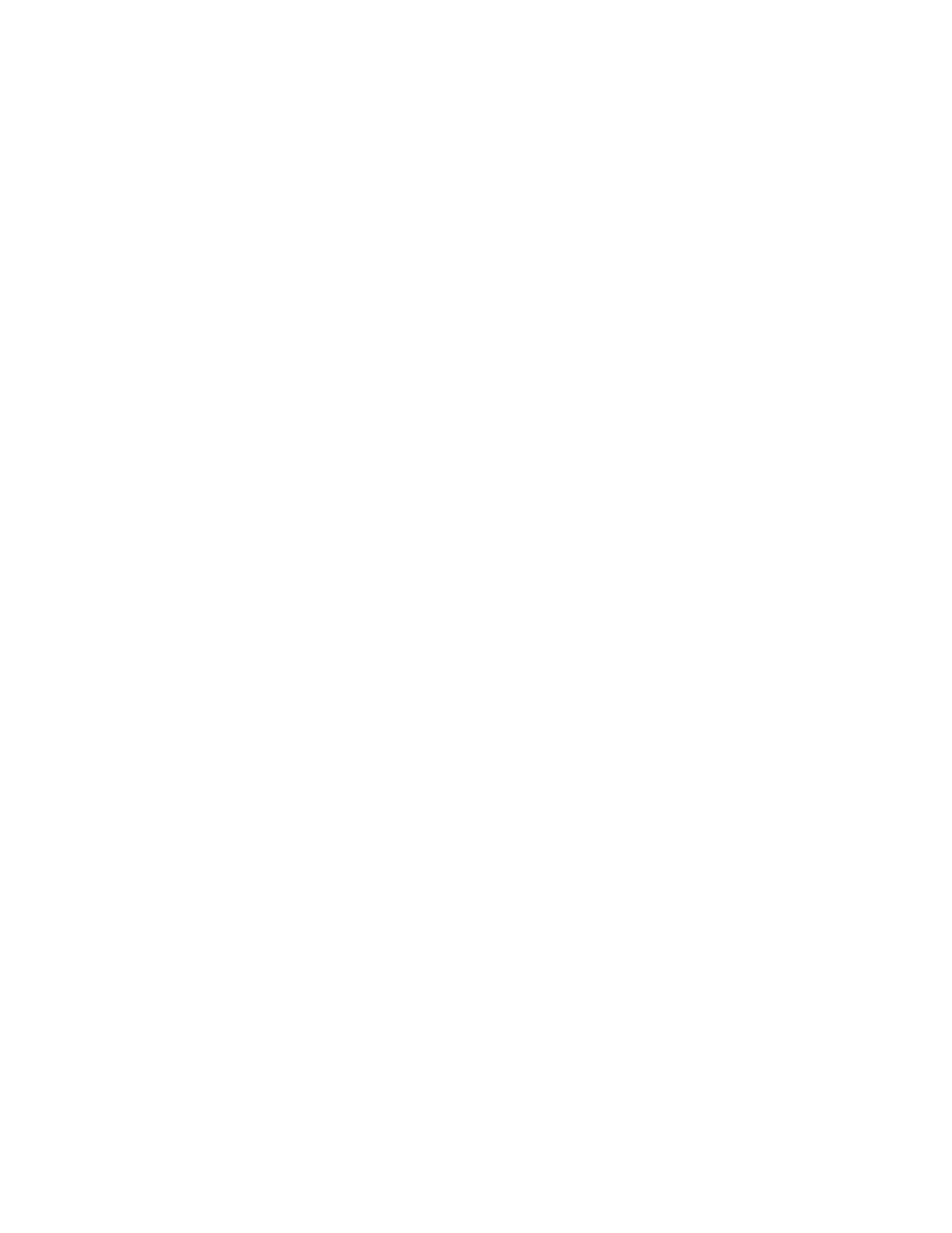
Ingalls
Product Installation Instructions
ING38545-062106
Part Number 38545
CAUTION: Observe proper safety and repair procedures for installation of all chassis parts. Some chassis parts require specialized tools and
experience and therefore MUST be installed by a qualified technician otherwise an unsafe vehicle and/or personal injury could result. Wear safety
glasses and other protection.
WARNING: Before beginning, check for any damaged or loose suspension connections. Loose connections here indicate worn or broken parts which
MUST BE REPLACED. Failure to replace a damaged or worn spindle and/or link may cause the wheel to separate from the vehicle, possibly resulting in
serious personal injury.
NOTE: These parts are intended for use in vehicles with abnormal alignment and are designed to replace the non-adjustable factory equipment. These
parts are not designed for installation on vehicles with suspension and/or steering systems modified for racing, competition or any other non-standard
purpose.
Instructions
1. Before starting alignment, complete inspection checklist and determine the amount of change needed.
2. Raise the rear of the vehicle and support body on jack stands in a safe manner. Remove rear tire and wheel assembly and
remove the clips holding the wire bundle on the forward lower OE support arm.
3. Restrain the spindle from excessive movement and remove the nut and bolt from the OE support arms at the spindle.
4. Remove the bolts from the inner end of both lower OE support arms near the rear differential unit and remove both OE arms.
5. The
SmartArm
TM
units consist of left (LH) and right (RH) hand threaded parts to form a turnbuckle arrangement. Match the LH end
of each tube (denoted by a groove just behind the wrench flats on one end) with the silver zinc plated jam nuts and the LH
threaded end pieces (denoted by the missing last thread on the end). Match the RH end of each tube (no groove) with the black
zinc plated jam nuts and the RH threaded end pieces.
6. For both arms, ensure both jam nuts are threaded all the way against their respective end pieces and thread each end piece into
its correct end of the center tube until the threads of each end piece are no longer visible. Note that there are two dimples on each
end piece that will indicate the minimum thread engagement allowable on this part.
7. With both SmartArm
TM
links now assembled, place the hex end of the shorter arm onto the forward mount of the spindle and insert
the long bolt through the bushing and into the spindle. Place the hex end of the longer arm onto the bolt at the aft mount of the
spindle and install the OE washer and nut but do not tighten at this time.
8. Install the other ends of both SmartArm
TM
links (keeping them parallel) into the body mounting brackets using the OE bolts and
nuts but do not tighten at this time.
9. Replace the tire and wheel assembly and lower the vehicle so the weight is on the wheels. Torque the nuts at the body mounting
bracket to 103 ft-lbs (140 N-m). Torque the nut and bolt at the spindle to 110 ft-lbs (150 N-m).
10. Adjust the wheel camber first by turning both center tubes to contract (for positive camber) or expand (for negative camber) until
the desired camber is achieved. Adjust both center tubes in and out as needed to set toe. Recheck camber. When expanding the
SmartArm
TM
, ensure that the end link dimples are not visible outside the center tube. DO NOT exceed the minimum allowable
thread engagement or damage to the part/vehicle/occupants may occur. Check for suspension clearance (see note below).
11. Place a wrench on the center tube hex and tighten the jam nuts against the center tube. Torque to 80 ft. lbs (108 N.M.) and verify
camber and toe readings.
12. Using included wire ties attach cables to the forward arms. Road test vehicle and make modifications as necessary.
ALWAYS CHECK FOR SUSPENSION CLEARANCE
Modifying any suspension component may change other part clearances and cause binding or interferences. After installing any Ingalls’ product, the
suspension must be checked for binds or interference between all components, other arms and the chassis. Be sure that all control arms, struts and
steering ends move freely through the full movement of the suspension (springs may need to be removed to fully check component travel). Installing
any Ingalls’ product on a modified vehicle (lowered or raised) from the original factory design requires a detailed check of all suspension components
and their movements. Ingalls recommends that a trained technician install all products.
Limited Warranty
Subject to Disclaimer. All Ingalls products are warranted against defects in materials and workmanship for ninety (90) days from date of purchase.
During the warranty period, Ingalls will repair, or at its option replace at no charge, components that prove to be defective. The product must be
returned, shipping prepaid, to Ingalls facility. This limited warranty does not apply if the product is damaged by accident or misuse. The foregoing
warranty is in lieu of all other warranties expressed or implied including but not limited to any implied warranty of merchantability, fitness, or adequacy for
any particular purpose or use. Ingalls shall not be liable for any special, incidental or consequential damages whether in contract, tort, or otherwise
resulting from the use or the inability to use the product.
Warranty Disclaimer
Use of this product in competition, or use on vehicles altered from original manufacturer’s specifications or settings, EXPRESSLY VOIDS WARRANTY.
The user is urged to inspect for suspension binding or interference when the product is used in these manners. However, due to the varying conditions
and manner of use which the product will be subjected to in such uses, Ingalls Engineering Co., Inc. makes no warranties, either express or implied,
including any warranty of merchantability or fitness for a particular purpose for use in competition or with specifications or settings other than those
specified by the original manufacturer’s specifications.
Copyright
©
2006 Ingalls Engineering Co., Inc.